Keywords
|
Induction Motor, Condition Monitoring, Bearing Faults, Time Domain Analysis. |
INTRODUCTION
|
A very important aspect of condition monitoring of induction motor is to detect the mechanical faults. The reliability of an induction motor is of paramount importance in industrial, commercial, aerospace and military applications. Bearing play an important role in the reliability and performance of all motor systems. Due to close relationship between motor system development and bearing assembly performance, it is difficult to imagine the progress of modern rotating machinery without consideration of the wide application of bearing. In addition, most faults arising in motors are often linked to bearing faults. The result of many studies show that bearing problems account for over 40% of all machine failure. In present paper, investigations have been done by using time domain analysis techniques for detection of bearing faults. As bearing faults are critical to the functioning of any electromechanical system, they form the main topic of discussion in this paper. In some applications such as aircrafts, the reliability of bearing may be critical in safeguarding human lives. For this reason, the detection of bearing faults has been an important research area. |
LITERATURE REVIEW
|
A large survey on faults in induction motor is carried out by Electric Power Research Institute (EPRI) in 1985.According to this survey found that bearing (41%), stator (37%), rotor (10%) and other (12%) faults occurred in the induction motor. Time domain refers to a display or an analysis of the vibration data as a function of time. The analysis can be done by visually looking at portions of the time domain waveform or by examining some statistical parameters related to time domain analysis. In the1980’s, Mathew and Alfredson presented a review of vibration monitoring techniques in the time and frequency domains for rolling element bearings. Analysing the vibration signals directly in the time domain is one of the simplest and Non-intrusive detection techniques.Tandon and Nakra (1993) reported visual inspection of the time history of the vibration signals, time wave form indices, probability density function, and probability density moments that are easily analyzed using the time domain analysis. Various time domain statistical parameters have been used as trend parameters to detect the presence of incipient bearing damage. The most commonly used ones are peak, RMS, crest factor and kurtosis. Dyer and Stewart (1978) first proposed the use of kurtosis for bearing fault detection. These values for a damaged bearing tend to be greater than the values for a normal bearing. |
BEARING FAULT TYPES
|
The bearing consists of mainly of the outer race and inner race way, the balls and cage which assures equidistance between the balls. The different faults that may occur in bearing can be classified according to the affected element: |
Outer raceway defect |
Inner raceway defect |
Ball defect |
Figure 1 shows internal structure of the ball bearing. It consist of rolling element (i.e. ball) fitted into a two races i.e. inner race & outer race in which one race is stationary and the other is attached to the rotating assembly. |
In the figure 2, it shows the inner race bearing fault. For the experiment purpose Motor bearings were seeded with faults using electro-discharge machining (EDM) or drilling a hole in its inner race. |
In the figure 2, it shows the inner race bearing fault. Both the inner raceway fault and outer raceway fault are occurred due to the wear and tear of the bearing. |
The faults occurs in the bearing is generally due to the excessive load, rise of temperature inside the bearing, use of bad lubricant and so on. For condition monitoring we can use the following signal analysing tools: |
ÃÂ¯ÃÆÃË Time Domain Analysis |
ÃÂ¯ÃÆÃË Frequency Domain Analysis |
ÃÂ¯ÃÆÃË Time-Frequency AnalysisEXPERIMENTAL SETUP |
EXPERIMENTAL SETUP
|
As shown in Figure 4 above, the test stand consists of a 2 HP motor (left), a torque transducer/encoder (center), a dynamometer (right), and control electronics (not shown). Vibration data was collected using accelerometers, which were attached to the housing with magnetic bases. Vibration signals were collected using a 16 channel DAT recorder, and were post processed in a Matlab environment. All data files are in Matlab (*.mat) format. Digital data was collected at 12,000 samples per second, and data was also collected at 48,000 samples per second for drive end bearing faults. Speed and horsepower data were collected using the torque transducer/encoder and were recorded by hand. In that we have use the Drive end bearing ball fault data for various diameters. |
DEFINATIONS
|
In Time domain analysis following factors are consider: |
A) RMS (Root Mean Square) Value: The value of an AC voltage is continually changing from zero up to the positive peak, through zero to the negative peak and back to zero again.The RMS (Root Mean Square) Value of the vibration acceleration can be used for primary Health investigation of the machine. The RMS of a variant X is the square root of the mean squared value of x. RMS level increases with increase in fault severity level. |
RMS=SQRT 1/ N Σ (Xi-μ) ^2 |
Where |
N is number of samples. |
Xi is the amplitude of individual sample. |
μ is the mean value of samples |
B) Peak Level: The Peak Level of the discrete time signal is: |
PEAK LEVEL = MAXIMUM (Xi) |
Peak level is indicative of occurrences of impacts. For low-level fault, peak level is good indicator. |
C) Crest Factor: The crest factor, is the ratio of peak value to the RMS value, yields a measure of spikiness of a signal. Crest factor of radial vibration signal is often used to indicate the rolling bearing faults. Crest factor for healthy bearing is more as compared to that of damaged bearing, in many cases. |
CREST FACTOR = PEAK VALUE / RMS VALUE |
The crest factor is initially increases with fault level but it decreases with the increase in fault severity after a particular level. |
D) Skewness: Skewness is a measure of symmetry, or more precisely, the lack of symmetry about its mean. A distribution, or data set, is symmetric if it looks the same to the left and right of the center point of Gaussian distribution. Negative values of Skewness indicate the data that are skewed left and positive values for right skewness. The skewness is found as the consistent parameter with respect to fault severity. |
SKEWNESS = [1/ N Σ (Xi-μ) ^3] / σ ^3 |
where σ is the standard deviation of the time record. |
E) Kurtosis: It is a measure of whether the data are peaked or flat relative to a normal distribution. A uniform distribution would be the extreme case. High kurtosis indicates a "peaked" distribution and low kurtosis indicates a "flat" distribution near the mean value. |
KURTOSIS = [1/ N Σ (Xi-μ) ^4] / σ ^4 |
The kurtosis value increases significantly up to low level ball defect however it decreases back to value corresponding to healthy case. |
OBSERVATIONS
|
In Figure 5, its show the time Vs acceleration graph of healthy bearing with no load condition by using accelerometer sensor data. |
In Figure 6, its show the time Vs acceleration graph of rolling element (i.e. ball) fault in the bearing. The ball is defect with 0.007 inches in diameter |
In Figure 7, its show the time Vs acceleration graph of ball fault in the bearing. The ball is defect with 0.014 inches in diameter. |
In Figure 8, its show the time Vs acceleration graph of ball fault in the bearing. The ball is defect with 0.021 inches in diameter. |
In Figure 9, its show the time Vs acceleration graph of ball fault in the bearing. The ball is defect with 0.028 inches in diameter. |
In Figure 10, its show the time Vs acceleration graph of inner race fault with diameter 0.007 inches in the bearing. |
In Figure 11, its show the time Vs acceleration graph of outer race fault with diameter 0.007 inches in the bearing. |
RESULTS
|
Table 1 shown the data which is extracted from the time domain signal of the bearing. This data is very useful at the time of deep study of bearing faults. As the faults occurred time domain parameter value is changes from normal condition to faulty condition. |
Figure 5 to figure 11 shown the time domain signal which are extracted from the bearing. Here we can easily see that the variation in spectrum from normal condition to different fault condition and through this analysis we can easily say that the bearing is faulty or not. |
CONCLUSION
|
This experiment conclude that through the condition monitoring of the motor bearing we can easily avoid the critical emergency shutdown as well as reduce the maintenance cost of the motor other faults. Here we also see that through the time domain analysis, we can easily distinguish the signals from normal to faulty condition. |
ACKNOWLEDGMENT
|
I express my sincere thanks to my mentor, Mrs. Meera A. Khandekar for her expert guidance, encouragement and motivation during the development of this work, without which this work would not have developed to its present form. We are thankful to Dr. S. L. Patil for his support and help. We are also thankful to bearing fault data centre website for providing access to ball bearing test data. Last but not the least; I am grateful for the endurance from my family and friends who silently supported me. |
Tables at a glance
|
 |
Table 1 |
|
|
Figures at a glance
|
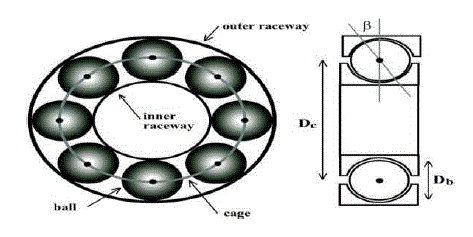 |
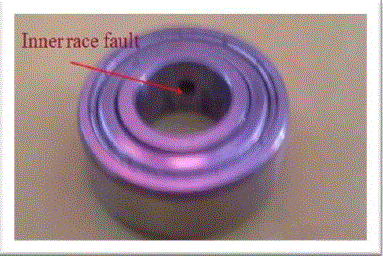 |
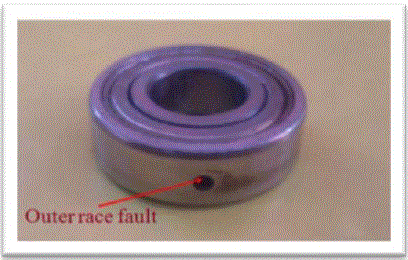 |
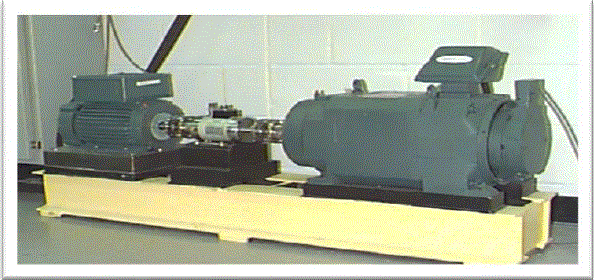 |
Figure 1 |
Figure 2 |
Figure 3 |
Figure 4 |
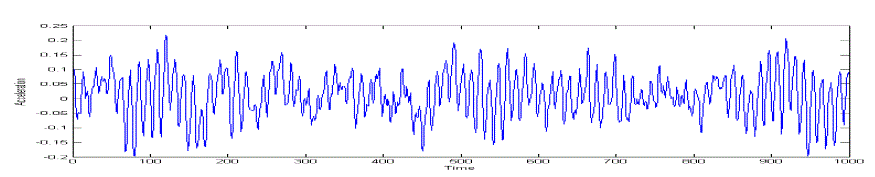 |
 |
 |
 |
Figure 5 |
Figure 6 |
Figure 7 |
Figure 8 |
 |
 |
 |
Figure 9 |
Figure 10 |
Figure 11 |
|
|
References
|
- P. F. Allbrecht, J. C. Appiarius, and R. M. McCoy, et al, “Assessment of the reliability of motors in utility applications – updated,” IEEE Transactions on Energy Conversion, Vol. 1, No. 1, pp. 39-46, 1986.
- Eschmann P, Hasbargen L, Weigand K, “Ball and roller bearings: Their theory, design, and application” (London: K G Heyden), 1958.
- Riddle J, “Ball bearing maintenance”, Norman, OK: University of Oklohama Press, 1955.
- http://csegroups.case.edu/bearingdatacenter/pages/download-data-file
- Tandon N and Choudhury A, “A review of vibration and acoustic measurement methods for the detection of defects in rolling element bearings”, Tribology International, Vol32 (8): pp 469-480. 1999.
- Williams T, et al,” Rolling element bearing diagnostics in run-to-failure lifetime testing”, Mechanical Systems and Signal Processing,Vol 15(5): pp 979-993.2001.
- Martin,H.R:Honarvar,F.,”Application of Statistical Moments to Bearing Failure Detection”,AppliedAcoustics,Vol. 44, 67-77,1995.
|