Keywords
|
Diode rectifiers, Average current mode control, interleaved boost converter, PFC, PI controller, THD. |
INTRODUCTION
|
The extensive use of dc power supplies inside most of electrical and electronic appliances lead to an increasing demand of DC power. So for obtaining this DC power, an interface must be provided between the AC power line and the load requiring DC voltage. |
Generally this conversion from AC to DC is done by single phase diode rectifiers. These classical converters rectify the input ac line voltage to obtain DC output voltage, but this DC voltage oscillates between zero to peak. To reduce this ripple from DC voltage a filter capacitor is used, and that is where the problem of power factor and THD arises. The capacitor maintains the DC voltage at a constant value but it draws non sinusoidal current from the supply. The capacitor draws current from the supply only at the line voltage peaks. So the input current becomes pulsating which results in poor power factor and high THD. So the power factor correction techniques are gaining attention. There are two types of power factor correction techniques, passive power factor correction and active power factor correction. Better power factor cannot be obtained by passive power factor correction techniques, and the output voltage also cannot be controlled. As a result active power factor correction technique is used for satisfactory result. In active power factor correction most popular is boost converter for its continuous input current. The boost converter is widely used as active power factor corrector [1] because it draws continuous input current from the supply. This input current can be controlled to follow a sinusoidal reference using current mode control techniques. There are different current mode control techniques [2], but best result can be obtained from average current mode control technique [3] due to its various advantages. In this paper, power factor correction and THD minimization is done by two phase interleaved boost converter [4] whose input current is controlled by average current mode control technique. In this interleaved boost converter there are two boost converters operating in 180Ãâ¹ÃÅ¡ out of phase . So the ripple present in the current of boost converter gets almost eliminated and that is the main advantage of the interleaved boost converter. Here for average current mode control, PI controllers are used. The simulation of interleaved boost converter with PI controller is shown here to show that interleaved boost converter with PI controller provides good input current with high power factor and low THD. All the simulation is done by MATLAB-Simulink. |
NECESSITY OF POWER FACTOR IMPROVEMENT
|
Power factor is a figure of merit that measures how effectively power is transmitted between a source and load network. It always has a value between zero and one. The unity power factor condition occurs when the voltage and current waveforms have the same shape, and are in phase. Power factor is defined as the cosine of the angle between voltage and current in an ac circuit. If the circuit is inductive, the current lags behind the voltage and power factor is referred to as lagging. However, in a capacitive circuit, current leads the voltage and the power factor is said to be leading. Power factor can also be defined as the ratio of active power to the apparent power .The active power is the power which is actually dissipated in the circuit resistance. The reactive power is developed in the inductive reactance of the circuit. Power factor = (Active power)/ (Apparent power) A load with a low power factor draws more current than a load with a high power factor for the same amount of useful power transferred. The higher currents increase the energy lost. So power factor improvement is required |
POWER FACTOR CORRECTION (PFC) TECHNIQUES
|
Power factor correction is a technique by which the degraded power factor of a power system can be improved by use of external equipments. Power factor correction can be classified into two types: passive power factor correction and Active power factor correction In Passive PFC, only passive elements are used with the diode bridge rectifier, to make the line current sinusoidal. By using passive PFC, power factor cannot be increased to a desired value. With increase in the voltage, the PFC components increase in size. In passive power factor correction, the power factor can never be corrected to 1 and the output voltage cannot be controlled as well. In active PFC there is control over the amount of power drawn by a load and power factor is close to unity. Commonly in any active PFC the input current of the load is controlled in order to make the current waveform follow the main voltage waveform closely (i.e. a sine wave). A combination of the reactive elements and some active switches are used to increase the effectiveness of the line current shaping and to obtain controllable output voltage. |
PFC BY AVERAGE CURRENT CONTROLLED BOOST CONVERTER
|
There are different current mode control techniques to manipulate continuous input current obtained from the boost converter, however among them average current mode control provides the best result. In average current mode control the switching frequency is constant and it allows a good input current waveform. Fig.1 PFC by average current controlled boost converter Here for average current mode control voltage control loop and current control loop are used. Input current iL is compared with the reference current iref. The current reference iref is obtained by scaling down the line voltage by a resistive divider with scaling factor K and multiplying it with the actuating signal obtained at the output of, voltage PI controller. This actuating signal is obtained by comparing the output voltage with reference voltage and passing the voltage error verror through the voltage PI controller. The comparison of il and iref gives the ierror which has been amplified by another PI controller, and compared with the saw tooth wave, and provides the PWM drive signal for the switch S.The PI controllers consist of a proportional gain that produces an output proportional to the input error and an integration to make the steady state error zero.When the inductor current iL rises, the error current ierror decreases. On the contrary, ierror increases. When output voltage Vo increases, the output voltage error verror decreases, error current ierror decreases. On the contrary, ierror increases. |
PFC BY AVERAGE CURRENT CONTROLLED INTERLEAVED BOOST CONVERTER
|
Interleaving technique consists of a phase shifting of the control signals of cells in parallel operating at the same switching frequency. The main advantages are the current distribution and ripple reduction. The current in the switches are just a fraction of the input current. So interleaved boost converters can reduce input current ripple and the Switching losses. The block diagram of the proposed system is represented in fig.2. |
Here for the power factor correction, a two phase interleaved boost converter is used. The continuous current drawn by the interleaved boost converter, is controlled using average current made control and for this purpose PI controllers are used. The average current mode control uses voltage control loop and current control loops. For ripple reduction the two phases of interleaved boost converter operate in 180Ãâ¹ÃÅ¡ out of phase. To obtain phase shift of 180Ãâ¹ÃÅ¡ the output of the two current PI controllers are compared with two saw tooth waves that are 180Ãâ¹ÃÅ¡ out of phase. In this way the PWM signals for the switches S1 and S2 are generated. |
RESULT AND DISCUSSION
|
At first simulation of single phase diode rectifier is performed. The MATLAB-Simulink model of single phase diode rectifier with filter capacitor is shown in fig.3 |
From Fig.4 we can see that the input current is discontinuous and pulsating. As a result the power factor is poor |
The active power and reactive power are respectively obtained P=1200W and Q=-680VAR So the power factor is 0.87 The THD of the input current is represented in Fig 6 |
From Fig 6;we can say that THD is as high as 100.41%. To improve the power factor and minimize the THD boost converter is used.The MATLAB-Simulink model using boost converter is shown in Fig.7. |
In this simulation output power is considered to be 800 watt. And the output voltage is 400V. So the resistance is taken as 200 ohm. At the output voltage one PI controller is used to maintain the voltage to its reference. The output voltage waveform is first shown in fig 8 to see whether the voltage follows the reference or not |
As we can see from Fig.9 input ac current is almost sinusoidal as the input ac voltage but there is fair amount of ripple is present in the input current. |
From the above figure we can say that |
Active power=915W |
Reactive power=- 63var |
So the power factor is 0.9976 |
THD of input current is shown in the Fig 10 |
It can be still improved by the use of interleaved boost converter and the ripple of input current can be minimized The MATLAB Simulink model of interleaved boost PFC converter average current mode control by PI controller is shown in Fig.12 |
From Fig.14 we can see that the output current is constant and pulsating. The input current is the summation of two inductor currents. As the inductor current ripples are phase shifted by 180Ãâ¹ÃÅ¡they cancel each other out. So the input current ripples are minimized. |
Active power is 950W Reactive power is -40 VAR |
So the power factor is 0.999 which is almost unity. Now the THD obtained of the input ac current is shown in Fig.16 |
The THD of input current is 10.92% |
So we can say that interleaved boost converter provides better power factor and THD |
The comparison of input power factor for different circuit topologies is shown in following table. |
CONCLUSION
|
Energy conversion is the main issue of the power electronics and widely applied in today’s world. Also we cannot compromise with the power factor and THD. In this paper power factor correction and THD minimization by interleaved boost converter in continuous conduction mode, with average current mode control using PI controller, has been theoretically analyzed and simulated in MATLAB- Simulink. From the simulation result it can be concluded that using interleaved boost converter power factor has been improved a lot and THD has been minimized significantly. For further improvement fuzzy logic controller or neural network can be used in the place of PI controller. |
Tables at a glance
|
 |
Table 1 |
|
|
Figures at a glance
|
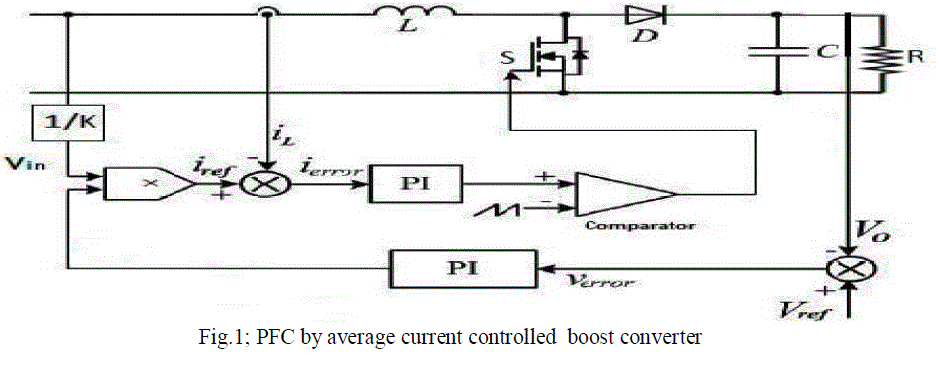 |
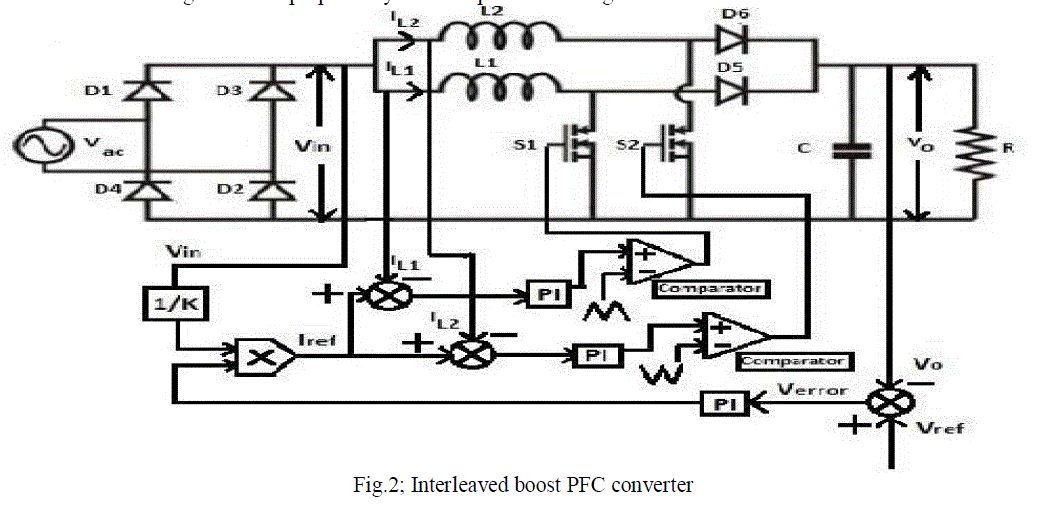 |
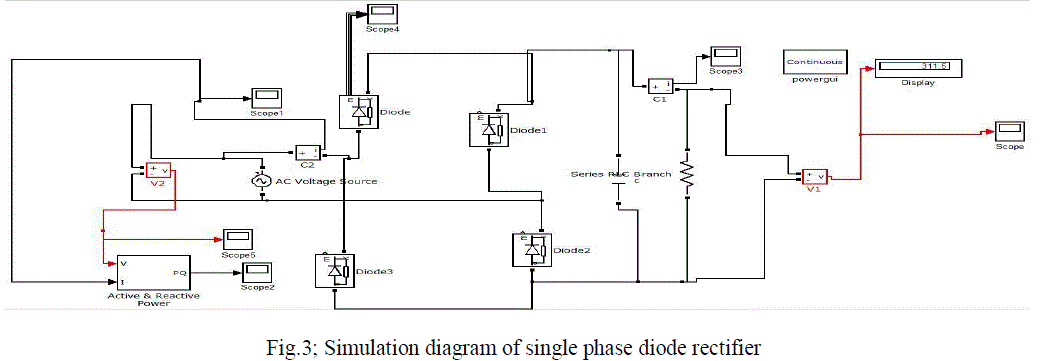 |
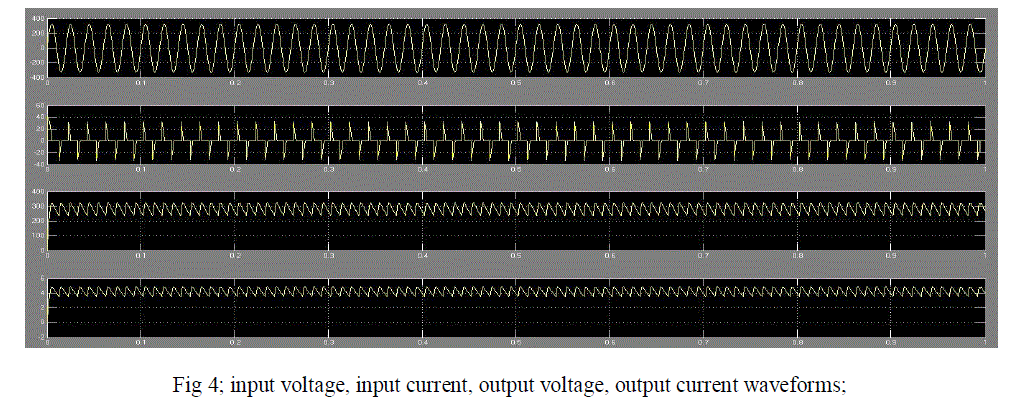 |
Figure 1 |
Figure 2 |
Figure 3 |
Figure 4 |
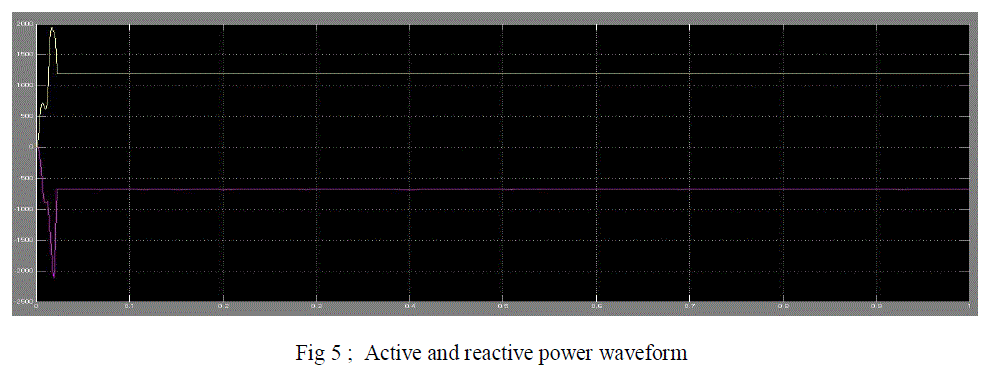 |
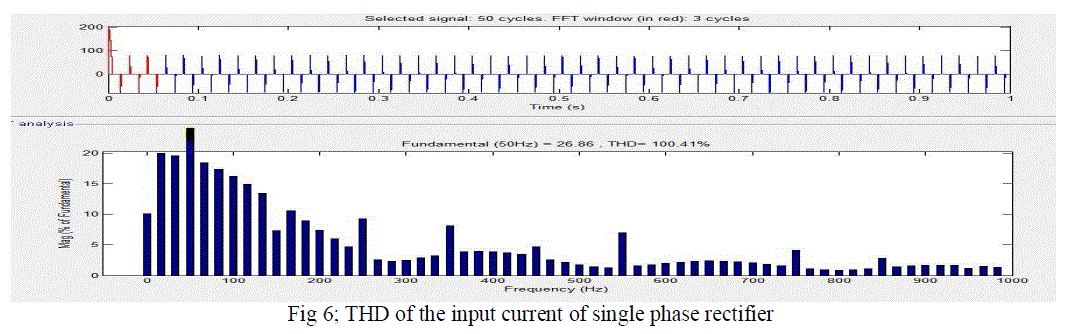 |
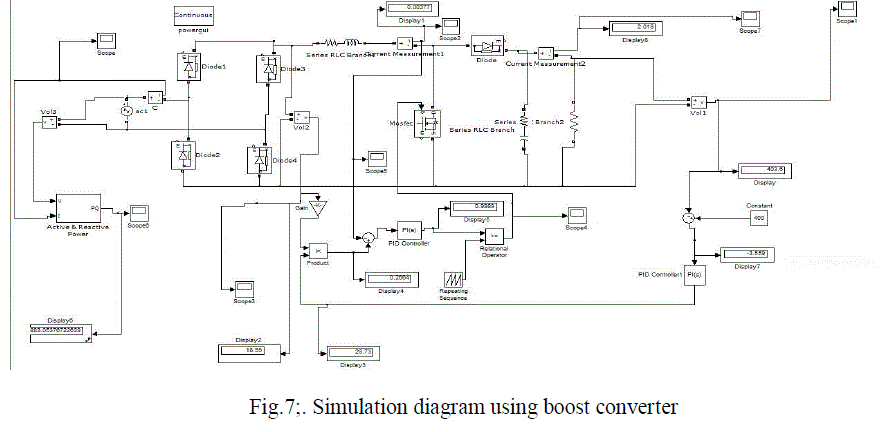 |
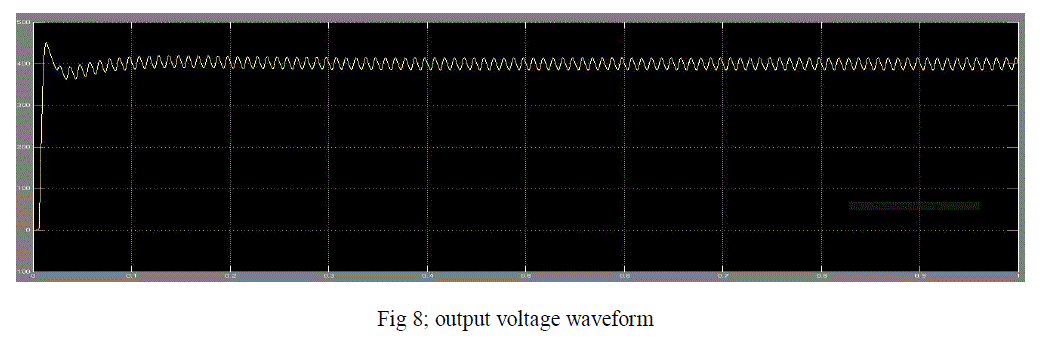 |
Figure 5 |
Figure 6 |
Figure 7 |
Figure 8 |
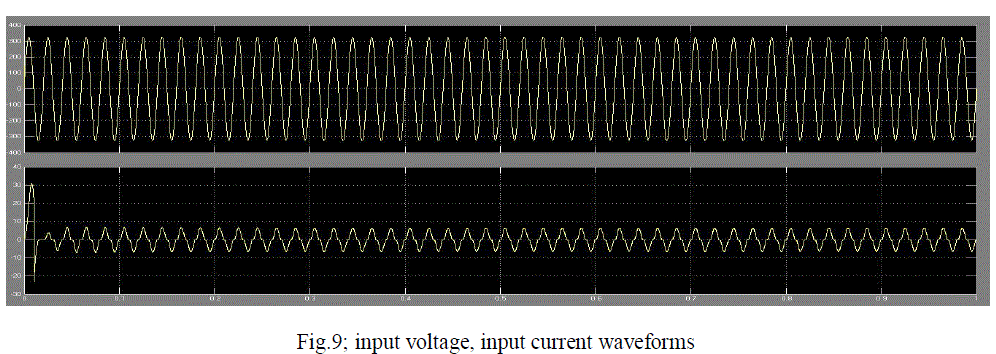 |
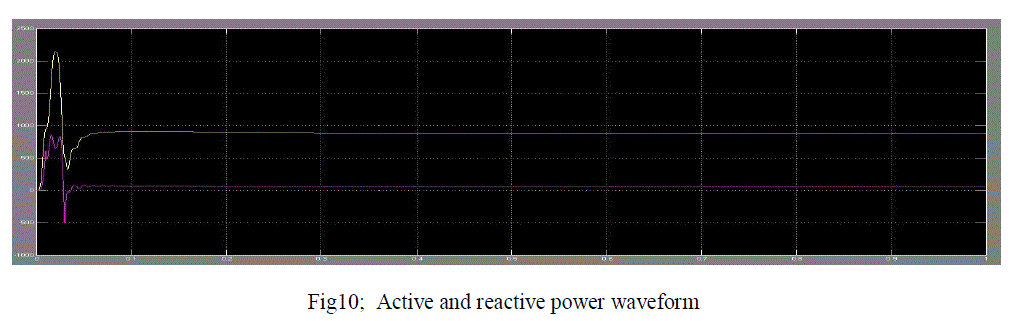 |
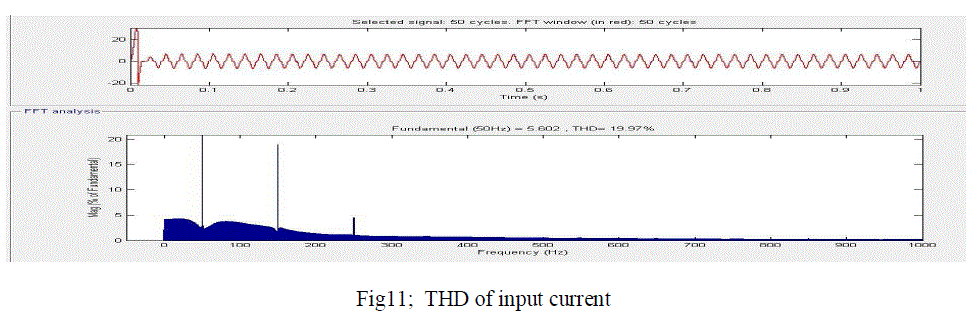 |
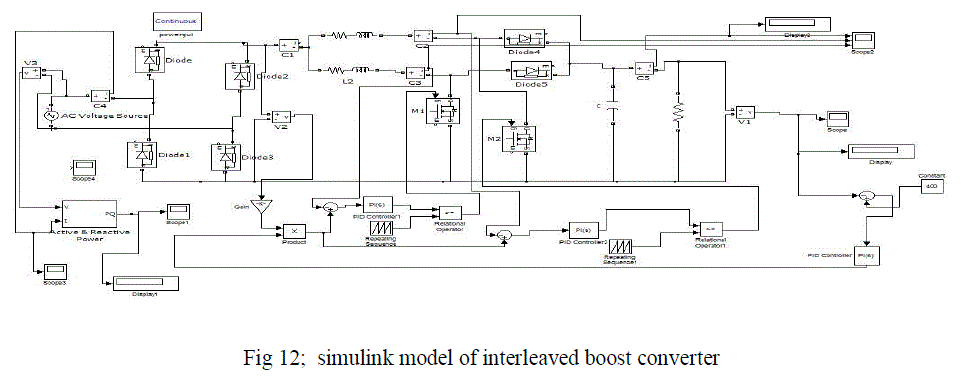 |
Figure 9 |
Figure 10 |
Figure 11 |
Figure 12 |
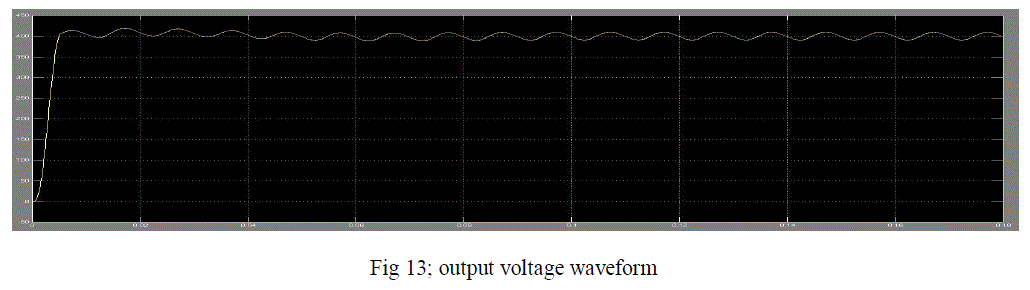 |
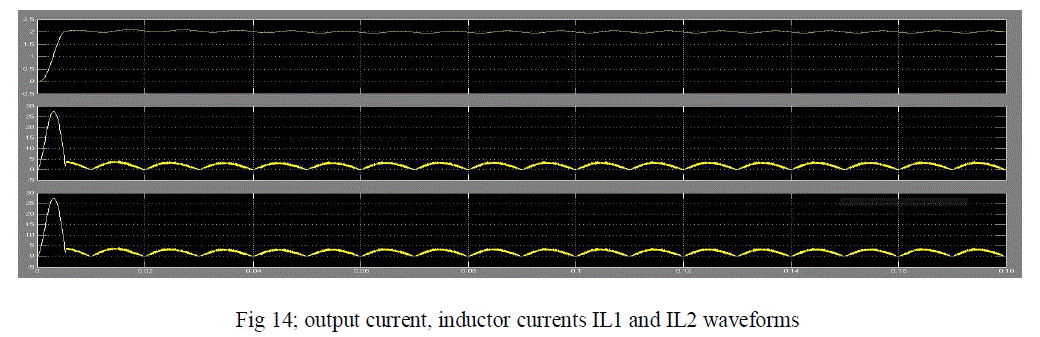 |
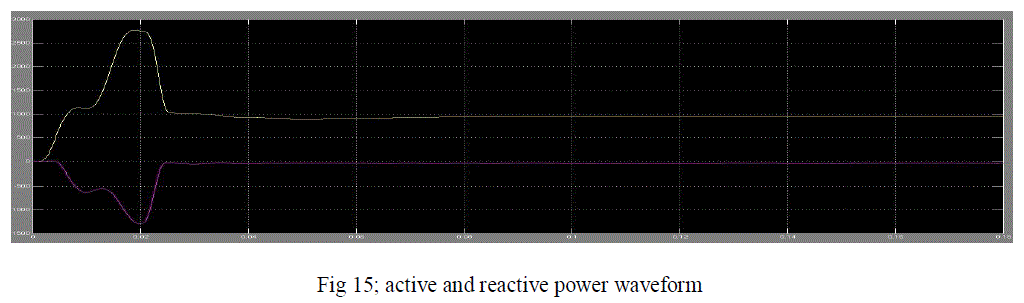 |
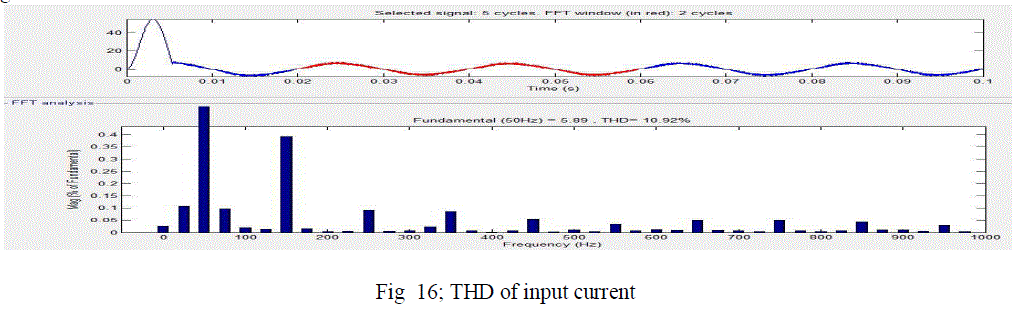 |
Figure 13 |
Figure 14 |
Figure 15 |
Figure 16 |
|
|
References
|
- Muhammad H. Rashid, Power Electronics Handbook (Academic Press, 2001).
- Brad Bryant, Member, IEEE, and Marian K.Kazimierczuk, Fellow, IEEE, Modeling the Closed-Current Loop of PWM Boost DC–DC Converters Operating in CCM with Peak Current-Mode Control, IEEE Transactions on circuit and systems—I: regular papers, vol. 52, no. 11, November 2005.
- Wa Ma, Mingyu Wang, Shuxi Liu, Shan Li, and Peng Yu, Stabilizing the Average- Current-Mode-Controlled Boost PFC Converter via Washout- Filter-Aided Method IEEE Transactions on Circuits and Systems- II, Express Briefs, vol. 58, no. 9, September 2011.
- Laszlo Huber, Member, IEEE, Brian T. Irving, and Milan M. Jovanovic´, Fellow, IEEE, Open-Loop Control Methods for Interleaved DCM/CCM Boundary Boost PFC Converters, IEEE Transactions on Power Electronics, vol. 23, no. 4, July 2008.
- Po-Wa Lee, Yim-Shu Lee, David K. W. Cheng, and Xiu-Cheng Liu, Steady-State Analysis of an Interleaved Boost Converter with Coupled Inductors, IEEE Transactions on Industrial Electronics, vol. 47, no. 4,August 2000.
- P. Vijaya Prasuna, J. V. G. Rama Rao, Ch. M. Lakshmi, Improvement in Power Factor & THD Using Dual Boost Converter, International Journal of Engineering Research and Applications, vol. 2, Issue4, July-August 2012, pp.2368 -2376
|