With the advent of sophisticated greenhouse technologies, computerized greenhouse has naturally become imperative. It has created new opportunities to manipulate the indoor environment according to the specific needs of plants. The temperature under greenhouse is the most influential factor on the plants. Usually, it has been closely correlated with the other climatic parameters. This paper examines new ways to control internal greenhouse temperature using two types of controllers: PID and PI-intelligent. The two controllers give good results, except that the PID requires a method of parameters identification, which should be valid for a large time as possible. It is therefore necessary to repeat the chosen identification technique face to change unexpected of external parameters. However, the PI-intelligent controller permits to keep the adjusted gain for a long time thanks to actualised identification and resulted by algebraic method. In order to visualize the evolution of climatic parameters in real time, a graphic interface has been developed.
Keywords |
Computerized Greenhouse, Climatic parameters, Control, PID controller, PI-intelligent. |
INTRODUCTION |
For several years, studies on greenhouse climate controlling have made a challenge of several research tasks. Many
control methods are proposed in literature: (Rodríguez et al. (2001); Bennis et al. (2008)) designed a feedforward
controller for greenhouse climate control based on physical models; optimal control approaches have been proposed
(Ioslovich et al., (2009)). Adaptive control strategies for greenhouse temperature control have been addressed by
(Berenguel et al., (2003)) and (Speetjens et al. (2009)). The recently introduced model free control is proposed to
control the temperature under greenhouse. It is a simple but efficient technique for the nonlinear, unknown or partially
known dynamics. While retaining the PID reduced computational cost, it is able to cope with general types of
nonlinearities. Model free control has been proven to be a simple but very efficient nonlinear feedback technique for
the unknown or partially known dynamics (Fliess et al. (2009); Fliess et al. (2013); Join et al. (2013); Lafont et al.
(2013); Lafont et al. (2014), Choi et al. (2009)). We shall here use so-called intelligent PID (or i-PID). While retaining
the PID reduced computational cost, it is able to cope with general types of nonlinearities. A precise relationship
between i-PID and PIDs is given in (d’Andréa-Novel et al. (2010)). It particularly emphasizes the ease of tuning of i-
PID gains and gives a clearcut explanation of the performance of usual PIDs. |
Greenhouses were been designed for plant cultivation in controlled environmental conditions. Greenhouse cultivation
has several advantages: it helps to maintain an optimal plant growth environment and protects the crops from pests and varying outdoor conditions. Therefore, the production in greenhouses becomes considerably sophisticated and
excessively expensive. For that, the greenhouse growers who want to remain competitive need to maximize their
investment through the better management of production conditions. In order to exploit the adequate opportunities for
crops, it is necessary to control the system in automatic way. The introduction of automatic techniques using computer
has been a major advance for agricultural production (Yang et al. (2013); Eredics (2009)). In fact, there are three basic
components in a greenhouse climate control: sensors, computer, and actuators. Sensors were be used to collect
information that are important for plant growth and actuators were be used to modify the collected information. The
management of the greenhouse environment is strongly reliant on temperature variation. This later is the result of
complex, interactive heat, mass exchanges between the inside air and the several elements of the greenhouse and the
outside climatic parameters. The process depends on the structure of the greenhouse type, the state of the crop and the
actuating control signals typically ventilation and heating which are able to modify the inside temperature conditions.
The various orders (heating and ventilating) of a greenhouse aim at the spontaneous improvement of the internal
climate, but this control is never complete. It is difficult in fact to act on an element of the environment without
modifying another element. |
In our laboratory, the studies showed that the inside temperature is the most influential parameters on the greenhouse
(Ezzine et al. (2010)). However, the automatic climate control requires the development of appropriate control laws that
are based on models representing linear and nonlinear system. We are therefore forced to make a study of the system to
control the temperature under greenhouse. To fully exploit the enhanced possibilities for crop and resource
management in greenhouse, it is indispensable to adjust and control variables with a remote automatic controlling (El
Afou1 et al. (2013); El Afou2 et al. (2013); Guerbaoui et al. (2013)). |
The result presented in this work is the implementation of a new control strategy of climatic parameters under
greenhouse. The proposed strategy is the PI-intelligent controller which compared with a classical PID controller. The
reader may consult the recent book (Van Straten et al. (2011)) for a comprehensive approach for modelling and for
optimal control (Iya et al. (2009)) that falls within a framework of modelling/ identification/ control. The controller
strategies are programmed using Matlab/Simulink software. |
This paper is organized as follows: the following section describes the experimental framework of the argument. A
brief presentation of model-free controller approach was presented. We describe the implementation of the controllers
and present the main experimental results. |
AN OVER VIEW OF THE EXPERIMENTAL GREENHOUSE |
Figure 1 presents a schematic view of the greenhouse system. The establishment of the greenhouse was made in order
to develop an integrated data acquisition system to control the inside climate. The system is linked to a computer (PC).
Sensors and conditioning modules allow us to measure the different climatic parameters inside and outside the
greenhouse. The acquisition and data processing has been developed by a multi-function card NI-6024E to control and
manage complex measurements. This experimental greenhouse has been equipped with many sensors: |
- Sensors of inside and outside temperature (LM35DZ), data are expressed in °C. |
- Sensors of inside and outside humidity (HIH-4000-001), data are expressed in %. |
- Sensor of carbon dioxide concentration (Figaro AM4 module), data are expressed in ppm and named CO2. |
In order to improve the climate under greenhouse, we have installed a heating system, pulsed air supply and a variable
speed fan (Ed-Dahhak et al. (2007); Lachhab et al. (2007); Ed-Dahhak et al. (2009); Guerbaoui et al. (2011)). |
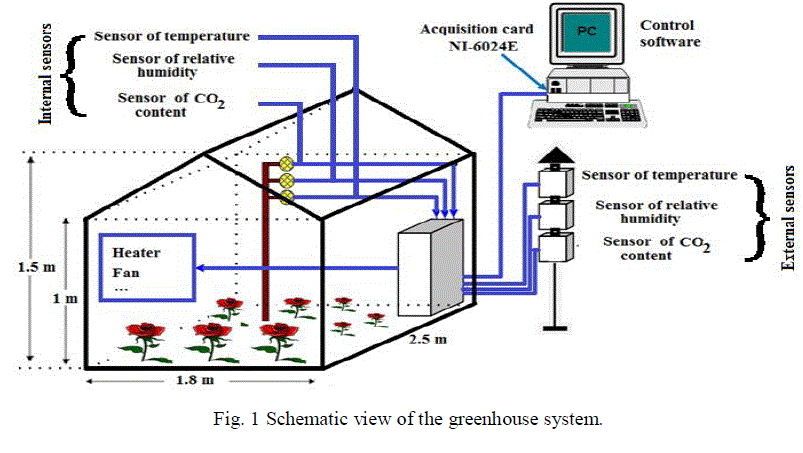 |
THEORITICAL STUDY OF THE USED CONTROLLERS |
A. PID Controller |
PID control is the method of feedback control that uses the Proportional, the Integral and the Derivative as the main
tools (Hensel et al. 2012, Beshi et al. 2011 and 2012). The purpose of control is to make the process variable y(t) as a
suitable value named set-point yr(t). To achieve this purpose, the manipulated variable u(t) is changed at the command
of the controller. In the present application, the process variable y(t) is the temperature and the manipulated variable
u(t) is the command of the controller. The “disturbance” is any factor, other than the manipulated variable, that
influences the process variable. In some applications, however, a major disturbance enters the process in a different
way, or plural disturbances need to be considered. The error e(t) is defined as: e(t) = yr(t) – y(t). Where, yr(t) is the
desired trajectory and y(t) is the measured variable. The PID is a controller that takes the present, the past, and the
future of the error into consideration. After digital implementation was introduced, a certain change of the control
system structure was proposed and was adopted in many applications. However, that change doesn’t influence the
essential part of the analysis and design of the PID controllers. The transfer function C(s) of the PID controller is: |
 |
B. PI-intelligent controller |
This section summarizes briefly the idea of model-free control, limited to the needs of this application, the
monovariable case and the derivation of order 1. Readers might refer to the extensive bibliography on this topic,
especially since the available items (Gédouin et al. (2011), Fliess (2008, 2009); Fliess et al. (2011); Abouaissa et al.
(2011)) for the monovariable model-free control, and (Mboup et al. (2009), Liu et al. (2011)) for the derivative
estimation. The model-free control is based on a local modelling of the system, from the only knowledge of its inputoutput,
thus avoiding the sometimes-difficult steps of modelling and identification valid over wide operating range. It is
based on algebraic techniques for estimating the derivatives of noisy signals to express the derivative signal y(i)(t) as an
integral over a short interval [(t – T), t] who is developed in order one, It’s sufficient for this application. The
estimation of this derivative can take the following form: |
(2) |
In practice, the equation (2) is evaluated at each sample time, t = kTs, with k = 1, 2… and T = nsTs, with ns is the
number of samples, Ts is used in the time window T, as a discrete sum using basic discrete method to calculate
integrals: |
 |
This estimation technique can apply to a fast phenomenological model of process behaviour and valid in a short period: |
 |
(5) |
This estimation therefore allows the implementation of the PI-intelligent. When the closed loop controller is of PID
type, the model free control can be named, intelligent PID as is expressed as follows: |
 |
SIMULATION RESULTS |
A. PID controller |
The development of the model describing the evolution of the temperature under greenhouse needs to apply a step as a
setpoint for heating temperature in open loop. The transfer function obtained as a first order system with pure delay
could be expressed as follows (El Afou et al. (2013)): |
(7) |
The parameters of PID controller are tuning from the identified system (Dindeleux (1981)): |
(8) |
(9) |
(10) |
We exploit these parameters to control the model representing our system using the MATLAB software in simulation
mode. To have an idea about the behaviour of the system in closed loop where the PID controller is involved, we made
the model simulation in SIMULINK. Fig. 2 shows the obtained performances with the developed algorithm. We also
notice that the output presents a short delay of 20 s and it perfectly follows the set point of 24 °C at 225 s. |
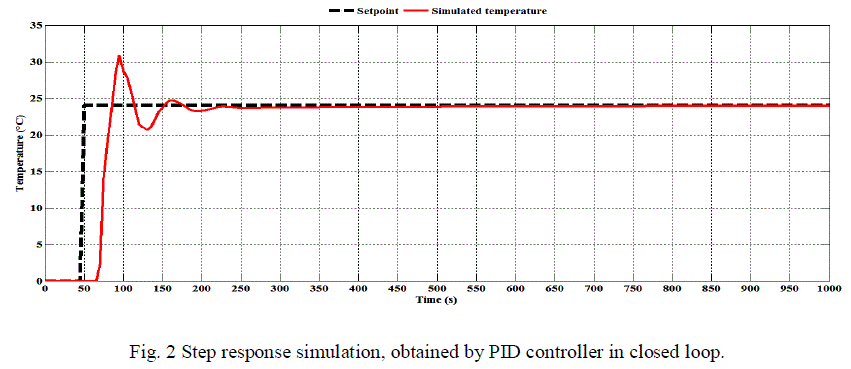 |
B. PI-intelligent controller |
Differentiation is a basic mathematical operation with a wide range of applications in many areas of science. It is
therefore important to have good methods to compute and manipulate derivatives. In our case, the new approach named
model-free control based on a derivative estimation, which we will, confirm better results even if signals are corrupted
by noise. We consider the signal y that is available through a measurement including some additional noise. The aim is
to estimate time derivatives of signal y, up to a first order, from its corrupted measurement. We can rewrite the
developed numerical derivative of the first order us follows: |
(11) |
In this application, we choice ns=11 and the simple time s Ts=5s Then the interval T= 55 s is sliding in order to get
this estimate at each instant. We translate equation (11) to algorithm of numerical derivative implemented in Simulink
as depicted in fig. 3. |
 |
In order to test this algorithm, we have compared the numerical first derivative with a simple derivative as depicted in
fig. 4. According to this schema, we can observe the existence of some similarities between the estimated numerical
derivative and the simple derivative. We conclude that the developed algorithm accurately presents a first derivative. |
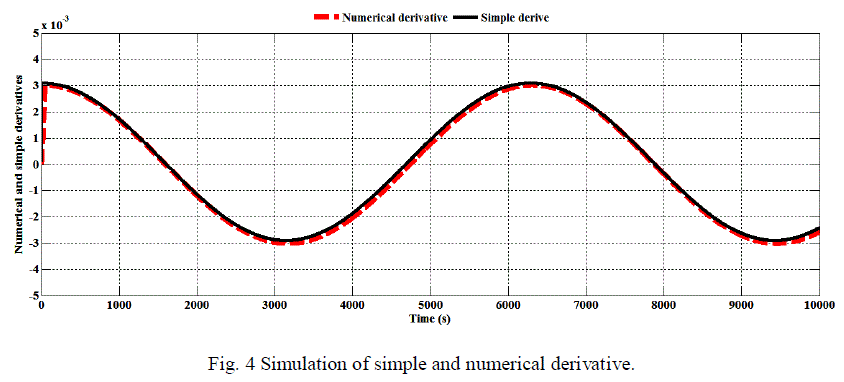 |
To go even further, we have added a white noise to the input of derivatives. Figure 5 shows the simple first derivative
and the fig. 6 presents the simulated of the first numerical derivative. It can be seen that a numerical derivation gives a
good performance. The estimated first numerical derivative is better than the simple first one. The above results are the
basis of the estimation techniques. |
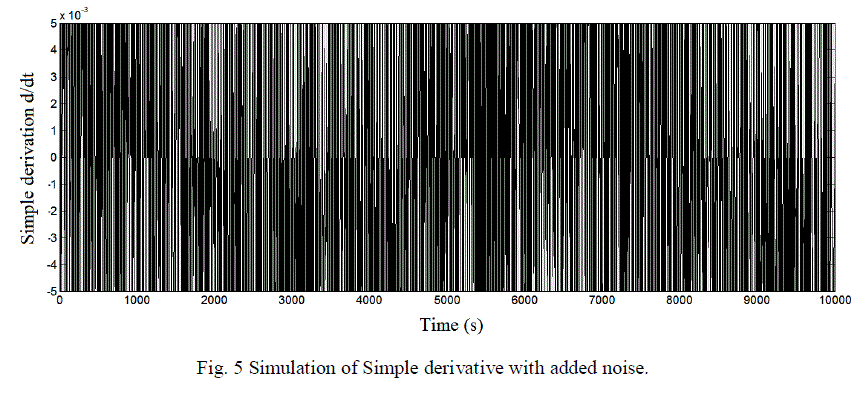 |
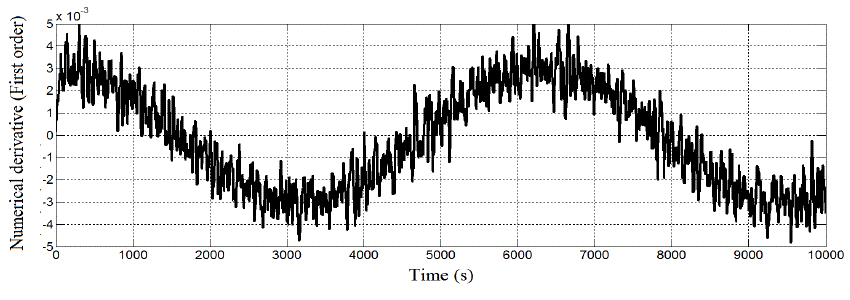 |
In this paper, the study is limited just on the control of the internal temperature. Fig 7 shows the simulation results of
step response of internal temperature obtained using PI-intelligent in closed loop. We note that the static error is equal
to zero, the system is fast (rise time tm≈ 19 s) and without overshoot. We also notice that the observed output presents at
the beginning a pure delay of 20.6 s and after a duration of 350 s, it is perfectly tracking accuracy the set-point. We can
improve the performances by tuning easily the parameters of this intelligent controller. Furthermore, these tuned
parameters can give good results whereas the setpoint implemented with noise. |
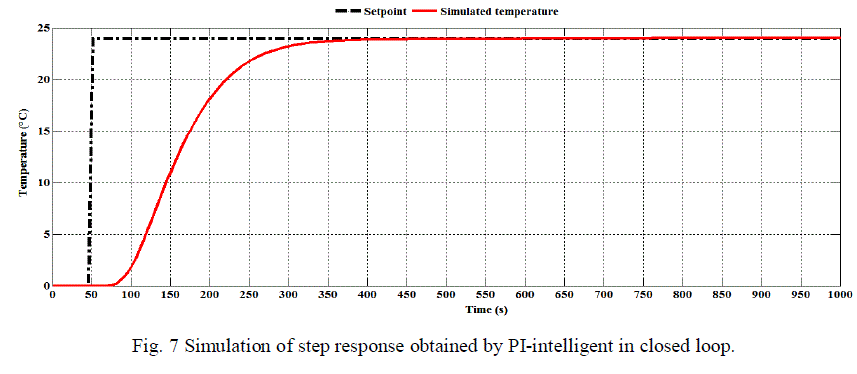 |
RESULTS OF FEEDBACK TECHNIQUES IN REAL TIME |
A. Application |
The inside temperature is the important parameter in the greenhouse and it influence most the culture under greenhouse
(Ezzine et al. (2008)). In order to control the inside temperature, we have used two actuators heater and fan. Then we
assimilate the process as a single input respectively distributed on heating and ventilation according to the value of the
inside temperature and the fixed setpoint. This hybrid process makes modeling hazardous and fully justifies the modelfree
approach proposed. In this study, the measured relative humidity and CO2 are not taken into account in the
elaboration of control strategies. Fig. 8 shows the structure of the control system. Note that, if [F]e = 0 then we obtain
the classical regulator like as the simple PID controller. |
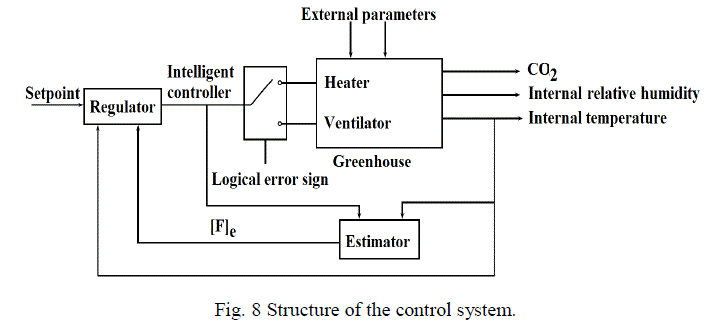 |
To make a controller in real time, we prepare an algorithm able to communicate with greenhouse process. For that,
we began by changing respectively the Input and Output of a feedback algorithm, which is presented in the mode simulation, by Analog Input and Output to apply the developed algorithm on the real system. Before running a
simulation, the SIMULINK must be built; some codes will be executed in the command window. If there is no error on
the command window, we finally connect to a target and we run simulation by start real time. |
B. PID controller |
In order to test the performance of the previous controllers, we excite the actuators (heater and fan) by several setpoints
and we measure, in real time, the temperatures response under greenhouse. Firstly, we present the closed-loop
step response of the PID controller as presented in fig. 9. We can observe that tracking is very good when the actuators
are controlled by a classical law whereas it is unsatisfactory in steady state. In addition to the strong effect of the
external climate, we can notice that the reference trajectory oscillates around a setpoint. Then, this controller isn’t
enable to reject the useless perturbations. In the fig. 9, the noises appear strongly between 7 h and 18 h. |
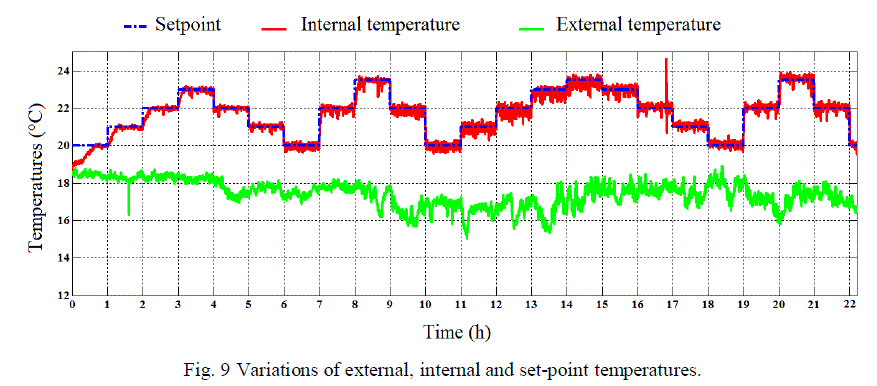 |
Furthermore, we present in the Fig. 10 the evolution of the PID controller that sent to the actuators. In the beginning,
this controller is growing and reach the maximum of 3 V at 15h. After that it remains stable around this value. That
means the used controller cannot minimise the consumed power by the actuators. Furthermore, it presents problems
overlooked lifetime of the controlled system. The poor performances are as results of the classical controllers based on
the methods of identification that are not valid for large time. Moreover, these methods the later need to be actualised
for each large variation of the external parameters climate. This is the reason why we are using the PI-intelligent
controller for monitoring temperature under greenhouse. |
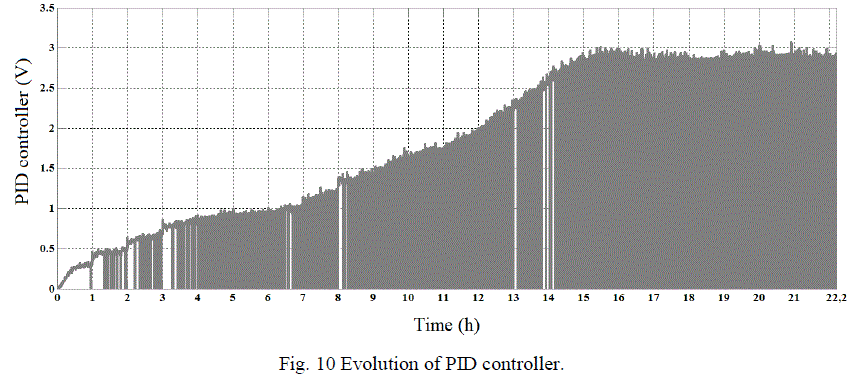 |
C. PI-intelligent controller |
Fig. 11 shows the performances of the PI-intelligent control with steps as reference trajectories that varied between
20 °C and 23.5 °C. We can observe that the perturbations are rejected faster by the PI-intelligent controller than the PID
one. Furthermore, the evolution of internal temperature demonstrates that the performances of the intelligent controller
behave better. The external temperature has presented to give the conditions where we are regulating the internal
temperature. Although a poor conditions of the closed loop with intelligent controller, it permits to obtain the good
performances. As a conclusion, the results show that the PI-intelligent controller is able to control the temperature
precisely within a reasonable range of error. Its effectiveness is appearing by minimum oscillations around a setpoint
and no overshoot. |
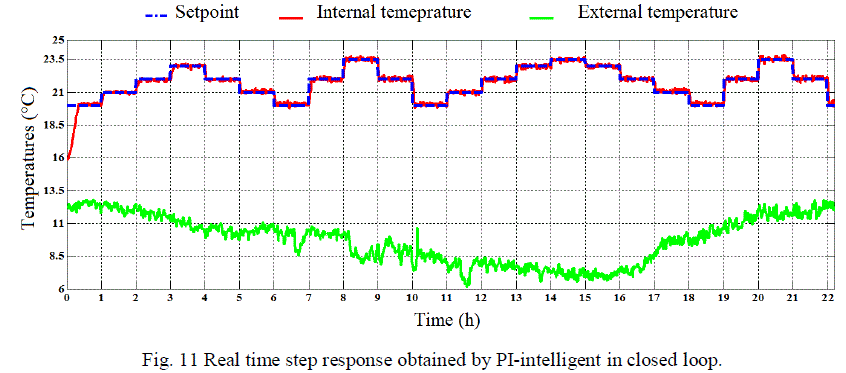 |
Similarly, we present the evolution of the PI-intelligent controller as depicted in Fig. 12. We notice that the value of the
output does not exceed 1.25 V and decrease at some times. Those good performances are obtained by the fast
phenomenological model of process behaviour and to the numerical derivative (equations 4 and 5). The later permits to
actualize the parameter F (eq. 5) that contain all of the unknown parameters of the process. To conclude, this intelligent
controller permits a good performance where we keep those parameters for large time and with a minimum power
generated for real time control signals of the actuators. |
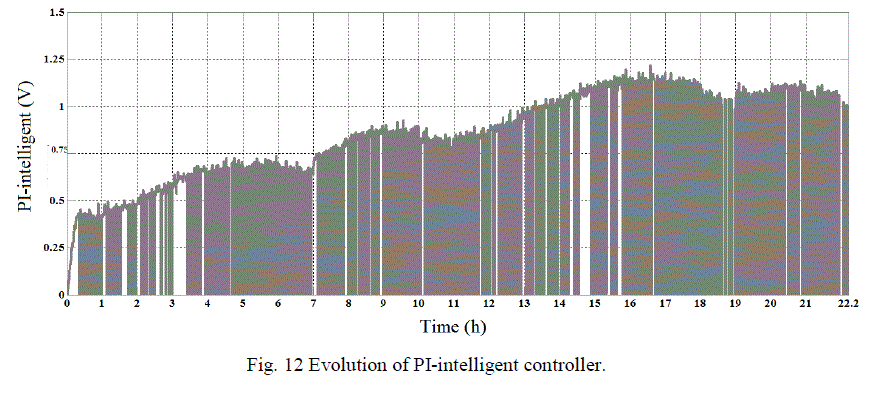 |
COMPARATIVE STUDY |
In this section, we present a comparison of the experimental results obtained by using the PID and PI-intelligent
controllers. In order to facilitate the readability of curves, we chose to present regulating temperature between 2 h and
5 h. All these were performed to monitor the internal temperature of greenhouse from 21 °C to 23 °C and also to assure
a fair comparison. The behaviour of temperature at the optimum PID values is shown in Fig. 13. Smooth theoretical
temperature behaviour is shown with slight amount of overshoot but no ripples. Experimentally, there was more
overshoot and fluctuations around the set-point. Little delay existed at the beginning of the experiment for about 20 s,
which might be attributed to the air mixing delay. The PID controller made a good tracking to set-point with values of
22 °C and 23 °C. However, the maximal error of this controller is equal 0.4 °C. We can see that the number of changes
in the control signals is small. This fact is a key issue in the actuator’s lifetime, especially in greenhouse where the
ventilation and heating systems are composed of mechanical actuators. |
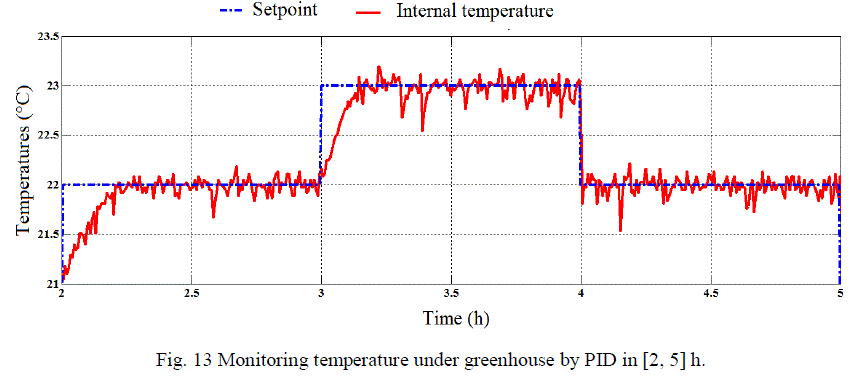 |
The optimized PI-intelligent parameter was plugged into the experimental controller as depicted in fig 14. Some
fluctuations existed in the theoretical curve at the intersection with the set-point. However, a good tracking of the setpoint
is demonstrated with a maximal error of 0.2 °C. This controller was easy to implement and was very effective in
tracking the set-point. Consequently, it made the best by means of tracking set-point. |
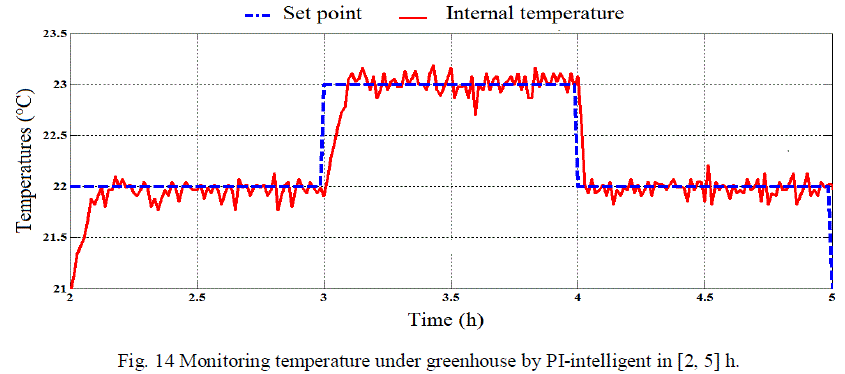 |
All controllers were able to control the greenhouse air temperatures precisely within a reasonable range of error. We
note that the values of the different initial temperatures are used because both controllers are applied under conditions
within the values of different external temperatures. This makes comparative study difficult. However, we will analyse the results to determine the advantages and inconvenient of each used controller. Figures 15 and 16 show, respectively
the evolution of commands computed by PID controller and PI- intelligent. |
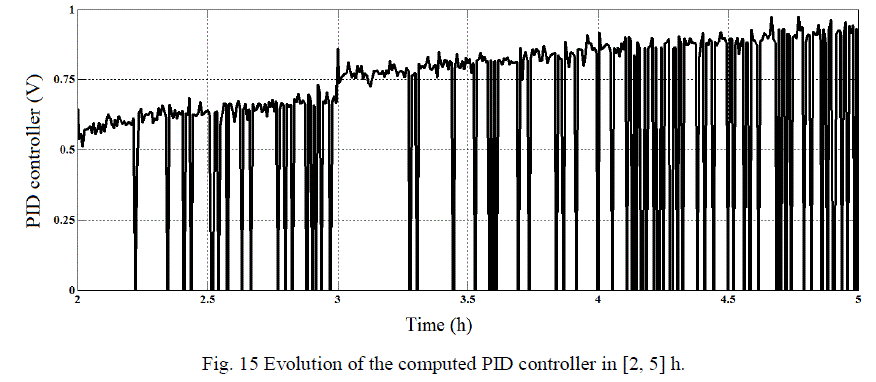 |
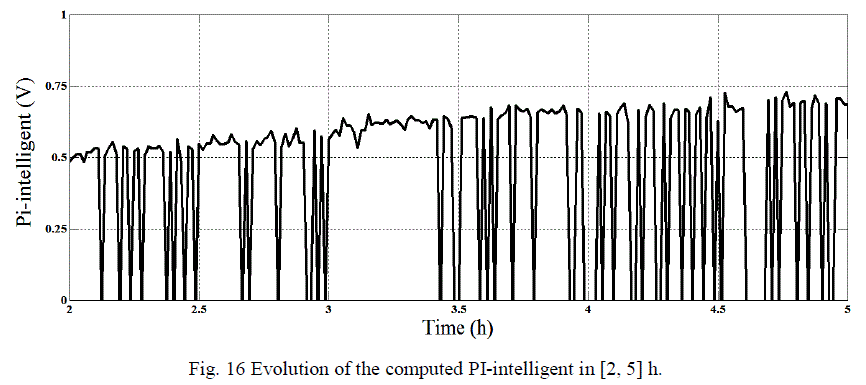 |
We note that the PID controller loses great power to reach the fixed objective. Indeed, it equals zero compared to other
orders and the number of times the command is reset and low. However, the maximum value does not exceed 1 V. For
PI-intelligent controller we note that the command is faster and stops at several moments. This evolution justifies this
intelligent controller as the best method to control the temperature in the greenhouse. Despite the good performance
obtained for the three orders, we note that the PID control begins to saturate because of the wide variation in climatic
parameters and the limitation of the validity of the identification methods used. However, we noticed that the model
free control permits to obtain a good performance, thus no saturation of used actuators. |
CONCLUSION |
This work presents the implementation of two controllers PID and PI-intelligent which were been implemented in order
to control the temperature under greenhouse. However, the tuning of several controllers in the complex greenhouse
environment is a challenge to process. Usually, the tuning of most controllers was based on the techniques of
identification, which are depending on the external weather conditions. For this reason, we are the recourse to the
adaptive controller that can identify the process online. The fundamental difficulty with PID controller is a feedback
system with constant parameters, and no direct knowledge of the process, and thus overall performance is reactive and
a compromise. PID controllers, when used alone, can give poor performance when the PID loop gains must be reduced so that the output trajectory oscillates around the set-point value with no overshoot. They also have difficulties in the
presence of non-linearity, do not react to changing process behavior and have lag in responding to large disturbances.
To overcome these difficulties, we used the PI-intelligent controller. It was easy to implement and was very effective in
tracking the setpoint. The derivative of perturbed error was estimated online for each sampling time. The PI- intelligent
controller ensure good performances without having to tune again and again the PID parameters and guarantees a
suitable adaptation when the plant is changing with time. |
ACKNOWLEDGMENTS |
This work has been supported by a PHC Hubert Curien Volubilis grant (Ref. MA/09/211). |
References |
- F. RodrÃÆÃÂguez, M. Berenguel and M.R. Arahal âÃâ¬ÃÅFeedforward controllers for greenhouse climate control based on physical models,âÃâ¬Ã European Control Conference.Porto, 2001.
- N. Bennis, J. Duplaix, G. En̮̩a, M. Haloua and H. Youlal, âÃâ¬ÃÅGreenhouse climate modelling and robust control,âÃâ¬Ã Computers and Electronics in Agriculture, vol. 61, pp. 96-107, 2008.
- I. Ioslovich, P. Gutman and R. Linker âÃâ¬ÃÅHamilton-Jacobi Bellman formalism for optimal climate control of greenhouse crop,âÃâ¬Ã Automatica, vol. 45(5), pp. 1227-1231, May 2009.
- M. Berenguel, L. Yebra and F. Rodriguez âÃâ¬ÃÅAdaptive control strategies for greenhouse temperature control,âÃâ¬Ã European Conference Control. Cambridge, 2014.
- S.L. Speetjens, J.D. Stigter and G. van Straten âÃâ¬ÃÅTowards an adaptive model for greenhouse control,âÃâ¬Ã Computers and Electronics in Agriculture, vol. 67, pp. 1-8, JuneâÃâ¬ÃâJuly 2009.
- M. Fliess and C. Join âÃâ¬ÃÅModel-free control,âÃâ¬Ã International Journal of Control, vol. 86 (12), pp. 2228-2252, 2013.
- C. Join, F. Chaxel and M. Fliess âÃâ¬ÃÅIntelligent controllers on cheap and small programmable devices,âÃâ¬Ã 2nd Int. Conf. Control Fault-Tolerant Syst., Nice, 2013.
- F. Lafont, N. Pessel, J.F. Balmat and M. Fliess âÃâ¬ÃÅOn the Model-free Control of an Experimental Greenhouse,âÃâ¬Ã World Congress on Engineering and Computer Science, International Association of Engineers, San Francisco, USA, vol. 2, pp. 960-965, October 2013
- F. Lafont, J. F. Balmat, N. Pessel and M. Fliess âÃâ¬ÃÅModel-free control and fault accommodation for an experimental greenhouse,âÃâ¬Ã International Conference on Green Energy and Environmental Engineering, 2014.
- S. Choi, B. dâÃâ¬Ãâ¢Andr̮̩a-Novel, M. Fliess and H. Mounier âÃâ¬ÃÅModelfree control of automotive engine and brake for stopand-go scenario,âÃâ¬Ã Proc. Of 10th European Control Conference (ECCâÃâ¬Ãâ¢09), Budapest, 2009.
- B. dâÃâ¬Ãâ¢Andr̮̩a-Novel, M. Fliess, C. Join, H. Mounier and B.Steux âÃâ¬ÃÅA mathematical explanation via intelligent PID controllers of the strange ubiquity of PIDs,âÃâ¬Ã Proc. of 18th Mediterranean Conference on Control and Automation, Marrakech, Morocco, 2010.
- L. Ezzine, M. guerbaoui, Y. El afou, A. Eddahhak, A. Lachhab, L. belkoura and B. Bouchikhi âÃâ¬ÃÅImplementation of identification algorithm using recurrent RBF neural networks for the inside temperature in a greenhouse,âÃâ¬Ã 4th International Conference on Integrated Modeling and Analysis in Applied Control and Automation, pp. 135-142, Fes, Morocco 13-15 October 2010.
- Y. El Afou, M. Guerbaoui, A. Ed-dahhak, A. Lachhab, L. Belkoura, and B. Bouchikhi.Modelling and control of inside temperature in greenhouse by pid. Association for the Advancement of Modelling and Simulation Techniques in Enterprises : AMSE, N 12026 (2B), accepted in press 29 Novembre 2013. 118
- Y. El Afou, M. Guerbaoui, M. Outanoute, A. Ed-dahhak, A. Lachhab, L. Belkoura, and B. Bouchikhi. Design and implementation of LQG strategies for temperature control under greenhouse. International Journal of Electrical and Electronics Engineering Studies 1, issue 2, accepted in press 2013. 123
- M. Guerbaoui, A. Ed-dahhak, Y. El Afou, A. Lachhab, L. Belkoura and B. Bouchikhi âÃâ¬ÃÅImplementation of direct fuzzy controller in greenhouse based on labview,âÃâ¬Ã International Journal of Electrical and Electronics Engineering Studies, vol. 1(1), pp. 1âÃâ¬Ãâ13, 2013.
- S. F. Yang and D. S. Simbeye âÃâ¬ÃÅComputerized greenhouse environmental monitoring and control system based on LabWindows/CVI,âÃâ¬Ã Journal of Computers, vol. 8, no. 2, pp. 399-408, 2013.
- P. Eredics, âÃâ¬ÃÅMeasurement for intelligent control in greenhouses,âÃâ¬Ã 7th International Conference on Measurement, pp. 178-181, 2009.
- G. Van Straten, G. Van Willigenburg, Van E. Henten and R. Van Ooteghem, âÃâ¬ÃÅOptimal control of greenhouse cultivation,âÃâ¬Ã Taylor and Francis Group, CRC Press, 2011.
- I. Iya, P. O. Gutman and R. Linker, âÃâ¬ÃÅHamilton Jacobi Bellman formalism for optimal climate control of greenhouse crop,âÃâ¬Ã Automatica, vol. 45, pp. 1227-1231, 2009.
- B. Bouchikhi, A. Ed-Dahhak, M. El Harzli and N. El Bari, âÃâ¬ÃÅLes capteurs et leurr̮̫ledans la mesure des param̮̬tresclimatiques pour une gestionrationnelle de lâÃâ¬Ãâ¢eau en agriculture,âÃâ¬Ã Journ̮̩esInternationales des Sciences et Technologies JICTâÃâ¬ÃË07, Cadiz-Tanger, December 2004.
- A. Ed-Dahhak, A. Lachhab, L. Ezzine and B. Bouchikhi, âÃâ¬ÃÅPerformance evaluation of developing greenhouse climate control with a computer system,âÃâ¬Ã AMSE Journal Modeling C, vol. 68, no. 1, pp. 53-64, 2007.
- A. Lachhab, A. Ed-Dahhak, S. Didi, L. Ezzine, J.R. Salinas, F. GarcÃÆÃÂa-Lagos, M. Atencia, G. Joya and B. Bouchikhi âÃâ¬ÃÅMise au point dâÃâ¬Ãâ¢un syst̮̬me de contr̮̫le et de supervision du climat et de la fertirrigationgoutte-ÃÆÃ -goutte sous serre,âÃâ¬Ã Journ̮̩esInternationales des Sciences et Technologies JICTâÃâ¬Ãâ¢07, 2007.
- A. Rahali, M. Guerbaoui, A. Ed-Dahhak, Y. El Afou, A. Tannouche, A. Lachhab and B. Bouchikhi, âÃâ¬ÃÅDevelopment of a data acquisition and greenhouse control system based on GSM,âÃâ¬Ã International Journal of Engineering, Science and Technology, vol. 3, no. 8, pp. 297-306, 2011.
- M. Guerbaoui, Y. El Afou, A. Ed-Dahhak, L. Ezzine, A. Lachhab, L. Belkoura, and B. Bouchikhi âÃâ¬ÃÅEtude et dimensionnementdâÃâ¬Ãâ¢une installationdâÃâ¬Ãâ¢ÃÆÃ©lectrificationhybrideutilisant des photopilessolaires et groupe̮̩lectrog̮̬ne pour lâÃâ¬Ãâ¢alimentation dâÃâ¬Ãâ¢un prototype de contr̮̫le et desupervision des param̮̬tresclimatiques sous serre,âÃâ¬Ã Congr̮̬s International sur les Energies Renouvelables et lâÃâ¬Ãâ¢EfficacitÃÆÃÂ©ÃÆÃâ°nerg̮̩tique CIEREE, FST F̮̬s, Maroc, 20-21 Avril 2011.
- B. Hensel, V. Vasyutynsky, J. Ploennigs and K. Kabitzsch âÃâ¬ÃÅAn adaptive PI controller for room temperature control with level-crossing sampling,âÃâ¬Ã International Conference on Control Cardiff (ICCC), Cardiff, UK, pp. 197-204, 3-5 September 2012.
- M. Beschi, A. Visioli, S. Dormido and J. SÃÆÃ nchez âÃâ¬ÃÅOn the presence of equilibrium points in PI control systems with send-on-delta sampling,âÃâ¬Ã Proceedings of the 50th IEEE Conference on Decision and Control and European Control Conference, Orlando, FL, USA, pp. 7843-7848, 12- 15 December 2011.
- M. Beschi, S. Dormido, J. SÃÆÃ nchez and A. Visioli âÃâ¬ÃÅOn the stability of an event-based PI controller for FOPDT processes,âÃâ¬Ã Proceedings of the IFAC Conference on Advances in PID Control, Brescia, Italy, pp. 436-441, 28-30 March 2012.
- P. G̮̩douin, E. Delaleau, J. Bourgeot, C. Join, S. Arbab-Chirani, and S. Calloch, âÃâ¬ÃÅExperimental comparison of classical PID and model-free control: position control of a shape memory alloy active spring,âÃâ¬Ã Control Engineering Practice, vol. 19, pp. 433âÃâ¬Ãâ441, 2011.
- M. Fliess and C. Join, âÃâ¬ÃÅCommande sans mod̮̬le et commande ÃÆÃ mod̮̬lerestreint,âÃâ¬Ã e-STA, vol. 5, pp. 1-23, 2008.
- M. Fliess, and C. Join, âÃâ¬ÃÅModel free control and intelligent PID controllers: towards a possible trivialization of nonlinear control,âÃâ¬Ã 15th IFAC Symp. System Identif., Saint-Malo, 2009.
- M. Fliess, C. Join, and S. Riachy, âÃâ¬ÃÅNothing is as practical as a good theory: Model-free control- rien de plus utile quâÃâ¬Ãâ¢une bonne tḫ̩orie: la commande sans mod̮̬le,âÃâ¬Ã 4̮̬mes Journ̮̩esDoctorales/ Journ̮̩esNationales MACS, JD-JN-MACS, Marseille, France, 2011.
- H. Abouaissa, M. Fliess, V. Iordanova and C. Join, âÃâ¬ÃÅFirst steps towards a model-free control of a free way traffic flow- prol̮̩gom̮̬nes âÃâ¬Ãâ une r̮̩gulation sans mod̮̬le du traficautoroutier,âÃâ¬Ã Conf̮̩renceM̮̩diterran̮̩ennesurlâÃâ¬Ãâ¢Ing̮̩nierie Sure des Syst̮̬mes Complexes, MISC, Agadir, Maroc, 2011.
- M. Mboup, C. Join, and M. Fliess, âÃâ¬ÃÅNumerical differentiation with annihilators in noisy environment,âÃâ¬Ã Numerical Algorithms, pp. 439-467, 2009.
- D. Y. Liu, O. Gibaru, and W. Perruquetti, âÃâ¬ÃÅError analysis of Jacobi derivative estimators for noisy signals,âÃâ¬Ã Numerical Algorithms, 2011.
- Y. El Afou, M. Guerbaoui, A. Ed-dahak, A. Lachhab, L. Belkoura, B. Bouchikhi âÃâ¬ÃÅModelling and control of inside temperature in greenhouse by PID,âÃâ¬Ã Journal de lâÃâ¬Ãâ¢Association for the Advancement of Modelling and Simulation Techniques in Enterprises (AMSE), Accepted in press: 28 November 2013.
- D. Dindeleux âÃâ¬ÃÅTechnique de la r̮̩gulationindustrielle,âÃâ¬Ã Eyrolles, 1981.
- L. Ezzine, A. Lachhab, A. Ed-Dahhak and B. Bouchikhi, âÃâ¬ÃÅIdentification of a model of regression of the climatic parameters under greenhouse,âÃâ¬Ã Physical & Chemical News, Phys. Chem. News, vol. 39, pp. 43-51, 2008.
|