Keywords
|
Single-Phase Capacitor-Run induction motor, rotor geometry, copper die-cast rotor technology. |
INTRODUCTION
|
The single phase induction motor is used extensively by all the industrial, residential and commercial solicitations in the present day and we need to develop extraordinary efficiency induction motor [1]. The admiration of Capacitor -Run induction motor is due to the simplicity of its rotor, which is made of laminated steel and cast aluminium. The basic ladders for rotor cage production are laminates piercing, bluing of laminates in furnace, stack assembling, casting, machining finish and finally the rotor galvanizing. However, despite of its effortlessness, the rotor plays an imperative role in motor performance. Crucial performance deviations in motors usually come from the rotor and this is more discernible in small motors [2]. |
Capacitor-Run Motors (CRMs) are extensively used in fields where there are no three-phase lines (domestic and agricultural) and in low-powered loads. Many zones have only single-phase power, which means that a hefty number of single phase motors is used. In such cases, it is important to diminish the energy ingestion by enhancing the performance of these motors [3]. A single-phase induction motor has been one of the most widely used motors in home employments, not only because it has a modest structure without a controller, but also because it is one of the inexpensive motors [4]. However, Capacitor-Run Induction Motor has deprived starting enactment like starting torque but has good running performance. Nowadays, the utmost efficiency of a single-phase induction motor with 1-KW output is less than 90% and an efficiency increase even of 1 or 2% has a crucial effect on the performance of home appliances, as well as on energy savings worldwide [4]. |
The optimal design of classical induction motors with respect to the electromagnetic torque must answer two contradictory requirements, respectively high value of starting torque and high value of breakdown torque. In case of Single-Phase Capacitor-Run induction motor, these characteristics are very dependent on the rotor slot geometry [5]. Many researches have been done to improve the starting performance of the capacitor-run motor as well as the efficiency and torque performance. In this review paper, the influence of rotor geometry like rotor slot type & shape, number of rotor slot on the efficiency, torque performance and electromagnetic noise has been discussed. |
LITERATURE REVIEW
|
The recent work carried out in the area of improvement of efficiency of the machine is led to the investigation of parameters affecting the losses.Various parameters for improving the efficiency are shown in fig. 1 [6]. |
It is critical to make comparison of motor efficiency using uniform product testing technology. There is no single standard test for investigating the efficiency. The various efficiency standards available over the world are: |
• IEEE 112-1984 (USA) |
• EPAct-USA 1992 |
• IEC 34-2 (Europe) |
• JEC-37 (Japan) |
• BS-269 (British) |
• C-390 (Canada) |
• Is 4889 (India) |
This paper provides the overview for different efficiency standards and research work carried out in the past for the improvement of efficiency of the induction motor. |
A)Motor Efficiency Assessment and Standards
|
Various standards of motor efficiency are established by countries all over the world to set minimum efficiency level of electric motors. There is no single standard method that will set same level of minimum efficiency. In 1992 Energy Policy act (EPAct) in united states authorized the Department of Energy to set up minimum efficiency standards in USA . 2-3% improvement in the efficiency of electric motor was recorded. NEMA –standards of energy efficient motor set up higher level of efficiency in 1994 without effecting torque and this also satisfied Standard of International Electro-Technical Committee .NEMA in 2001 announced NEMA PremiumTM efficiency in which the motors have 20% less losses as compared to EPAct-motors. The European Union and Committee of European Manufacturers Electrical Machines and Electronics has established classification of motors on the basis of efficiency level in which three phase squirrel cage motors ranging from 1.1 to 90 KW with 2 pole and 4 pole categorized In the classification the motors are designated as EFF1 for highest efficiency and EFF2 for standard efficiency. Indian Electrical and Electronics Manufacturers Association (IEEMA) set up standards IEEMA-19:2000 on the basis of which the Bureau of Indian Standards developed IS: 129615-2004 [6]. The efficiency of motor tested under various norms is not same. Table-I presented for full load efficiency test of 7.5hp motor using common global standards [7]. |
EFFECTS OF ROTOR GEOMETRY
|
In recent few years many researchers have evaluated the description of Induction Motor by the rotor geometry. Rotor geometry plays an inestimable provision in the performance of Single-Phase Induction Motor. The rotor geometry like as rotor slots opening and closing, rotor slot design, rotor slot shape, rotor core material, rotor winding etc. has very imperative role in the performance perfection in SPIM. The impacts of slot shape, slot configuration, rotor material are discussed further. |
A) Influence of slot opening |
Gun Hee Jang and S. J. Park [4] investigated the effects of slot opening on the performance of the single phase induction motor using Finite Element Methods and Maxwell Stress Tensor. They perceived that the torque is twisted in the locality of slot opening because of the incidence of revolving magnetic field.The author designed the stator with provisions of different slot opening and slot closure to minimize theeffect ofnegative torque and tactic is made obtain sophisticated efficiency of the motor under test. |
The Single-Phase Induction Motor of output rating 0.79KW with number of stator/rotor slots 24/33 shown in Fig.2 has been replicated. When the slot opening diminished from 2.1 mm to 1.5 mm, there is reduction in the current and power of the single phase induction motor for generating same torque and the efficiency improvement up to 1.3% has been achieved [4]. |
B) Effects of slot configuration |
The slot configuration plays a crucial role in the performance of SPIM. Various research works has been carried out to improve the performance of the motor. Zhou Rui et al [9] have designed a model of Single-Phase Capacitor-Run Induction Motor with the help of Maxwell 2D software. The author changed the slot shape and analysed the results after optimization. It has been investigated that the torque and efficiency improved by optimized the slot shape. Two models of SPIM i.e. YDL13-2 & YDL092-2 have been taken and changed the slot dimensions of rotor. The slot dimensions of both models are shown in Fig. 3. After changing the slot dimensions, the author simulated the proposed model in Maxwell 2D. The original design of both models is shown in table II and the results after slot dimensions optimization are shown in table III. |
Compared with the table II, the torque performance of YDL 13-2 is improved observably and the efficiency is inclined marginally, it is acceptable because the efficiency of the original design is adequate. Similarly, the original design of YDL092-2 has a high torque, but the maximum torque and start torque are deranged, optimization of this project focus on raising the start performance and efficiency. In addition, because the rotor slot area is increased, there is a convinced rise of start current ratio [9].S. Sobhani et al [10] also changed the dimensions of rotor slots. The author has taken two models of Single-Phase Capacitor-Run Induction Motor i.e. SOB-1 & SOB-2. The author simulated the original models in Maxwell 2D and scrutinized the results as shown in table IV. The optimized slot dimension is shown in Fig. 4. After slot dimensions optimization the results are shown in table V. The results are paralleled with each other and the author analysed the results. |
On comparison of these results with original performance of the motor, the author analysed that Mechanical shaft Torque is increased in both models. The efficiency has been improved. Thus it can be conclude by this work that the rotor slot geometry has implausible sustenance in the performance of the Single-Phase Capacitor-Run Induction Motor [10].Subhasis Nandi [11] investigated the effect of slot permeance on the creation of RSH (Rotor slot harmonics). The explicit slot permeance variation due to stator and rotor slots is another major contributor to RSH generation. They can be described as in (1), with ωr, the rotor speed in radians per second, |
Psp = Ps cos (Sx) + Pr cos {R(x - ωrt)} + Prsd cos {(S-R)x + Rωrt} + Prss cos {(S+R)x - Rωrt} + …….. (1) |
They interrelate with the resultant of stator and rotor MMF to generate components. Variations due to other slot permeance components may also result in RSH generation. It was demonstrated that, at least for a particular class of machines, |
1) The production of the RSH is chiefly influenced by slot MMF rather than the slot permeance. |
2) With no constructional deficiencies and supply unbalance only one principal RSH may be detectable theoretically. |
3) Other major RSH is caused by reverse rotating field allied with the negative-sequence component of current [11]. |
However, by the experimental results the author has seen that the second principal harmonic is indeed noticeable under normal operating conditions. |
Negoita et al. [12] have presented the differences between a motor with no oddness and the same motor with 15% static oddness in terms of the amplitude and frequency spectrum of the magnetic forces generated. The author has taken a 0.75 kW, 1500 rpm, 4 pole squirrel-cage induction motor with 24 stator slots and 30 rotor slots and modelled in FLUX 2D. Two different models were created in FLUX 2D, one for the motor with no oddness and one for a motor with a 15% static oddness level. The author concluded that rotor oddness leads to a drastic increase of the magnetic force amplitude and force amplitude increases with the increase in capacitor value. |
C) Effects of core material of the rotor |
The core material has an apparent influence on the performance of single-phase capacitor-run induction motor. The material of rotor of the machine plays a strategic role in the improvement of efficiency and torque developed by the induction motor. Researches in the past have investigated various types of material and their effect on the motor performance. |
Zhou Rui et al. [9] have designed the optimal model with the choice of core material using the package of Rmxprt in MAXWELL 2D based on two single-phase induction motors, YDL13-2 and YDL092-2.YDL13-2 and YDL092-2 are both Split-Phase capacitor-run single-phase induction motor.The performance of the original design is calculated byRmxprt as Table VI [9]. |
The original design used the D23 as the stator and rotor materials. The author has taken DW465 as rotor and stator material. The RMXPRT software chooses capacitor routinely on the goal of minimum anti-magnetic potential. In the following design, all the capacitances are the optimal value preferred by software. After changing the stator and rotor materials, the results are calculated as Table VII [9]. |
On comparing the results of with original design as in Table VI, the efficiency and power factor increase, torque performances worsened as iron-loss reduced. |
S. Sobhani et al. [10] also worked to improve the performance of the motor by changing the core material. In original design of the engine, the D23 was used for the stator and rotor. The author has taken DW465 as core material and simulates the model in Maxwell 2D software. After changing the stator and rotor materials in SOB-1 and SOB-2, the results are calculated as Table VIII. The results show improvements in performance and torque. |
As can be seen, in SOB-1 the efficiency is improved from 37% to 43% and Torque improved from 2.31 to 2.51. This increment has a significant role in this investigation. |
Thus the core material has important protagonist in improvement of the Single-Phase Capacitor-Run Induction Motor. |
EFFECT ON MAGNETIC FIELD AND SLOT RIPPLES
|
Ke Zhang et al [12] have inspected the magnetic potential of slot ripples and the torque formed by magnetic field harmonics introduced by stator and rotor slot geometry. The proposed work was partially supported by various agencies in China. The degree of harmonics in magnetic field inside the machine is the functions of magnetic potential of slot ripples which in turn depend upon the stator rotor slot opening. This magnetic field is main factor of generating harmonics torque in the electric motor. The author calculated the degree of oscillation of magnetic field in all the three slots. The results are shown in Table IX. The ripple component is 0.52T in trapezoidal slots and is 0.46T in pear shaped slots. The effect of higher harmonic is observable in the performance of asynchronous machine. |
The simple substitution of Aluminium by copper in rotor bars displays significant improvement in efficiency. The resistivity of copper at 20oC is 10.4Ω/foot and that of Aluminium is 16Ω/foot. Author [17] calculated that for same current drawn with copper bars there is reduction in rotor copper losses by 35.4% as compared to aluminium. Die cast copper rotor technology in motor started in 1997 and rapidly grow due to advantages of performance, energy savings and environment [18]. Mark Hodowanec et al [19] have designed four types of rotors namely Aluminium die cast (ADC), Copper die cast rotor (CuDC), fabricated aluminium bars (AlBar) and fabricated Cu bars (CuBar). Out of these performance-wise CuBar provides best results, but the fabrication cost is higher side. The problem of higher temperature and pressures in comparison to Aluminium has been solved by using Ni-based alloy die [18] and Petters, D. T. et al [18] developed high pressure die cast and resolved the problem of porosity. Lie et al [20] has analysed the enrichment in efficiency by using copper die cast rotor. The overall rotor losses of 46% in 3KW induction motor are recorded. Economic consideration and performance improvement presented by Jown G. Cowieet at [21] and Poloujadoff et al [22] prepared economic comparisons between die cast aluminium and die cast copper. Initial cost higher side by about 30% on the other hand 7 to 8 times savings in running price recovered. |
SPIM WITH EXTERNAL ROTOR
|
M.Popescu [23] has presented an external rotor single-phase induction motor, in which short-circuiting trinkets can be thrust by a conducting shell linking two rings, which recovers cooling and operating appearances. New equivalent circuits of the rotor with conducting shell between the rings and the lumped parameters have been established. The author has derived an equivalent circuit for analysis and modelling of the single-phase induction motor with external rotor incorporating iron loss and saturation effects. The detailed control strategy can be readily implemented for standard single-phase or two-phase induction machine. |
The author investigated that in single-phase induction machines with external rotor the shunting effect can be very important: |
1. Electromagnetic rated torque is increased throughdecreasing the rotor resistance and impedance. |
2. Pulsating loads for different frequencies can be avoidedby using increased rotor inertia. |
3. Fast start-up speed response with minimized oscillations. |
ROTOR BARS DIAGNOSIS
|
Mariana et al. [24] analysed the vibration and current spectrum of an induction motor in order to achieve information for the detection of rotor bars faults. The author used a specialized system to measure the noise and vibration with regard to electric motor judgment. The author has observed significant vibration and current spectrum differences between healthy motors and motors whose rotor bars are broken. The frequency spectral analysis of vibration and current provides a method to detect broken rotor bars faults. The developed system has scalable to power ratings and it has been successfully verified with 0.65 kW single phase induction motor data. |
By the corresponding zoom the author [24] observed that vibration and stator current it is different at the “healthy” motor related fault motor. |
CONCLUSION
|
The importance of efficiency and race to improve it remains the important factor for the researchers and the work carried out in this direction in the past played a key role in saving the resources. Number of designs has been proposed by exploring design parameters for achieving optimized performance. Both stator and rotor geometries of the machine has immense influence on the performance. Improvement in stator & rotor slot configuration, magnetic properties of the core material and consequence of air-gap variation has been analysed using various techniques and software. Most of the magnetic field analysis work has been carried out using FEMM (Finite Element Method Magnetics), Maxwell etc. The rotor bar parameters evaluation and use of combined rotor winding materials with suitable composition analysis will provide new height of augmentation of performance. |
Tables at a glance
|
 |
 |
 |
 |
 |
Table 1 |
Table 2 |
Table 3 |
Table 4 |
Table 5 |
 |
 |
 |
 |
Table 6 |
Table 7 |
Table 8 |
Table 9 |
|
|
Figures at a glance
|
 |
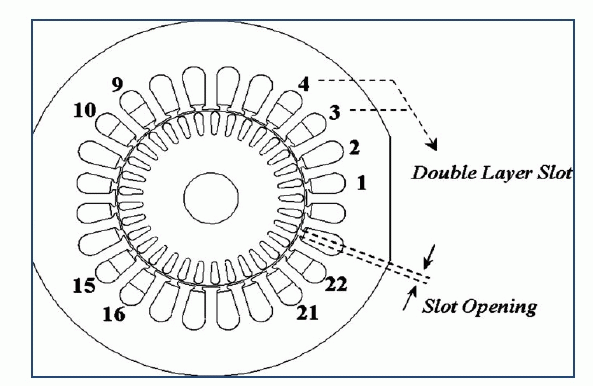 |
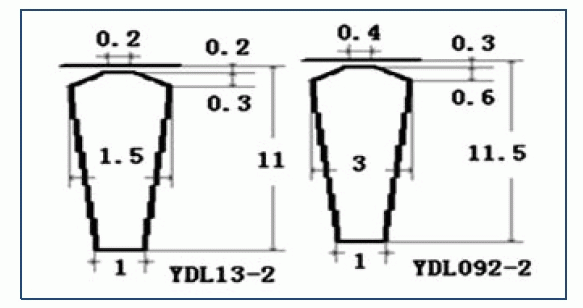 |
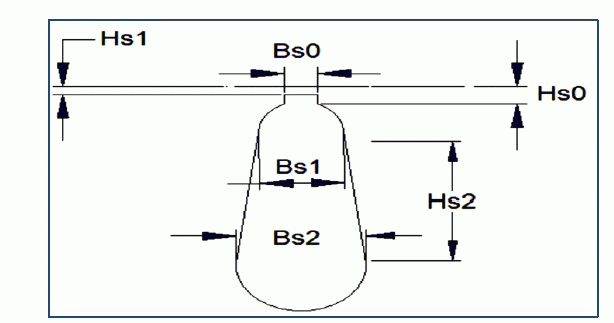 |
Figure 1 |
Figure 2 |
Figure 3 |
Figure 4 |
|
|
References
|
- Kwangsoo Kim, Seung-Bin Lim and Ju Lee, “Design of Rotor Slot of Single-Phase Induction Motor with Copper Die-Cast Rotor Cage forHigh Efficiency,” International Telecommunications Energy Conference (INTELEC), pp. 1-4, 2009.
- Claudia A. da Silva, Alvaro B. Dietrich and Renato Lopes, “Rotor Cage of Single-Phase Induction Motors - Process Analysis,” Electric Machines and Drives Conference (IEMDC '09), pp. 1469-1473, 2009.
- M.S. Alshamasin, “Optimization of the Performance of Single-Phase Capacitor-Run Induction Motor,” American Journal of Applied Sciences,pp. 745-751, 2009.
- Gun Hee Jang and S. J. Park, “Characterization of a Single-Phase Induction Motor Due to the Effect of Slot Opening,” IEEE Transactions onmagnetics, Vol. 40, No. 4, pp. 2065-2067, july 2004.
- V. Fireteanu, T. Tudorache and O.A. Turcanu, “Optimal Design of Rotor Slot Geometry of Squirrel-Cage Type Induction Motors,” International conference onElectric machines & drives conference (IEMDC), pp. 537-542, 2007.
- Subramanian Manoharan et al, “Review on efficiency improvement in squirrel cage induction motor by using DCR technologyâÃâ¬Ãâ” Journal ofElectrical Engineering, 2009, Vol. 60, No. 40, pp. 227-236.
- Gilbert A. McCoy, Todd Litman and John G. Dounglass âÃâ¬Ãâ¢Energy efficient electric motorâÃâ¬Ãâ Washington State Energy Office Olympia, Washington, 1993.Revision 3.
- K. J. Park, Kwangsoo Kim, Sang-Hoon Lee, Dae-Hyun Koo, Kwang-CheolKo and Ju Lee , “Optimal Design of Rotor Slot of Three-PhaseInduction Motor with Die-Cast Copper Rotor Cage,” International conference on Electrical machines and Systems (ICEMS), pp. 61-63, 2009.
- Zhou Rui, Wang Qunjing, Li Guoli, Pang Cong and Fang Guanghui, “Optimal Design of Single-Phase Induction Motor Based on MAXWELL2D Rmxprt,” International conference on Electrical machines and Systems (ICEMS), pp. 1367 – 1370, 2010.
- SobhanSobhani, Hamid Yaghobi and Mehdi Samakoosh, “Optimize Efficiency and Torque in the Single-Phase Induction Motor by Adjustingthe Design Parameters,” Environment and Electrical Engineering international conference (EEEIC), pp. 237 24, 2013.
- Subhasis Nandi, “Modeling of Induction Machines Including Stator and Rotor Slot Effects,” IEEE Transactions on industry applications, Vol.40, No. 4, pp. 1058-1065, July/August 2004.
- A. Negoita, G. Scutaru, I. Peter, R.M. Ionescu, O. Plesa and C. Nistor, “Influence of rotor static eccentricity on the noise level of a single phase squirrel cage induction motor,” International conference on Optimization of Electrical and Electronic Equipment (OPTIM), pp. 373- 378, 2012.
- Ke Zhang, Xuechen Jiang, Yuhou Wu, Lixiu Zhang and Xiaoping Wu, “Effect of Slot Shape in Rotor of Electrical Motor with High-SpeedSpindle on Slot Ripples,” Proceedings of the international Conference on Modeling, Identification and control, pp. 670-675, 2010.
- Dianhai Zhang, Chang Soon Park and Chang SeopKoh, “A New Optimal Design Method of Rotor Slot of Three-Phase Squirrel Cage Induction Motor for NEMA Class D Speed-Torque Characteristic using Multi-Objective Optimization Algorithm,” IEEE Transactions on Magnetics, Vol. 48, No. 2, pp. 879-882, February 2012.
- S. Williamson and C. I. Mcclay , “Optimization of the geometry of closed rotor slots for cage induction motors,” IEEE Trans. Ind. Appl., vol.32, no. 3, pp. 560–567, May 1996.
- A. Boglietti, A. Cavagnino, and M. Lazzari, “Computational algorithms for induction motor equivalent circuit parameter determination PartII: Skin effect and magnetizing characteristics,” IEEE Trans. Ind. Electron., Vol. 58, No. 9, pp. 3734–3740, Sept. 2011.
- Hsu, J. S.—Franco-Ferreira, E. A. , “Method of Manufacturing Squirrel Cage Rotors,” U.S. Patent NO. 6,088,906, July 18, 2000.
- Peters, D. T.—Cowie, J. G.—Brush, E. F. Jr.-, “Advantages of the Copper Rotor Motor – Performance, Energy Savings and Environmental,”Copper (Dr. Jean-Marie Welter, ed.), Pub-lished Online: 22 Oct 2007, Wiley-VCH Verlag GmbH & Co. KgaA, 2006.
- Finleyw. R. Hodowanec, M. M., “Selection of Copper versus Aluminum Rotors for Induction Motors,” IEEE Transactions on Industry Applications, Vol. 37, No. 6, pp. 1563-1573, Nov/Dec 2001.
- Lie, S.—Di Pietro, C., “Copper Die Cast Efficiency Improvement and Economic Consideration,” IEEE Transaction on Energy Conversion,Vol. 10 No. 3, pp. 419–424, Sept. 1995.
- Cowie, J. G.—Brender, D. T.—Peters, D. T., “Die-Cast Copper Rotors for Improved Motor Performance,” IEEE Pulp and Paper Conference,pp. 42-49, 2003.
- Poloujadoff, M.—Mipo, J. C.—Nurdin, M., “Some Economical Comparisons between Aluminum and Copper Squirrel Cages,” IEEE Transactions on Energy Conservation, Vol. 10, No. 3, 415–418, Sept. 1995.
- M. Popescu, “Analysis and Modeling of Single-Phase Induction Motor with External Rotor for Domestic Applications,” Industry Applications Conference, Vol. 1, pp. 463-470, 2000.
- Mariana, R. Beloiu and M.O. Popescu, “Rotor bars diagnosis in single phase induction motors based on the vibration and current spectrumanalysis,” International Conference on Optimization of Electrical and Electronic Equipment, (OPTIM), pp. 364-370, 2010.
|