Brushless DC Motors, by their high efficiency, high torque and low volume are increasingly used in many industrial applications. By taking it into consideration, a complete model of four quadrant control of BLDC Motor operation in association with GA optimized PID controller for its position control to obtain maximum speed operation is presented in this paper. The power supply to feed the windings of the motor is given by an inverter circuit. The gate drives to the switches of inverter is fed by space vector PWM technique in this paper for reducing the total harmonic index of the proposed system than the conventional existing methods. The MatLab/ Simulink are used in this paper to establish a model of four quadrant operation of BLDC motor.
Index Terms |
Brushless DC Motor, GA optimized
PID controller, Space Vector PWM |
INTRODUCTION |
BRUSHLESS DC MOTORS are becoming more
popular in industrial applications which require high
performance as they are having comparatively high
starting torque, smaller volume and simple system
structure compared to induction motors used
commonly in industries.The motor has less inertia and
therefore it is easier to start and stop. |
BLDC motor has a permanent magnet rotor and
laminated stator poles to carry windings. Currently,
design of the BLDC Motor drive involves some
complex processes such as modelling, control scheme
selection, simulation, parameters tuning etc. To get
optimal performance expert knowledge of system is
required for tuning the controller parameters of servo
system. Recently, in the existing system different
modern control solutions included the use of PI
controllers for the optimal control design of four
quadrant operation of BLDC Motor. However, these methods are complex in nature and require excessive
computation. In addition to that, driver circuit is
required to provide gate pulses to the inverter. In the
existing systems the driver circuit to the inverter
switches was providing multiple synchronized Pulse
Width Modulation signals to the inverter providing
rectangular or trapezoidal voltage strokes supply to the
BLDC motor. |
In a BLDC motor the brushes and commutator have
been eliminated and the windings are connected to the
control electronics. The control electronics, which
includes the inverter supply and the driver circuit for
inverter switches, replaces the function of the
commutator and energizes the proper winding. So an
inverter supplies power to the stator windings of the
BLDC Motor. The switches of the inverter require gate
supply which is provided by the driver circuit. By
providing the most advanced pulse width modulation
technique of Space Vector PWM technique to the gate
driver circuits the harmonics in the inverter output is
reduced to much extend. |
Observations showed that PID controller provides a
simple and yet effective solution to many control
problems in closed loop control systems. Even though
PID controllers have a simple structure, it is a quite
challenging task to find the optimized PID gains to
provide the best possible output. Continuing
performance improvements of computational systems
are required for obtaining best performance output.
This requirement has made Genetic Algorithm (GA)
the most appropriate technique for finding global
optimal solution for some of the control systems
operations such as the search of optimal PID controller
parameters. |
OPERATING STRATEGY OF PROPOSED
SYSTEM |
The proposed system has the speed control in
association with four quadrant operation of Brushless DC motor. For the operation of BLDC motor, it
requires a three phase AC supply to be feed with the
help of an inverter. It provides a AC supply voltage to
the windings of BLDC motor. The inverter has six
switches to convert the DC supply to three phase AC
supply. The gate drive circuit is given to supply the
gate supply to the switches of the inverter. The gate
drive circuit can control the operation of BLDC motor.
Space Vector PWM signals are provided by gate driver
circuit to the switches of inverter. The implementation
of Space Vector PWM reduces the total harmonic
distortion of the inverter operation output voltage. |
The closed loop speed control of BLDC motor is
performed with the help of PID controller. The PID
controller in association with the global optimization
technique of genetic algorithm is used in this paper.
The speed of BLDC motor is sensed and the necessary
signals are provided by hall position sensors to the PID
controller. |
The PID controller in association with Genetic
Algorithm provides the output for obtaining best
controlled speed to the gate driver circuits which works
based on Space Vector PWM. The gate driver circuit
provides the gate supply and thus a controlled output is
provided to the stator windings of BLDC motor. Thus
the speed of BLDC motor can be controlled and the
process continues until the supply voltage turns to OFF
state. |
The process is followed for the operation of the
BLDC motor in all the four quadrants. The four
quadrant operating modes are Forward Motoring,
Forward Braking, Reverse Motoring and Reverse
Braking. In regenerative mode of operation the supply
is used to charge the battery with the regenerative
power. The overall architecture of the proposed system
is shown in the fig.1. |
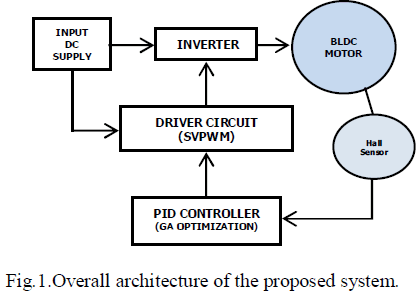 |
A. BLDC Motor |
BLDC motors are generally powered by a conventional
three-phase voltage source inverter (VSI) or current
source inverter (CSI) which is controlled using rotor
position. The rotor position can be sensed using Hall
position sensors, resolvers, or optical encoders. Due to
ease of control in BLDC motors, they are preferred for
numerous applications in low power and variable
speed drives. BLDC motor drive and it is also called a
trapezoidal brushless DC drive, or rectangular fed
drive. It is supplied by three-phase rectangular current
blocks of 120° duration, in which the ideal motional
EMF is trapezoidal, with the constant part of the
waveform timed to coincide with the intervals of
constant phase current. |
The PMBLDC motor has its losses mainly in the stator
due to its construction; hence the heat can easily be
dissipated into the atmosphere. As the back EMF is
directly proportional to the motor speed and the
developed torque is almost directly proportional to the
phase current, the torque can be maintained constant
by a stable stator current in a BLDC motor. The
average torque produced is high with fewer ripples in
BLDC motors. BLDC motor can be used in general
and low cost applications. These motors are preferred
for numerous applications, due to their features of high
efficiency, silent operation, compact in size and low
maintenance. |
The stator of a PMBLDC motor usually has three
phase concentrated windings; however, the rotor
construction varies according to desired requirements.
Two main configurations of PM rotors are surface
mounted magnet type where magnets are mounted on
the outer surface of the rotor, and the buried magnet
type where the magnets are mounted inside the
magnetic structure of the rotor. |
Another type of PMBL motor is the axial field
machine where the direction of the magnetic field is
axial instead of radial. The configurations of axial field
BLDC motors include a single stator and single rotor, a
single stators and wiched between two rotors (double
air gaps), a single rotor sandwiched between two
stators (double air gaps)and a variety of multiple
stators and rotors (multiple air gaps). |
Any of these BLDC motor rotor configurations can be
selected on the basis of application and power rating.
Various other configurations of BLDC machines
include Axial Flux Permanent Magnet (AFPM)
machines, Permanent Magnet alternators and torus
alternators with different rotor geometries like surface type, interior type, radial and axial field machines in
two, three and multiphase PMBLDC machines. |
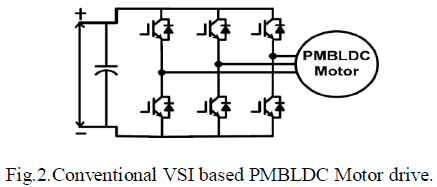 |
A BLDC motor can be divided into electrical part and
mechanical part. The electrical part contains phase
currents, phase voltages and back-EMF voltages, while
the mechanical one is described by electromagnetic
torque, load, motor inertia, angular speed and rotor
position. Equation (1) shows the relation between
electrical parameters. |
 |
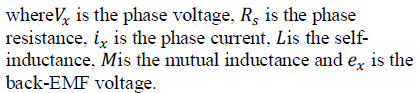 |
The relations describing the mechanical activity in the
motor are presented in equations(2)and (3). |
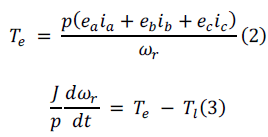 |
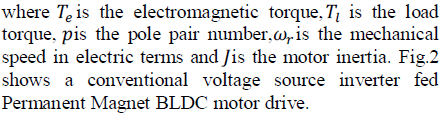 |
B. PID Controller |
In the absence of knowledge of the underlying process,
a PID controller has historically been considered to be
the best controller. |
As shown in fig.2. is a typical inverter drive system for
a BLDC motor. The switches used are IGBT. Typical
waveforms for a BLDC motor with trapezoidal flux
distribution are shown in fig.3. Approximately, the back EMF is constant for 120°, before and after which
it changes linearly with rotor angle. In order to get
constant output power and consequently constant
output torque, current is driven through a motor
winding during the flat portion of the back EMF
waveform. |
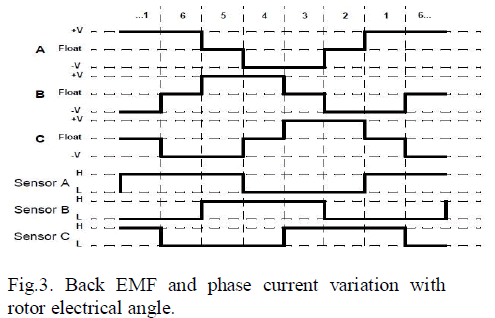 |
The closed loop speed control of BLDC motor is
achieved by the use of PID controller in association
with GA optimization. The
PIDcontrollercalculationalgorithminvolvesthreeseparat
econstantparameters, and is accordingly sometimes
called three-term control: the proportional, the integral
and derivative values, denoted P,I, and D. Simply put,
these values can be interpreted in terms of time. P
depends on the present error, Ion the accumulation of
past errors, and Disaprediction of future errors, base
concurrent rate of change. The weighted sum of these
three actions is used to adjust the process via a control
element such as the position of a control valve,
adamper,or the power supplied to a heating element. |
By tuning the three parameters in the PID controller
algorithm, the controller can provide control action
designed for specific process requirements. The
response of the controller can be described in terms of
the responsiveness of the controller to an error, the
degree to which the controller overshoots the set point,
and the degree of system oscillation. Note that the use
of the PID algorithm for control does not
guarantee optimal control of the system or system
stability. |
The three types of controllers are combined together to
form a PID controller. The PID controller is a device
which produces an output signal, u(t), consisting of
three terms, one proportional to the input signal, e(t),
another one proportional to the integral of input signal,
e(t), and the third one proportional to the derivative of
the input signal, e(t).In PID controller; |
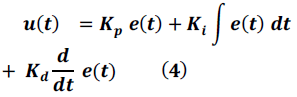 |
The transfer function of PID controller is given by
equation (5). |
 |
 |
As the PID controller have the combined effect of all
the three control actions, the introduction of PID
controller provides many advantages as it fuses the
properties of P, PI and PD controller, it stabilizes the
gain, reduces the steady state error, implementation
costs are relatively cheap and are flexible, reduces the
peak overshoot of the system and can work effectively
with Genetic Algorithm optimization approach. |
C. Genetic Algorithm |
Genetic Algorithms (GA’s) are a stochastic global
search method that mimics the process of natural
evolution. The genetic algorithm starts with no
knowledge of the correct solution and depends entirely
on responses from its environment and evolution
operators to arrive at the best solution. By starting at
several independent points and searching in parallel,
the algorithm avoids local minima and converging to
sub optimal solutions. In this way, GAs have been
shown to be capable of locating high performance
areas in complex domains without experiencing the
difficulties associated with high dimensionality, as
may occur with gradient decent techniques or methods
that rely on derivative information. |
A genetic algorithm is typically initialized with a
random population consisting of between 20-100
individuals. This population (mating pool) is usually
represented by a real-valued number or a binary string
called a chromosome.How well an individual performs
a task is measured is assessed by the objective
function. The objective function assigns each
individual a corresponding number called its
fitness.The fitness of each chromosomeisassessed and
asurvivalofthe fittest strategy isapplied. |
In this project, the magnitude of the error will be used
to assess the fitness of each chromosome.There are
three main stages of a genetic algorithm; these are
known as reproduction, crossover and mutation. The steps involved in Genetic Algorithm are shown in the
form of a flow chart in the fig.4 as shown below. It
includes the processes of reproduction, crossover and
mutation. By the fig.4, it shows the working of genetic
algorithm in the proposed project. The parameter used
here is the position of rotor of BLDC motor as given
by the Hall Effect sensor. |
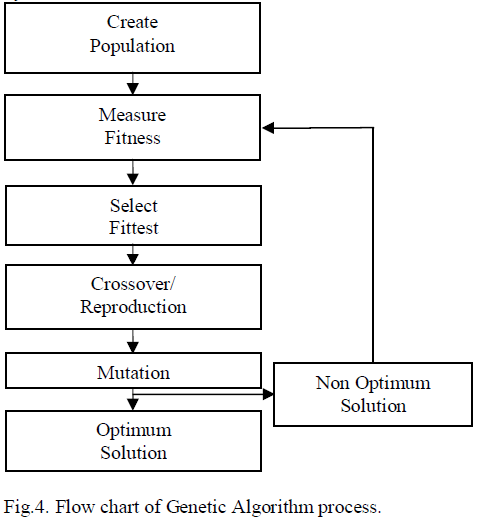 |
The steps involved in creating and implementing a
genetic algorithm are as follows: |
1. Generate an initial, random population of
individuals for a fixed size. |
2. Evaluate their fitness. |
3. Select the fittest members of the population. |
4. Reproduce using a probabilistic method (e.g.,
Roulette wheel). |
5. Implement crossover operation on the reproduced
chromosomes (Choosing probabilistically both
the crossover site and the ‘Mates’). |
6. Execute mutation operation with low probability. |
7. Repeat step 2 until a predefined convergence
criterion is met. |
The convergence criterion of a genetic algorithm is
a user-specified condition e.g. the maximum number of
generations and here the rated speed of the BLDC
motor is specified as 500 rpm. The GA optimized PID
controller provides the necessary reference signal for
Space Vector PWM technique to the driver circuit |
D. Space Vector Pulse Width Modulation |
Space Vector Pulse WidthModulation (SVPWM) is an
algorithm which is developed for the control of Pulse
Width Modulation (PWM). It is used for the creation
of Alternating Current(AC) waveforms; most
commonly to drive 3 phase AC powered motors at
varying speeds from DC using multiple class-D
amplifiers.There are various variations of SVPWM
that result in different quality and computational
requirements.One active area of development is in the
reduction of total harmonic distortion (THD) created
by the rapid switching inherent to these algorithms. |
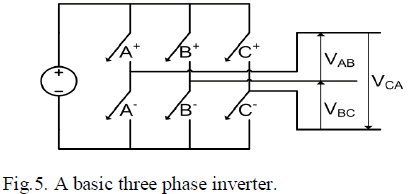 |
A three phase inverter as shown in fig.5 must be
controlled so that at no time both switches in the same
leg are turned on or else the DC supply would be
shorted. This requirement may be met by the
complementary operation of the switches within a leg.
i.e.; if A+ is on, then A− is off and vice versa. This
leads to eight possible switching vectors for the
inverter, V0 through V7 with six active switching
vectors V1 through V6 and two zero vectors V0 and V7.
To implement space vector modulation a reference
signal Vref is sampled with a frequency, fs (Ts = 1/fs).
The reference signal in this project is generated from
the GA optimized PID controller. The reference vector
is then synthesized using a combination of the two
adjacent active switching vectors and one or both of
the zero vectors. |
SIMULATION RESULTS |
The simulation of the four quadrant operation of
BLDC Motor in association with GA optimized PID
controller and Space Vector PWM method is done by
using MatLab/Simulink. The various input and output
waveforms obtained for the forward motoring mode
operation are showed below. The input voltage of 110v
is fed to the inverter andthree phase voltage output is
given to the BLDC motor. Here the various outputs are
shown with respect to the time. The operation of
BLDC Motor in four operating modes by the use of GA optimized PID controller in association with Space
Vector PWM algorithm can be clearly known from the
below showed figures [fig.6(a-e)]. |
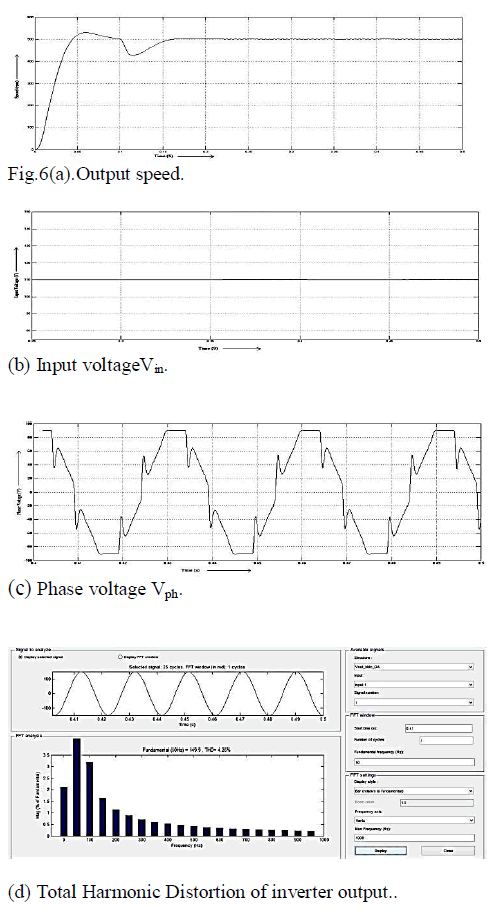 |
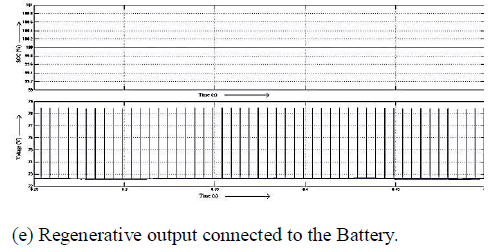 |
The output speed of BLDC Motor is found to be
controlled at a constant speed of500 rpm after a sudden
rise and fall of speed at the time of starting the motor.
The THD of the inverter output is found to be 4.26%
for one cycle of operation. The regenerative output
given to the battery is found to be 72.5 V and state of
charge is 100%, which decreases the losses in the
system. |
CONCLUSION |
This paper deals with the four quadrant speed control
of the BLDC Motor by position control of the stator
winding excitation is presented. It included the closed
loop control with the help of GA optimized PID
controller and Space Vector PWM applied to the gate
driver circuit of the inverter supplying power to the
BRUSHLESS DC Motor. The simulation results
include the performance of Space Vector PWM
technique. However PID controller works more
effectively when GA is optimized with PID controller.
Hence it can be concluded that GA and SVPWM
provides an efficient controller tuning methodology for
obtaining improved and accurate performance of the
system. |
References |
- C. SheebaJoice, S. R. Paranjothi, and V. JawaharSenthilKumar,âÃâ¬ÃÅDigital Control Strategy for Four Quadrant Operation ofThree Phase BLDC Motor With Load VariationsâÃâ¬Ã - IEEE Trans. OnIndustrial Informatics, vol. 9, no. 2, May 2013.
- Bhim Singh and SanjeevSingh,âÃâ¬ÃÅState of the art on PermanentMagnet Brushless DC Motor DrivesâÃâ¬Ã Ã¢Ãâ¬Ãâ Journal of PowerElectronics, Vol. 9,No.1, January 2009.
- Francis BoafoEffah, Patrick Wheeler,JonClareand Alan Watson,âÃâ¬ÃÅSpace-Vector-Modulated Three-Level InvertersWith a Single ZSource NetworkâÃâ¬Ã Ã¢Ãâ¬Ãâ IEEE Trans. on Power Electronics, vol. 28, no.6, June 2013.
- Alin Ãâø Stirban, Ion Boldeaand Gheorghe-Daniel Andreescu,âÃâ¬ÃÅMotion-Sensorless Control of BLDC-PM Motor With OfflineFEM-Information-Assisted Position and Speed ObserverâÃâ¬Ã Ã¢Ãâ¬ÃâIEEETrans. on Industry Applications, vol. 48, no. 6, November/December2012.
- AnandSathyan, Nikola Milivojevic, Young-Joo Lee, MaheshKrishnamurthy and Ali Emadi, âÃâ¬ÃÅAn FPGA-Based Novel DigitalPWM Control Scheme for BLDC Motor DrivesâÃâ¬Ã - IEEE Trans. OnIndustrial Electronics, vol. 56, no. 8, August 2009.
- Changliang Xia, Zhiqiang Li, and TingnaShi,âÃâ¬ÃÅA control strategyfor four-switch three-phase brushless DC motor using single currentsensorâÃâ¬Ã -IEEE Trans.On Industrial Electronics,vol. 56, no. 6, June2009.
- E. Afjei, O. Hashemipour, M. A. Saati and M. M. Nezamabadi,âÃâ¬ÃÅA new hybrid brushless DC motor/generator without permanentmagnetâÃâ¬ÃÂ- IJE Transactions B: Applications Vol. 20, No. 1, April2007.
- Chung-Wen Hung, Cheng-Tsung Lin, Chih-Wen Liu and Jia-YushYen,âÃâ¬ÃÅA Variable-Sampling Controller for Brushless DCMotorDrives With Low-Resolution Position SensorsâÃâ¬ÃÂ-IEEE Trans. OnIndustrial Electronics, vol. 54, no. 5, October 2007.
- VladGradinaru, Lucian Tutelea and Ion Boldea, âÃâ¬ÃÅBLDCâÃâ¬ÃâSPMMotor Drive with DCâÃâ¬ÃâDC Converter in the DC Link: Hall Sensorversus Sensorless Speed ControlâÃâ¬Ã - 12th International Conference onOptimization of Electrical and Electronic Equipment, OPTIM 2010.
- Ian Griffin and Ms. Jennifer Bruton, âÃâ¬ÃÅOn-line PID ControllerTuning using Genetic AlgorithmsâÃâ¬ÃÂ, 22/08/03.
|