-Power management has been one of the most talked about topics in the past decade or so because of the decrease in the energy reserves. Power shutdown is a major problem now-a-days and it occurs because a lot of power is wasted in industries. My project, ENERGY MONITORING SYSTEM deals with this problem in a simple and effective way by auditing the energy usage in industries. It checks power shut downs by knowing the large amount of energy wasted in industries. I perform all this in an automated process. In ENERGY MONITORING SYSTEM, Energy Meters, PLC’s and PC’s are used for performing its operations. Multiple energy meters with a single PLC which in turn connects with a PC. VB - serial communication is used to facilitate the communication between the PLC and PC. Several PLC's in a network can also be used. The network is obviously connected using RS-485 cables, which provide universality. But PC's are only compatible with RS-232. Hence we connect a converter (that converts RS-485 to Ethernet) between the network of PLC's and the PC. SCADA- Supervisory Control and Data Acquisition of industrial processes used for serial communication to facilitate communication between the programmable logical controllers and computer.
INTRODUCTION |
Over the past two decades, the electric power industry’s involvement in power Distribution Automation (DA) has
been principally focused on remote monitoring and control of the distribution systems and their equipments. Advance in
metering and communications have meant that electric power utilities worldwide are increasingly adopting the monitoring
technology of energy monitoring system to provide better and more efficient services to electric consumers.In order to
establish communication between the electricity meter and the calculation of utility, Programmable logic controllers (PLC)
can be used. |
Development of an online energy monitoring system via PLCs in environment by the use of |
• Data Acquisition |
• Communication Protocol |
• Processing within Energy Meter and host central station. |
The objectives of this project is |
Easiest way for energy auditing process |
Reduce the manual cost |
Online energy consumption calculation |
Energy Consumption Monitoring using graphs. |
LITERATURE SURVEY |
The adoption of Internet and Intranet technologies has been rapidly spreading and existing systems are being
replaced with new systems based on these new technologies. At changing environment of the power system industry, in
1999 Toshiba announced a concept of new middleware for power system network control systems including energy
management systems (EMS), supervisory control and data acquisition systems (SCADA), and distribution management
systems (DMS). This new middleware is based on latest Internet and Intranet technologies, offering the real-time
operation and high reliability required for network control systems. Several systems are being manufactured, and some of
which are already at the stage of commissioning tests. This paper focuses on a SCADA system for the ultra high voltage
equipment pilot plant of Tokyo Electric Power Corp. (TEPCO) which has been working since December 2000, and uses
Intranet technologies, with an emphasis on a functional overview and the features of the newly developed system. |
The impact of new technology on energy management systems and SCADA: |
The energy management system (EMS) is the centre of the control system for a power system. EMS
extends the scope of the supervisory control and data acquisition (SCADA) systems by the provision of power application
software to assist the operator in report monitoring and control of the electrical network. With the emergence of high
powered personal computers, EMS functions have moved to PC bases. |
DESIGN AND IMPLEMENTATION OF WEB BASED REMOTE SUPERVISORY CONTROL AND
INFORMATION SYSTEM |
There is a great deal of benefits for process plants in adopting the Internet to control systems. Over the years, there
has been constant increase in the development of industrial automation through remote monitoring and diagnosis virtually.
By surveying down the existing remote monitoring system used for process plant equipment, this system tends to focus on
the recent trends and developments in the control of equipments and devices in the industries by remote monitoring through
Internet. The Internet based automation is made possible by the use of Programmable Logic Controller (PLC),
Supervisory Control and Data Acquisition (SCADA), Virtual Private Network (VPN) and other network elements. The
objectives of remote monitoring and diagnosis are prevention of unplanned downtime, making optimal control operation
and maximizing the operational life of plant assets. An online integrated web based remote supervisory control and
information system takes real-time data on process control unit’s performance and helps the remote expert for further
analysis and thereby supports the plant engineer. The design, Internet security and user interface challenges are focused in
this project. |
SYSTEM SPECIFICATION |
Hardware Requirements: |
• Delta PLC |
• RS232 Converter |
• Energy Pulses by DM52 Series Energy Meter |
Software Requirements: |
• Ladder programming for PLC. |
• King view 6.53 for SCADA view |
BLOCK DIAGRAM: |
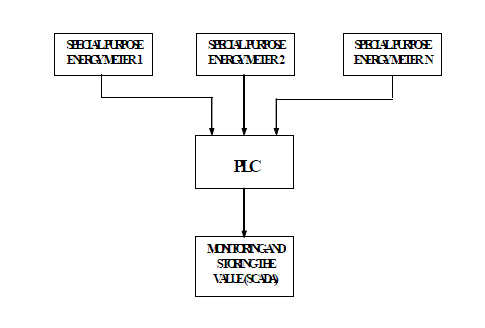 |
BLOCK DESCRIPTIONS ENERGY METERS |
An electricity meter or energy meter is a device that measures the amount of electric energy consumed by a
residence, business, or an electrically powered device. Electricity meters are typically calibrated in billing units, the most
common one being the kilowatt hour [kWh]. Periodic readings of electric meters establishes billing cycles and energy used
during a cycle. In settings when energy savings during certain periods are desired, meters may measure demand, the
maximum use of power in some interval. "Time of day" metering allows electric rates to be changed during a day, to record
usage during peak high-cost periods and off-peak, lower-cost, periods. Also, in some areas meters have relays for demand
response shedding of loads during peak load periods. |
3Ø Electronic Energy Meters - DM 52 series: Direct measurement of energy consumption, no external multiplication factor
required. Can be hooked on to an Energy Management System, SCADA, PLC, DCS.
Multiplying Factor (MF):The meter is calibrated for particular CT, PT ratio as mentioned on the terminal block. When the
meter is used with CT, PT of the same ratio, MF is either 0.01 or 0.1 or 1.0 or 10.0 or 100.0. A decimal point has been
placed on the 9 digit (6 moving and 3 dummy digits) depending on the MF. While noting the energy readings, the 9 digit
energy readings need to be taken including the decimal point. |
Applications: |
• Electrical Panels |
• Test Benches |
• Wind Energy |
• Co-Generation |
• Genset Panels |
• Lab Equipment |
• Power Plants |
• All types of Industries |
• Load Centers |
Features: |
• True RMS |
• Low PT, CT burden |
• Accuracy class 1.0 IEC 61036 & Class 0.5 |
• Simultaneous sampling of Volts & Amps |
• Accurate on distorted waveforms |
• Sealed dust-proof construction |
Pulse Output Feature: Optically Isolated, Solid-state NO Contact gives digital pulse output to drive Remote Counter,
PLC, DCS Station etc. for off line monitoring of Energy Data, on line control for Energy/Power/Process optimisation,
correlating Energy Input to product output etc. |
PLC: |
A programmable logic controller (PLC) or programmable controller is a digital computer used for automation of
electromechanical processes, such as control of machinery on factory assembly lines, amusement rides, or light fixtures.
PLCs are used in many industries and machines. Unlike general-purpose computers, the PLC is designed for multiple
inputs and output arrangements, extended temperature ranges, immunity to electrical noise, and resistance to vibration and
impact. Programs to control machine operation are typically stored in battery-backed-up or non-volatile memory. A PLC is
an example of a hard real time system since output results must be produced in response to input conditions within a limited
time, otherwise unintended operation will result. |
DESCRIPTION |
PLCs are often defined as miniature industrial computers that contain hardware and software that is used to perform
control functions. A PLC consists of two basic sections: the central processing unit (CPU) and the input/output interface
system. The CPU, which controls all PLC activity, can further be broken down into the processor and memory system. The
input/output system is physically connected to field devices (e.g., switches, sensors, etc.) and provides the interface
between the CPU and the information providers (inputs) and controllable devices (outputs).PLC (Programmable Logic
Controller) is an electronic device, previously called “sequence controller”. In 1978, NEMA (National Electrical Manufacture Association) in the United States officially named it as “programmable logic controller”. PLC reads the status
of the external input devices, e.g. keypad, sensor, switch and pulses, and execute by the microprocessor logic, sequential,
timing, counting and arithmetic operations according the status of the input signals as well as the pre-written program
stored in the PLC. The generated output signals are sent to output devices as the switch of a relay, electromagnetic valve,
motor drive, control of a machine or operation of a procedure for the purpose of machine automation or processing
procedure. The peripheral devices (e.g. personal computer/handheld programming panel) can easily edit or modify the
program and monitor the device and conduct on-site program maintenance and adjustment. The widely used language in
designing a PLC program is the ladder diagram. With the development of the electronic technology and wider applications
of PLC in the industry, for example in position control and the network function of PLC, the input/output signals of PLC
include DI (digital input), AI (analog input), PI (pulse input), NI (numeric input), DO (digital output), AO (analog output),
and PO (pulse output). Therefore, PLC will still stand important in the industrial automation field in the future. |
CONTENTS OF PLC: |
• History of Programmable Controllers |
• Relay Ladder Logic |
• Central Processing Unit |
• Input/Output System |
• Programming and Peripheral Devices. |
MAJOR COMPONENTS OF A COMMON PLC: |
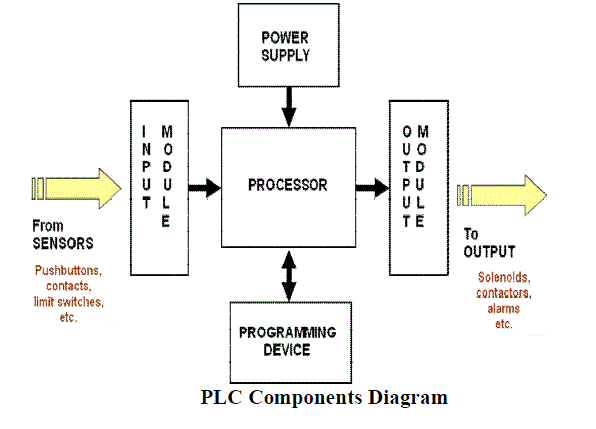 |
PLC EXECUTION: |
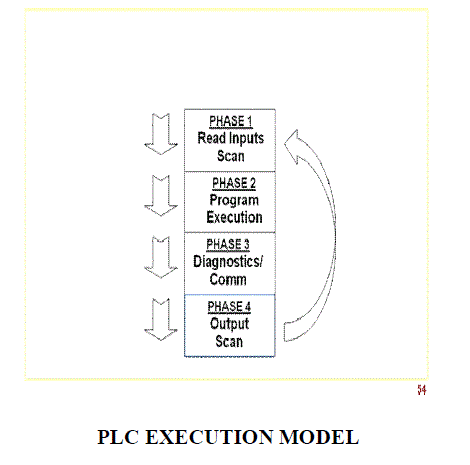 |
AREAS OF APPLICATION: |
• Manufacturing / Machining |
• Food / Beverage |
• Metals |
• Power |
• Mining |
• Petrochemical / Chemical |
ADVANTAGES OF PLCS: |
• Less wiring. |
• Wiring between devices and relay contacts are done in the PLC program. |
• Easier and faster to make changes. |
• Trouble shooting aids make programming easier and reduce downtime. |
• Reliable components make these likely to operate for years before failure. |
SCADA: |
An industrial SCADA system will be used for the development of the controls of the four LHC experiments. This
paper describes the SCADA systems in terms of their architecture, their interface to the process hardware, the functionality
and the application development facilities they provide.Widely used in industry for Supervisory Control and Data
Acquisition of industrial processes, SCADA systems are now also penetrating the experimental physics laboratories for the
controls of ancillary systems such as cooling, ventilation, power distribution, etc. |
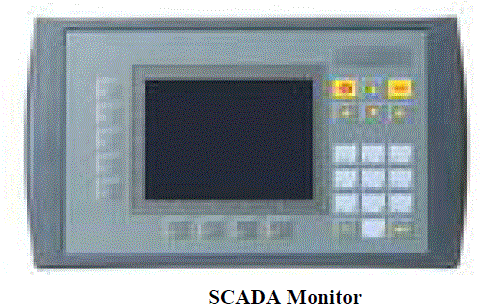 |
SCADA systems have made substantial progress over the recent years in terms of functionality, scalability,
performance and openness such that they are an alternative to in house development even for very demanding and complex
control systems as those of physics experiments. |
TYPES OF SCADA: |
1. D+R+N ( Development +Run + Networking) |
2. R+N ( Run +Networking ) |
3. Factory focus |
MANUFACTURE OF SCADA: |
Modicon (Telemecanique) Visual look |
Allen Bradly : RS View |
Siemens : win cc |
KPIT : ASTRA |
Intelution : Aspic |
Wonderware : Intouch |
WHAT DOES SCADA MEAN? |
SCADA stands for Supervisory Control And Data Acquisition. As the name indicates, it is not a full control
system, but rather focuses on the supervisory level. As such, it is a purely software package that is positioned on top of
hardware to which it is interfaced, in general via Programmable Logic Controllers (PLCs), or other commercial hardware
modules. |
SCADA systems are used not only in industrial processes: e.g. steel making, power generation (conventional and
nuclear) and distribution, chemistry, but also in some experimental facilities such as nuclear fusion. The size of such plants
range from a few 1000 to several 10 thousands input/output (I/O) channels. However, SCADA systems evolve rapidly and
are now penetrating the market of plants with a number of I/O channels of several 100 K: we know of two cases of near to 1
M I/O channels currently under development. |
SCADA systems used to run on DOS, VMS and UNIX; in recent years all SCADA vendors have moved to NT
and some also to Linux. |
OVERVIEW OF THE PROJECT |
Readings from n - energy meters are collected automatically by the PLC's, PLC1 to PLCm and the data from each PLC is
sent to a RS485 to Ethernet Converter (to make the readings compatible with Computers). |
From the converter, the data is fed into a hub, so that many PC's can have access to the data. |
Further, a copy of the data is also sent to the database server (Back-end) to update the database. |
The database server can then provide the user with front end services through VB. |
I have also use VB - serial communication to facilitate communication between the PLC and PC. |
FUTURE TECHNOLOGY |
Automation of the energy management system has to be achieved. I have also enable the world-wide access of the
energy management system by connecting to internet by Changing resident PLC programs – uploading/downloading from a
supervisory controller (Laptop or desktop computer). Forcing I/O points and memory elements from a remote terminal.
Linking a PLC into a control hierarchy containing several sizes of PLC and computer. RS 232 used in short-distance
computer communications, with the majority of computer hardware and peripherals. Has a maximum effective distance of
approx. 30 m at 9600 baud. King SCADA also provides abundant graphical development tools, stunning graphics elements
and others which compose a facilitated developing environment.Remote Terminal System (RTU), database, historical
database and other system together, it can provide a powerful guarantee to complete the construction enterprise information
system. |
References |
- "Handbook for Electricity Metering" by The Edison ElectricInstituteâÃâ¬ÃâThe Bible of electric meters, continuously updated since electricity was discovered.
- S.K.Goudos ,V. Peristeras, and K.A.Tarabanis, âÃâ¬ÃÅSemantic Web Application for Public Administration using OWL for Public Domain Data Knowledge RepresentationâÃâ¬Ã WSEAS Transactions on Information Science &Application.Vol.4(4),pp.725-730,2007
- R. Kimball, and M.Ross,âÃâ¬ÃÂThe Data Warehousing Toolkit: The Complete Guide to Dimensional ModelingâÃâ¬Ã John Wiley,2002.
- T.B.Pedersen , âÃâ¬ÃÅWarehousing The World :A Vision for Data Warehouse Research âÃâ¬Ã New Trends.
- ZaferAydogmus, OmurAydogmus, âÃâ¬ÃÅA Web-Based Remote Access Laboratory Using SCADAâÃâ¬ÃÂ, IEEE Transactions on education, Vol. 52, No. 1, February 2009, pp. 126-132.
- XinZhao , Wei Liang , âÃâ¬ÃÅResearch on the Remote Monitoring and Intelligent Fault Diagnosis System âÃâ¬ÃÅ, Sch. Of Computer & Electronic Eng., Hunan University of Commerce, Changsha , Wireless Communications,Networking and Mobile Computing(WiCOMâÃâ¬Ãâ¢08), 2008 , pp.1-4.
- D .Y. RaghavendraNagesh, Sowjanya A and Dr S.S TulasiRam, âÃâ¬ÃÅ Real Time Decision Support for EnergyManagement âÃâ¬ÃÅ, Proceedings of the World Congress on Engineering 2008, Vol.1., pp. 5-9.
- Chengen Wang , LidaXu , WuliangPeng , âÃâ¬ÃÂConceptual design of remote monitoring and fault diagnosis systemsâÃâ¬Ã ,Science Direct (Information Systems) ,Vol.32, 2007, pp. 996-1004.
- Shin Bong-Cheol, Kim Gun-Hee, Choi Jin-Hwa, JeonByung-Cheol, Lee Honghee, Cho Myeong-Woo, Han Jin-Yong, Park Dong-Sam, âÃâ¬ÃÅA Web-based machining process monitoring system For E-manufacturing implementationâÃâ¬ÃÂ,Journal of Zhejiang University Science, Vol.7 (9), 2006, pp. 1467-1473.
- Adnan Salihbegovic, VlatkoMarinkovic, ZoranCico, Elvedin Karadzic, NinaDelic, âÃâ¬ÃÅWeb based multilayereddistributed SCADA/HMI system in refinery applicationâÃâ¬ÃÂ, Elsevier Science, Vol.31, 2009, pp. 519-612
- EnginOzdemir, MevlutKaracor,âÃâ¬ÃÂMobile phone based SCADA for industrial automationâÃâ¬ÃÂ, ISA Transactions,Vol. 45, No. 1, 2006, pp. 67âÃâ¬Ãâ75
- Henry Wu, David P. Buse, JunqiuFeng, Pu Sun, âÃâ¬ÃÅe-Automation, an Architecture for Distributed IndustrialAutomation SystemsâÃâ¬ÃÂ, International Journal of Automation and Computing, Vol. 1, 2004, pp. 17-25.
- Dr. AdityaGoel& Ravi Shankar Mishra,âÃâ¬Ã Remote Data Acquisition Using Wireless âÃâ¬Ãâ SCADA SystemâÃâ¬ÃÅ, InternationalJournal of Engineering (IJE), Vol.3 (1), 2008, pp. 58-65
- Albert W.L. Yao, C.H. Ku, âÃâ¬ÃÅDeveloping a PC-based automated monitoring and control platform for electricpower systemsâÃâ¬ÃÂ, Electric Power Systems Research, Vol. 64, 2003, pp. 129-136
- Toshiaki Kimuraa, Yuichi Kandab, âÃâ¬ÃÅDevelopment of a remote monitoring system for a manufacturing supportsystem for small and medium-sized enterprises âÃâ¬ÃÅ, Computers in Industry, Vol.56, 2005, pp.3-12
- Juan Jose Gonzalez de la Rosa Antonio Moreno Munoz, Aurora Gil de Castro, Victor Pallares Lopez &JoseAntonio Sanchez Castillejo,âÃâ¬Ã A web-based distributed measurement system for electrical power quality AssessmentâÃâ¬ÃÂ,Elsevier Science, Vol. 43, 2010, pp. 771-780
- Hongbo Lana, YuchengDinga, Jun Honga, HailiangHuangb, BinghengLua,âÃâ¬Ã A web-based manufacturing servicesystem for rapid product developmentâÃâ¬ÃÂ, Elsevier Science, Vol.54, 2004, pp. 51-67
- CihanSahin&EmineDogruBolat, âÃâ¬ÃÅDevelopment of remote control and monitoring of web-based distributed OPCsystemâÃâ¬ÃÂ, Elsevier Science, Vol.31, 2009, pp. 984-993
- A.W.L. Yao, âÃâ¬ÃÅDesign and implementation of Web-based diagnosis and management system for an FMSâÃâ¬ÃÂ,International Journal of Advanced Manufacturing Technology, Vol.26, 2005, pp.1379-1387
- Automation Quality and Testing Robotics (AQTR), 2010 IEEE International Conference on 28-30 May 2010,Author(s): Balogh, S.Corha, A. ; Stancel, E. ; Gyurka, B. ; Vigu, C. ; Ignat, S.Volume: 3 Page(s): 1 âÃâ¬Ãâ 5.
|