Keywords
|
Kurtosis, DWT, Bearing Fault |
INTRODUCTION
|
Defect or fault in rotating machine leads to serious consequence in terms of downtime and failure. Faults are broadly classified as electrical fault and mechanical fault, in which rotor fault, shorted turn fault are electrical in nature and misalignment, unbalance, gear fault, bearing fault are mechanical type of fault. More than fifty percent machine failures are mechanical in nature, in which most of them are related to the bearing fault in which ninety percent of them are inner race and outer race type[1][8]. Vibration signal can be very importantly used in fault diagnosis Some of recent work in the field of fault diagnosis, by the several researchers are reported, in which McInery,S.A. et al.(2003) proposed a fault diagnosis technique of rolling element bearing with the help of industrial module by envelope analysis and kurtosis feature [1].Bhende A.R. et.al (2011) feature like kurtosis, crest factor, shape factor and impulse factor are used to compare the signal using time and frequency domain analysis techniques[2].Devaney M. J. et.al (2004) proposed a technique using root mean square (RMS) as fault feature along with wavelet packet decomposition of raw vibration signal, also suggested a radial basis function neural network model for fault diagnosis [3]. Bechhoefer E & Michel kingley (2009) presented the performance evaluation method of the time synchronous averaging when no tachometer signal is available. They also proposed the background and properties of the TSA [4].A RMS feature extraction related to the bearing damage using wavelet transform for the different aging cycle of the machine is proposed by Seker S. et,al (2003) [5].Wang H. et al (2009) developed a method based on the kurtosis wave and information divergence for rolling element bearing fault diagnosis, also compare the proposed method with the traditional envelop spectra [6]. |
Various signal processing techniques are used in machine fault such as Fourier transform (FFT), Hilbert Huang transform (HHT) Gabor transform (GT) Short Time Fourier Transform (STFT). FFT method is easy to implement, normally used for stationary signal but couldn’t set remarkable outcomes for the non-stationary signal like vibration [9] STFT is used to analyse transient signal in time frequency domain with fix window size, leads to poor frequency resolution, above problem is overcome by wavelet transform Multi resolution analysis. DWT provide high time resolution for high frequency and high frequency resolution for low frequency. |
A Discrete Wavelet transform, Wavelet packet transform, Empirical mode decomposition, Wigner-Ville distribution are some signal processing techniques used in fault diagnosis in time-frequency domain. Main objective of the proposed work is to verify the effectiveness and robustness of the different signal processing techniques in terms of the computation effort and time for analysis of the bearing related fault. |
DISCRETE WAVELET TRANSFORMS
|
Wavelet transform is process of correlation shifting and scaling of the signal with the small duration wavelet. DWT is discrete in terms of sampling scaling and shifting parameters not in terms of signal. A DWT permit systematic decomposition of signal into its frequency sub-band with minimum distortion of signal, this process is achieved by using two channel sub band coder proposed by Mallat.1989, in which low frequency and is referred as approximate and high frequency band is referred as detail [1][10][11][12][17]. wavelet analysis splits-up the signal into shifted and scaled version of function called mother wavelet, DWT uses filter bank of low pass and high pass filter which is followed by down sampling to compute approximate and detail coefficient where approximate is low pass filtered and detail is high pass filter which is derived from mother wavelet, the process is continue with the approximate( low frequency) coefficient to increase the level of decomposition by further breaking it up in approximate and detail part as shown in the Figure 1 . The shape and the frequency response of these filter depends on the type and order of mother wavelet used in analysis. |
EXPERIMENTAL SETUP AND DATA USED
|
The standard set of data is collected from the test setup prepared by vibration data centre “case western reserve university” [7] the experimental setup prepared by the university consists of a 2 hp motor running at the speed of 1730 rpm, transducer/encoder, dynamometer, and control electronics. The test bearings support the motor shaft. Vibration signal was collected with accelerometers, attached to the housing with magnetic bases. During some experiments, an accelerometer was attached to the motor supporting base plate as well. 16 channel DAC recorder and Matlab environment was used to collect and process the data at 12,000 samples per second. Four set of data were obtained from the experimental set up one in normal condition, inner race condition, and outer race condition rolling element defects of 0.7”, 0.14” and 0.21” severity of the damage, respectively. |
The most common faults in rolling element bearing are outer race defect, inner race defects and bearing defect. Bearing fault frequencies are depends on the bearing geometry shape and shaft running frequency Figure 1 showing the defective bearing of respective fault type.. |
Detail specification of the bearing is listed in table 1. The characteristic fault frequency depends upon the bearing geometry and size. A mathematical expression mentioned in the Tommy S. Chow et al. 2004[18]. Correlate the different bearing fault type with rotating frequency of the machine and the bearing geometry. |
The characteristic fault frequency is listed in the Table 2, illustrate characteristics frequency of the bearing fault under Inner Race, Outer Race and Bearing element defect |
FAULT DETECTION AND PARAMETER EXTRACTION
|
Five different group of pre-processing techniques and thirteen different traditional features like rms, kurtosis, crest factor, FM0, NA4 etc are used in vibration signal analysis and fault detection, these signal processing are; 1)raw signal analysis, 2)Time synchronous averaging (TSA), 3)residual (RES) signal analysis 4) Differential (DIF) signal analysis 5) band-pass mesh signal (BPM) analysis [3]. A lot of analysis techniques and method has been reported in the field of condition monitoring and fault diagnosis in which the raw vibration signal collected from the motor after conditioning and DC component removal is used in fault detection[5][13]. The time synchronous averaging (TSA) is a preprocessing technique in which vibration signal coming out of sensor, is segmented based on the synchronous (Trigger) signal. It is used to extract repetitive signals from additive noise. In TSA approach a raw data is divided up into segments of equal length chunks related to the synchronous signal and averaged together [14]. An accurate knowledge of the repetitive frequency of the desired signal or a signal that is synchronous with the desired signal (such as shaft running frequency) is the basic need of the process. A Time synchronous averaging of the vibration data is obtained with respect to the shaft running frequency , a shaft rotating frequency is 29.95Hz or 1797 RPM. A mother wavelet ‘Sym 8’ is used in the DWT. Eight level of signal decomposition are used in DWT, which splits the signal in eight details and one final approximation coefficient. This component covers the entire frequency spectrum in different band width. Detail at the eighth level contains the shaft running frequency in it as show in the table 3. Three different fault type of rolling element bearing, Inner race, Outer race and ball bearing defect are detected in the proposed work using the DWT of the TSA of the vibration data. It gives a simplified procedure for fault diagnosis using kurtosis as statistical parameter based on DWT. Kurtosis trained of detail ‘D6’ corresponds to the characteristics fault frequency as tabulated in the table 2 are compared with the other statistical parameter such as the RMS Crest factor. The variation in the kurtosis value respect to the fault severity are tabulated and demonstrated in the Figure 3. A signal acquired from the accelerometer can be is used after TSA based pre-processing in frequency domain or time-frequency domain analysis techniques as reported in [5][13][14]. A FFT method provides the frequency domain analysis, DWT, HHT [15] Empirical Mode Decomposition (EMD) [12] Wigner’s Ville Distribution (WVD), wavelet packet analysis (WPT) provides the Time frequency domain analysis. Each technique has its own advantages and limitation in which the computation time plays important role in the real time diagnosis of the fault. A comparison of the all the signal processing technique based on their computations time required for analysis of the signal is demonstrated using the bar chart in the Figure 4. |
RESULT AND CONCLUSION
|
The experimental procedure discussed in the work utilizes the TSA based pre processing method and a time-frequency domain signal processing method DWT to detect various bearing fault. The experimental data show that the kurtosis value remain typically at 2 in undamaged condition as soon as the fault developed, initially it overshoot in different range of amplitude with respect to the different fault type as described in [13]. When fault severity increases from the 0.7” to 0.14” and 0.21” in size, the kurtosis value initially overshoots and thereafter starts decreasing and comedown, as show in the Figure 3. The variation in the amplitude of the kurtosis remains in the different range for the different fault type but no such classified variation occurs in the RMS value and Crest factor as tabulated in the table 4, table 5 and Table 6. |
The fault diagnosis based on the TSA method is effectively used in this experimental procedure to diagnose bearing faults such as the Inner race, outer race and bearing fault Bearing fault such as IRF BRF ORF are successfully and more efficiently detected using Kurtosis as statistical parameter instead of the RMS and crest factor. |
A suitability of the various signal processing techniques are verified in terms of their computation effort Figure. 4 illustrate and compare the computational effort of different signal processing in which the highest computational effort is observed in the HHT where as the lowest is in the DWT, by this DWT can be selected as the most suitable signal processing with lowest computation effort. |
Tables at a glance
|
 |
 |
 |
Table 1 |
Table 2 |
Table 3 |
 |
 |
 |
Table 4 |
Table 5 |
Table 6 |
|
|
Figures at a glance
|
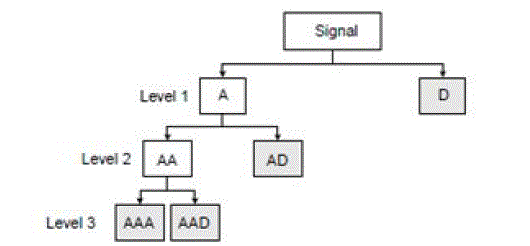 |
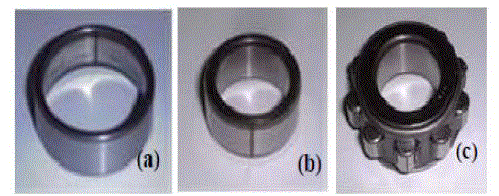 |
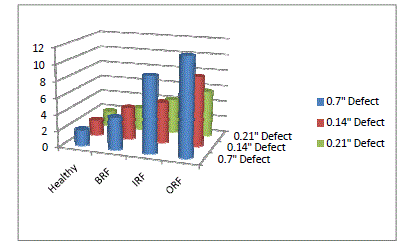 |
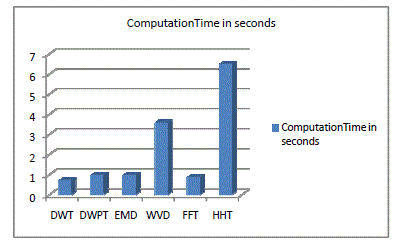 |
Figure 1 |
Figure 2 |
Figure 3 |
Figure 4 |
|
|
References
|
- Mcinerny S.A. and Y Dai “Basic vibration Signal Processing for Bearing Fault Detection, IEEE Transaction & Education) Vol.46, No.1,pp 149-156. 2003
- Bhende A. And G.K. Awari, SP Untawale “Assessment of Bearing Fault Detection Using Vibration Signal Analysis” VSRD-TNTJ, Vol.4, No.5.pp 249-261, 2011
- Devaney M.J. and Levent Eren “Monitoring an induction motors current and detecting bearing failure IEEE instrumentation and measurement magazine” ISN. 1094-6969/4, pp 30-50, 2004
- Bechhoefer E. & Michael Kingsley “A Review of Time Synchronous Average Algorithms” Proceeding of In proceeding of Annual Conference of the Prognostics and Health Management Society, 2009
- Seker S and Emine ayaz “Feature Extraction Related To Bearing Damage In Electric Motor By Wavelet Analysis” Journal of the frankline institute Vol. 340, pp 125-134, 2003
- Wang H. and Peng cheng “Fault Analysis Method Based On Kurtosis Wave And Information Divergence For Rolling Element Bearings” WSES Transaction on systems Vol.8, No.10,pp 1155-1165,2009
- Bearing data centre,www.csegroups.case.edu/bearingdatacenter/pages/12k-drive-end-bearing-fault-data. (Case Western University).
- Santhana A. R & N. Murali “Morlet Wavelet UDWT Denoising And EMD Based Bearing Fault Diagnosis” Electronics, Vol. 17, No. 10 pp.01- 07,2013
- Jayaswal P, A.K.Wadhwani, K.B.Mulchandani “Review Article; Machine Fault Signature analysis, International journal of Rotating Machine, vol.2008, Hindawi Publication corporatoion” IJRM,Vol. 2008. AID 583982 pp 1-10, 2008
- Kumar A & Sarita Chokhandre, Dr. Anup Mishra “Discrete wavelet transform based signal stegnography & encryption” Vol. 4 No.05 May 2012
- Bendjama H et al.” Application of wavelet transform for Fault Diagnosis in Rotating Machinery” Vol. 2 No.1 pp 82-86
- Mallat S. G. “A Wavelet tour of signal Processing” Academic Press, Second Edition Tommy S. Chow et al. “inducation machine fault diagnosis Analysis with wavelet” IEEE Transactions ,Vol. 51 No.03.1998
- Lebold M, Mcclintic. k, Campbell. R “Review of Vibration analysis Method for Gearbox diagnostics & prognostics” Proceeding of 54th meeting of society of machine failure prevention Technology, (54) pp 623-634,2004
- Bechhoefer E. & Michael Kingsley “A Review of Time Synchronous Average Algorithms” Prod. In proceeding of Annual Conference of the Prognostics and Health Management Society, 2009
- Peng Z.K and F.L. Chu “Application of the wavelet transform in machine condition monitoring and fault diagnostics: a review with bibliography, Science Direct, Mechanical Systems and Signal Processing Vol.18 , pp 199–221,2004
- Eftekharnejad B. and M.R. Carrasco B Charney, D M. “The Application of Spectral Kurtosis on Accostic emission and Vibration from a defective bearing” Elsevier Mechanical System and Signal Processing Vol. 25, pp 266-284 ,2011
- Mallat S. G. “A Theory for multiresolution Signal Decomposition: The Wavelet Representation” IEEE Transactions on Pattern Analysis and Machine intelligence Vol II No 7. 1989
- Tommy S. Chow et al. “inducation machine fault diagnosis Analysis with wavelet” IEEE Transactions , Vol. 51 No.03 June 2004.
|