Keywords
|
Hybrid Electric Vehicles, Bidirectional DC-DC converter, Flyback Snubber, RCD Snubber, Active Clamp Snubber |
INTRODUCTION
|
Electric vehicles, Hybrid Electric Vehicles have been typically proposed to replace conventional vehicles in the near future. The inherent flexibility of Hybrid Electric Vehicles makes them suited for personal transportation and military applications. The major components are battery, engine, electric motor which also can work as generator and power electronic equipment. Hybrid Electric Vehicle combines the benefits of engine and electric motor to provide improved fuel economy. Engine provides most of the vehicle’s power and the additional power is provided by the motor when needed such as for accelerating and passing. The electric power for the motor is generated from regenerative braking and from the engine, so Hybrid Electric vehicle don’t have to be “plugged” into an electric outlet to recharge [4]. Batteries in a Hybrid Electric Vehicle are usually required to backup power for power. Their voltage levels are typically much lower than dc bus voltage. Some converters are only suitable for stepping up or stepping down the voltage. Bidirectional converter is used for both stepping up and stepping down the voltage. Bidirectional converters for charging/discharging the batteries are therefore required. |
In Fig.1, the left hand side is a low voltage side and right hand side is a high voltage side. Low voltage side consists of battery and current fed full bridge and high voltage side consist of voltage fed full bridge. Low voltage side and high voltage side is separated by an isolation transformer with turns ratio, 1:n. Inductor, Lm acts as boost inductor when power flows from the low voltage side to high voltage side, which is described by boost mode of operation. On the other hand, inductor, Lmperforms output filtering, when power flows from high voltage to low voltage side, which is described by buck operation. But in the main circuit there occurs over voltage and over current stress which can be reduced by the snubber circuits [1]. |
The transformer with a current fed full bridge lead to high voltage spike and high current stress across the switches because of the leakage inductance of the transformer. So a snubber circuit is needed to limit the voltage spike and current stress. Snubber circuits used in bidirectional converter are:- |
a) RCD Snubber |
b) Active Clamping snubber |
c) Flyback Snubber |
In RCD snubber, there is power dissipation on the resistor, which results in lower efficiency and is not used for high power operations.Active snubber switches at twice the switching frequency, so the burden of high current stress and associated thermal issues of the active switches and the capacitor add the limitations. Flyback converter together with clamping diode and clamping capacitor forms the flyback snubber thereby we can reduce the current flowing through the active switches[7]. |
The objective of the paper is to compare bidirectional DC-DC converter with RCD, active clamp and flyback snubber. From the comparison, to prove that flyback snubber in the bidirectional converter is better to reduce the current stress and voltage spikes of the active switches.The Section I give the Introduction of the bidirectional converter for hybrid electric vehicle. Section II is helpful to understand the background of related work. Section III explains the simulations and its results and the lastsection IV concludes the paper and followed by the references. |
CIRCUIT DESCRIPTION
|
The proposed isolated bidirectional full-bridge DC–DC converter with a flyback snubber is shown in Fig. 2. The converter is operated with two modes which are buck mode and boost mode. Fig.2 consists of a current-fed switch bridge, a flyback snubber at the low-voltage side, and a voltage-fed bridge at the high-voltage side. Inductor Lmperforms output filtering when power flows from the high-voltage side to the batteries, which is denoted as a buck mode. On the other hand, it works in boost mode when power is transferred from the batteries to the high-voltage side. |
The clamp branch capacitor CC and diode DCare used to absorb the current difference between current-fed inductor Lmand leakage inductance Llland Llhof isolation transformer Txduring switching commutation. The flyback snubber can be independently controlled to regulate VCto the desired value, which is just slightly higher than VAB. Thus, the voltage stress of switchesM1–M4 can be limitedto a low level.A bidirectional DC-DC converter has two types of conversions: step-up conversion (boost mode) and step-down conversion (buck mode). In boost mode, switches M1–M4 are controlled,and the body diodes of switches M5–M8are used as a rectifier. In buck mode, switches M5–M8 are controlled, and thebody diodes of switches M1–M4 operate as a rectifier. |
A. STEP UP OPERATION |
First of all switches M1-M4 are turned on, so the primary side of the transformer is short circuited and therefore VAB=0. Inductor, L is charged by the battery. At t1, M1& M4 remain conducting, so VAB is present. Clamping diode, Dc continues to conduct until the current difference drops top zero at t2. Moreover D5 and D8 are conducting to transfer the power. During this interval (iL-iP) flows into clamping capacitor. So clamp capacitor voltage, VC is rising at the interval t1-t2 and ip= iL condition is reached. During t2 -t3, Dc stops conduction and flyback snubber starts to operate. Cc is discharging and the flyback switch is turned on and the energy is stored in flyback snubber as flux. In the interval t3-t4 energy stored in the inductor is transferred to high voltage side. Over this interval, flyback snubber will operate independently to regulate VC to VC(R). Energy stored in the transformer of the flyback snubber is transferred to the output when flyback switch turns off.At t4, Vc has been regulated to VC(R) and the snubber remains idle. Over this interval the main power stage is still transferring power from low voltage to high voltage side. It stops at t5 and completes a half switchingcycle operation. |
B. STEP DOWN OPERATION |
During the time period t0-t1, switches M5 and M8 are on, while switches M6 and M7 are in the off state. High side voltage is immediately exerted on the transformer and the whole voltage is exerted on the transformer causing current to rise. With transformer current, is increasing linearly towards the load current at t1, switches, M1 and M4 are conducting to transfer the power and the voltage across the transformer terminals on the current fed side changes immediately to reflect the voltage from the voltage fed side. |
At t1, switch M8 remain conducting, while switch M5 is turned off. Diode, D6 starts to conduct the freewheeling leakage current. Transformer current reaches the load current level at t1 and starts to decrease during the interval t1-t2 and voltage VAB starts to decrease. The clamping diode, Dc starts to conduct during this interval. |
At t2, with diode, D6 conducting, switch, M6 can be turned on under ZVS. At t3, switch M6 remains conducting, while switch, M8 is turned off. Diode, D7 then starts to conduct the freewheeling leakage current. |
At t4, with the diode, D7 conducting, switch M7 can be turned on under ZVS. Over this interval, the active switches change to the other pair of diagonal switches and the voltage on the transformer reverse its polarity to balance the flux and to alleviate the transient voltage problem. It stops at t5 and completes a half switchingcycle operation. |
An isolated bidirectional full bridge DC-DC converter transformer converter had voltage spikes due to the current difference between the current fed inductor and leakage inductance of the isolation transformer. This voltage spike has been alleviated by the flyback snubber. The flyback snubber can be controlled to attain a soft start-up feature. The current stress is reduced under heavy load conditions. This converter has also the advantage of increased reliability and efficiency. |
SIMULATIONS
|
The simulation of the proposed paper is carried out using MATLAB software. The closed loop simulation of buck mode and boost mode is done separately. For closed loop simulation, a voltage and current feedback circuit is considered. The isolated bidirectional DC-DC full bridge converter with RCD snubber, active clamp snubber flyback snubber is simulated. The hybrid electric vehicles using isolated bidirectional DC-DC converter with a flyback snubber is also simulated. |
We obtain an output voltage of 381.2V for open loop bidirectional full bridge DC-DC converter without flyback snubber. |
We obtain a speed of 58.1rad/sec for of bidirectional full bridge DC-DC converter with flyback snubber- Boost open loop operation. |
The simulation results of open loop and closed loop control of isolated bidirectional DC-DC converter with and without flyback snubber for various loads are done. DC motor as a load is used for the simulation in hybrid vehicle application. The input 230V is stepped down to 15v using a step-down transformer and it is rectified to dc by the bridge rectifier. In boost mode, the output of the rectifier is boosted by a step-up transformer of ratio 12:230. The output is converter into ac by an inverter. The load used is a resistive load of rating 1K, 10W. Fig.23 shows the photograph of the prototype converter. |
CONCLUSION
|
The bidirectional DC-DC converter with flyback snubber is proposed for hybrid electric vehicles. Compared to RCD and Active clamp snubber, flyback snubber for converter provides the better efficiency. Simulations and experimental setup are described in this paper. |
ACKNOWLEDGMENT
|
The authors acknowledge gratefully for the support of Electrical and Electronics Department of AmalJyothi college of Engineering, Kanjirappilly. |
Figures at a glance
|
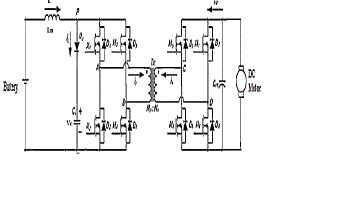 |
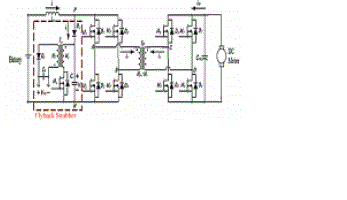 |
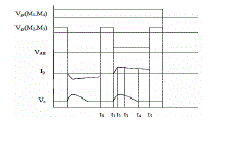 |
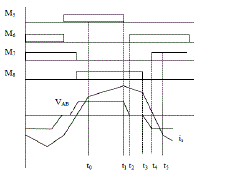 |
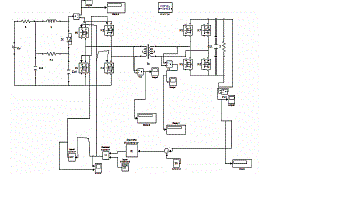 |
Figure 1 |
Figure 2 |
Figure 3 |
Figure 4 |
Figure 5 |
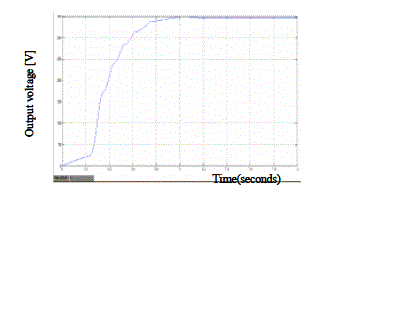 |
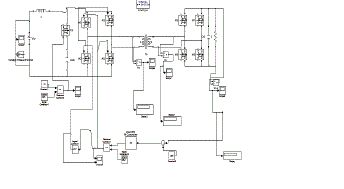 |
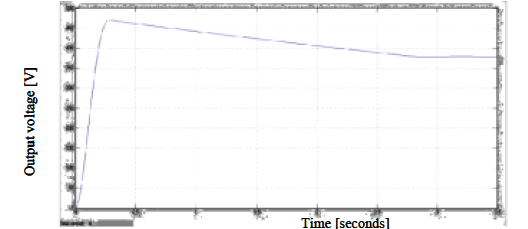 |
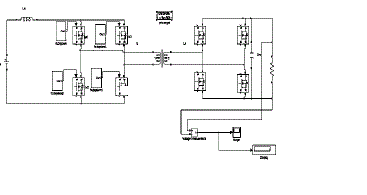 |
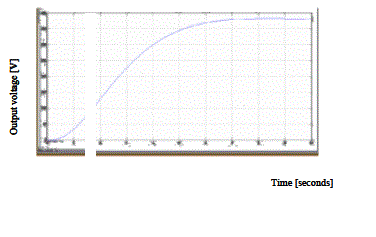 |
Figure 6 |
Figure 7 |
Figure 8 |
Figure 9 |
Figure 10 |
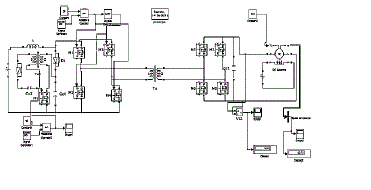 |
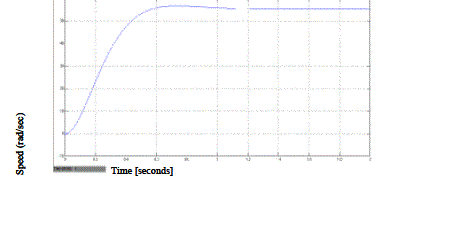 |
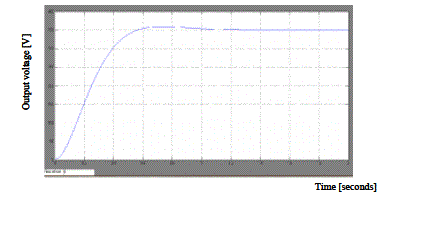 |
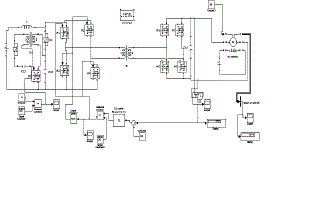 |
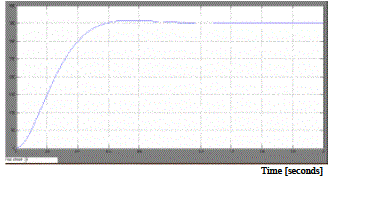 |
Figure 11 |
Figure 12 |
Figure 13 |
Figure 14 |
Figure 15 |
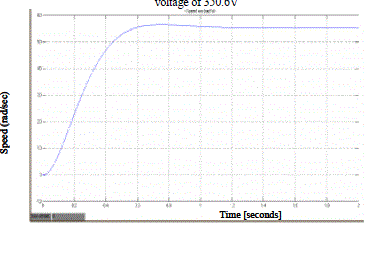 |
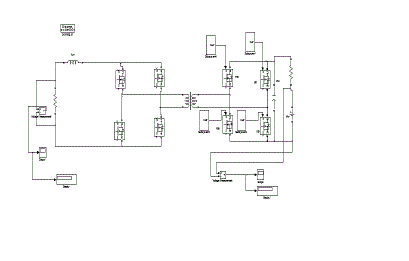 |
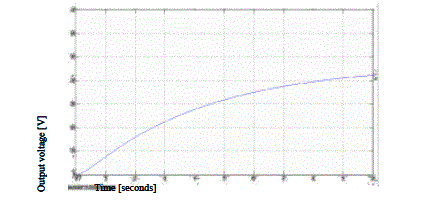 |
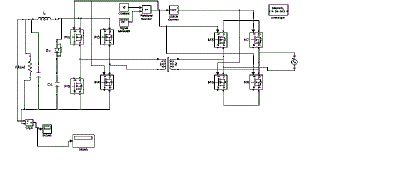 |
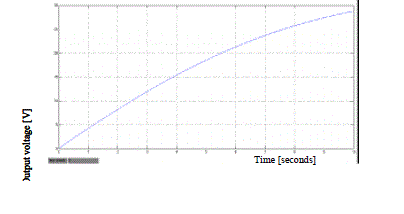 |
Figure 16 |
Figure 17 |
Figure 18 |
Figure 19 |
Figure 20 |
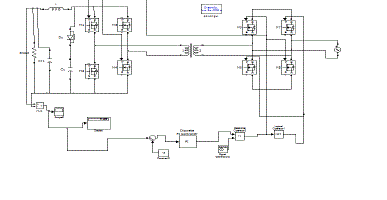 |
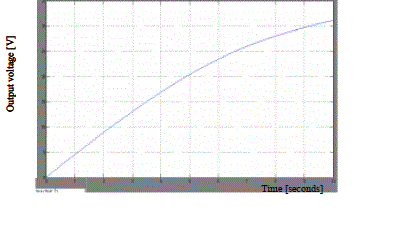 |
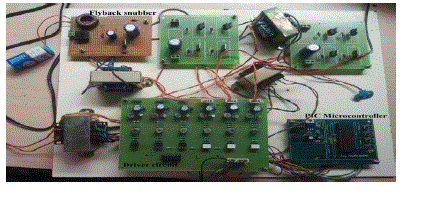 |
Figure 21 |
Figure 22 |
Figure 23 |
|
References
|
- T. Wu,, Y. Chu Chen, J. Yang, and C. Kuo, “Isolated Bidirectional Full-Bridge DC–DC Converter With a FlybackSnubber”, IEEE Transactions Power Electronics,Vol.23, pp 1915-1922, 2010.
- X. D. Xue, K. W. E. Cheng, and N. C. Cheung, “Selection of Electric Motor Drives for Electric Vehicles” Australasian Universities Power Engineering Conference (AUPEC'08),Vol.56, pp198-208, 2008.
- K.Wang, F.C. Lee, and J.Lai “Operation principles of bi-directional full-bridge DC-DC converter with unified soft-switching scheme and soft-starting capability” International Journal of Engineering Science and Technology (IJEST), Vol. 3, pp 167-174, 2011.
- M. Rafiq, M. F. Hasan “Design and Analysis of 60 kW DC-DC Converter for Hybrid Electric Vehicle Applications”.”, IEEE Transactions Power Electronics, vol. 39, pp. 1881-1886, March 2010.
- P.Pany, R.K. Singh, R.K. Tripathi , “Bidirectional DC-DC converter fed drive for electric vehicle system” International Journal of Engineering, Science and Technology, Vol. 3, No. 3, pp. 101-110,2011.
- O. García, L.A. Flores, J.A. Oliver, J.A Cobos, and J. de la Pena, ‘Bi-directional dc-dc converter for hybrid vehicles”, IEEE Transactions Power Electronics, vol. 27, no. 3, pp. 1881-1886, 2005.
- T. Bhattacharya, V. S. Giri, K. Mathew, and L. Umanand, “Multiphase Bidirectional Flyback Converter Topology for Hybrid Electric Vehicles”, IEEE Transactions Industrial Electronics, vol. 56, no. 1, pp. 78-84, 2009.
- O. C. Onar and A. Khaligh,” A Novel Integrated Magnetic Structure Based DC/DC converter for Hybrid Battery/Ultracapacitor Energy Storage Systems”, IEEE Transactions on SMART GRID, vol. 3, no. 1,pp. 296-307, 2012.
|