This paper presents a control strategy for the operation of a Self Excited Induction Generator (SEIG) based stand-alone variable speed wind turbine. To extract maximum energy form the generator and to regulate the terminal voltage of the generator a control strategy is present. In this system there is no grid connection, only stand-alone system is present. The topology of the system consists of a three phase squirrel-cage induction machine connected to a wind turbine through a step-up gear box, Pulse Width Modulation (PWM) Current Controlled Voltage Source Inverter (CC-VSI), Electronic Load Controller (ELC), three fuzzy logic PI controllers and one Hysteresis Current Controller (HCC). A dump-load resistance with IGBT chopper control and the dc link voltage is present to consume the maximum output power from the generator. Dynamic and steady-state performance where simulated using Matlab/Simulink software
Index Terms |
Self-Excited Induction Generator
(SEIG), maximum power extraction, stand-alone
variable speed wind turbine, voltage control. |
INTRODUCTION |
The conventional energy sources such as thermal power
generation, nuclear power generation etc., are limited and
pollute the nature. So more attention and interest have
been paid to the utilization of renewable energy source
such as Wind Energy, Fuel Cell, Solar Energy etc., Wind
Energy is the fastest growing and most promising
renewable energy source among them as it is economically
viable. |
Electrical generators are used to produce electricity,
which are driven by the wind turbines by using the wind
power. Blades are rotated when the wind passes over it,
the blades are connected to the shaft so that the speed can
be increased with the help of gear box the rotational speed is increased. The wind energy is converted into electrical
energy. The output power form the generator is given to a
transformer, which step up the electrical voltage from
700V to 33 kV. The energy produced from the Wind is not
a constant source. It varies continuously and gives energy
in sudden bursts. About 50% of the entire energy is given
out in just 15% of the operating time. Wind strengths
continuous vary and thus cannot guarantee continuous
power. |
The wind turbine output power can be calculated by the
given formula: |
Pw = 0.5ρπ R2V3Cp(λ,β) (1) |
Pw = extracted power from the wind, |
ρ = air density, (1.225 kg/m3 at 20° C at sea level) |
R = blade radius (in m), (it varies between 40-60 m) |
V = wind velocity (m/s) (velocity can be controlled
between 3 to 30 m/s) |
Cp = the power coefficient |
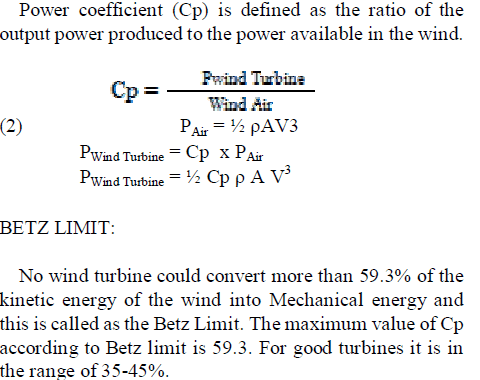 |
PROPOSED SYSTEM |
The power circuit diagram of the proposed system is
shown in the fig 1. Self-Excited Induction Generator
(SEIG) is connected to the variable speed wind turbine
througt a step up gers box. The terminals of the SEIG is
connected in
parallel with the fixed capacitor bank and main load
resistance to the Current Control Voltage source inverter
through a smoothing reactance. The fixed capacitor bank
provides two functions one to avoid pre-charging of DC
side capacitor Cdc of the CC-VSI for the start up process
of the Induction generator and the second function it
acts as |
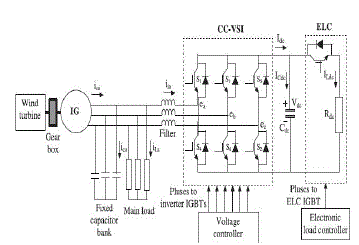 |
Fig 1 Power Circuit Diagram |
a second order filter to reduce the higher order harmonics.
The Electronics Load Controller(ELC) is Connected in
parallel with the CC-VSI to extract to maximum available
energy from wind turbine. The ELC and dump load
resistance are connected in series. The dump load
resistance may be a battery charger or a heater. |
CONTROL STRATEGY |
The active power and reactive power of the Wind
Turbine Induction generator (WTIG) is used to control
and extract maximum available energy from the wind
turbine and to maintain the generated terminal voltage
against wind speed and main load variations using control
strategy. |
Control strategy consists of two controllers |
i. The Voltage controller |
ii. The Electronics Load Controller |
i. THE VOLTAGE CONTROLLER |
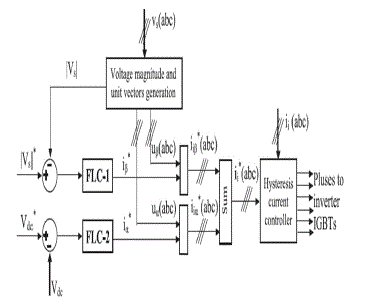 |
Fig 2 The Voltage controller |
The voltage generated from the SEIG can by adjusting its
reactive power (excitation).The output current of the
CC-VSI is used to control or regulate the terminal voltage
of the SEIG. Fig 2 shows the diagram of a voltage
controller. There are two control loops. The Hysteresis
Current Controller (HCC) provides the required switching
pulses to the inverter which is generated from the two
loops, the outer gives the reference current ii*(abc) and the
inner loop gives the actual inverter current ii(abc). The
reference current ii*(abc) are formed by adding two
current component of each phase. |
1. The in-phase active current component iiα* (abc) |
2. The quadrature reactive current component iiβ* (abc) |
The in-phase active current component iiα*(abc) is also
known as real power is used to keep the DC side capacitor
charged to the specified level and excess real power is
given to the dump load resistance as a wastage. The
quadrature reactive current component iiβ*(abc) is also
known as reactive power is used to regulate the generated
voltage. The AC voltage magnitude of the SEIG is sensed
and compared against the AC reference voltage
magnitude. The AC voltage error output is given to the
first fuzzy logic controller (FLC-1). The output of the
FLC-1 is iβ* of the AC voltage control loop is multiplied
by the quadrature unit vectors uβ (abc) which lead the unit
vectors of AC voltages by a phase shift of 90° to give
the reference reactive current components iiβ* (abc) that
control the amplitude of the reactive power generated in
the CC-VSI and the reference reactive current components lead by a phase shift of 90° the corresponding AC voltages
for a positive sign of the AC voltage error. The negative
sign of the AC voltage error, they lag by a phase shift of
90°. Thus, the CC-VSI operates in capacitive and
inductive modes respectively for positive and negative
sign of the AC voltage error. Similarly, the in-phase
components iiα*(abc) are obtained through the DC voltage
control loop. The DC voltage error is given the second
fuzzy PI controller (FLC-2).The output of FLC-2 iα* is
multiplied by the unit vectors uα(abc) (which in-phase
with the corresponding AC voltages) to give the reference
active current components iiα*(abc). |
ELECTRONIC LOAD CONTROLLER (ELC) |
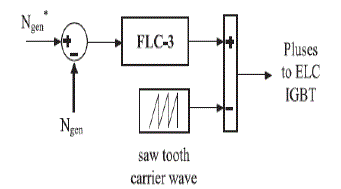 |
Fig 3 ELECTRONIC LOAD CONTROLLER (ELC) |
The generator speed is controlled, by controlling the
electrical load on the induction generator. An active power
controller is used as an ELC. ELC circuit is shown in the
fig 3 in which the generator speed and generator feedback
speed is compared and the speed error is given and
processed in the third fuzzy logic PI controller FLC-3. The
output of FLC-3 and saw tooth carrier wave is compared to
get the required PWM pulses for the IGBT of the ELC. |
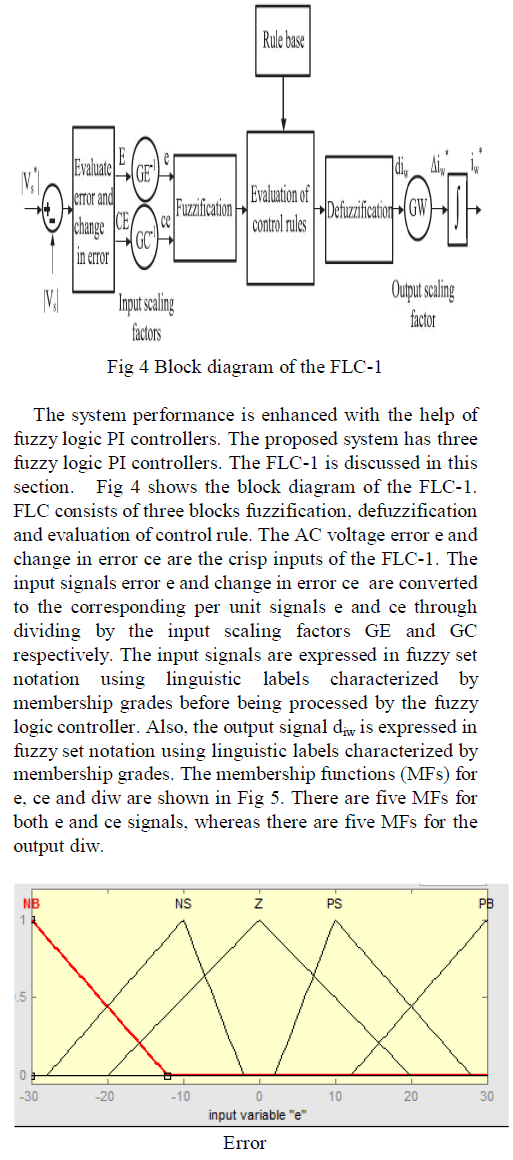 |
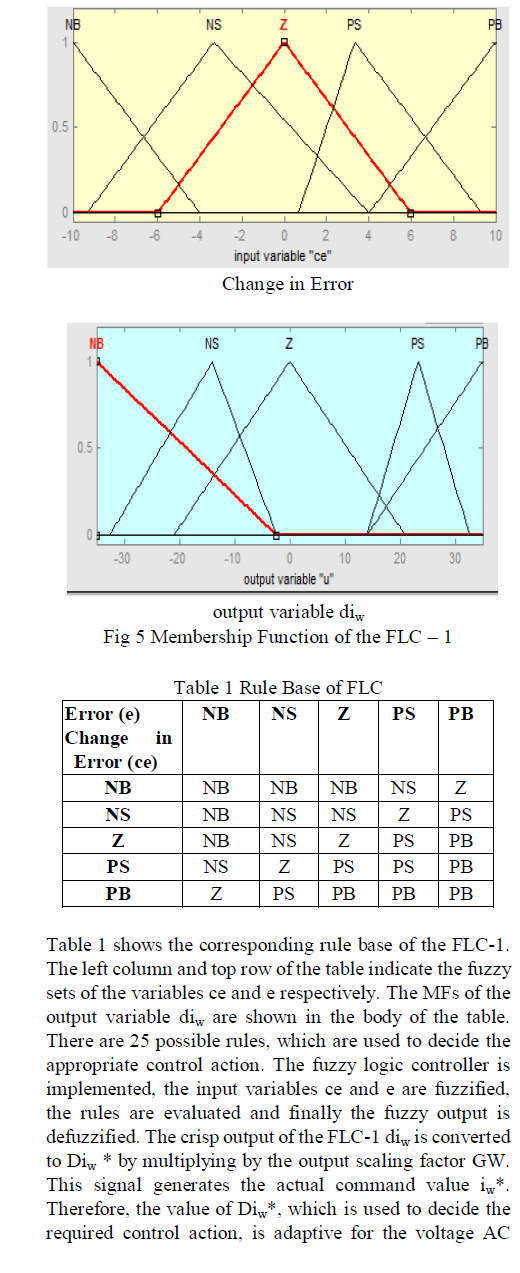 |
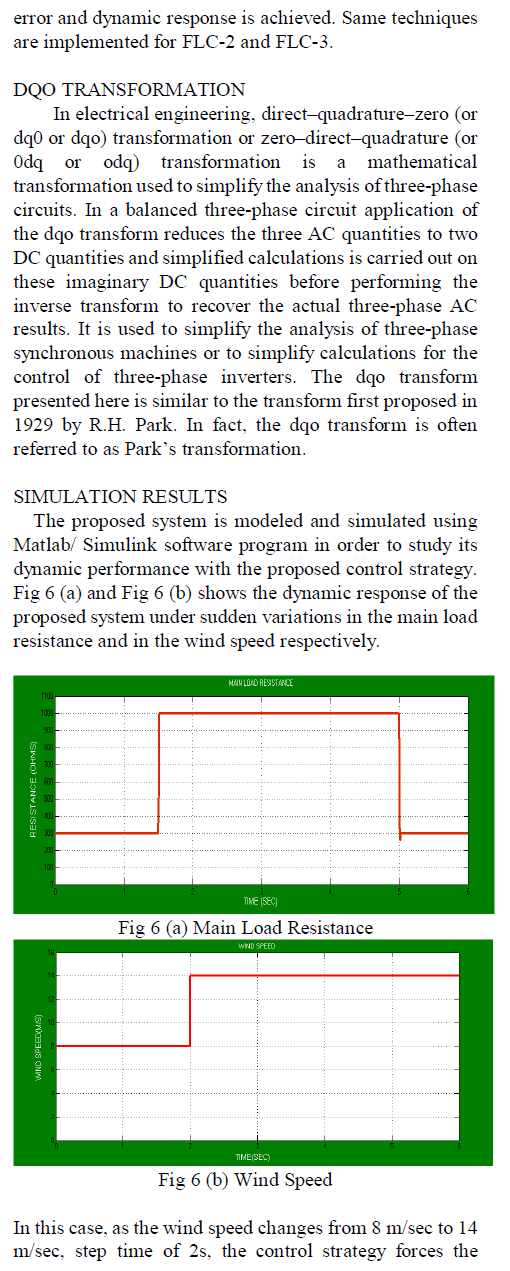 |
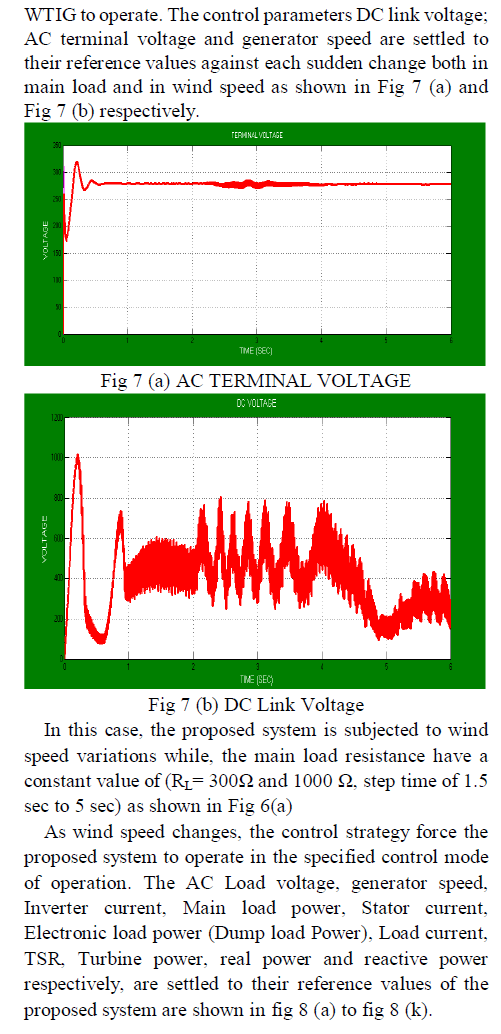 |
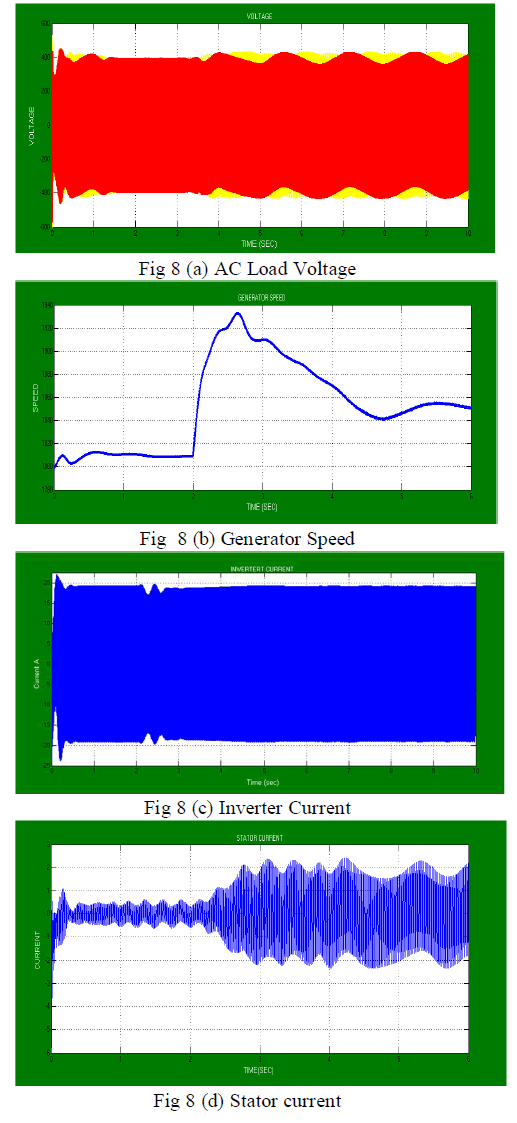 |
 |
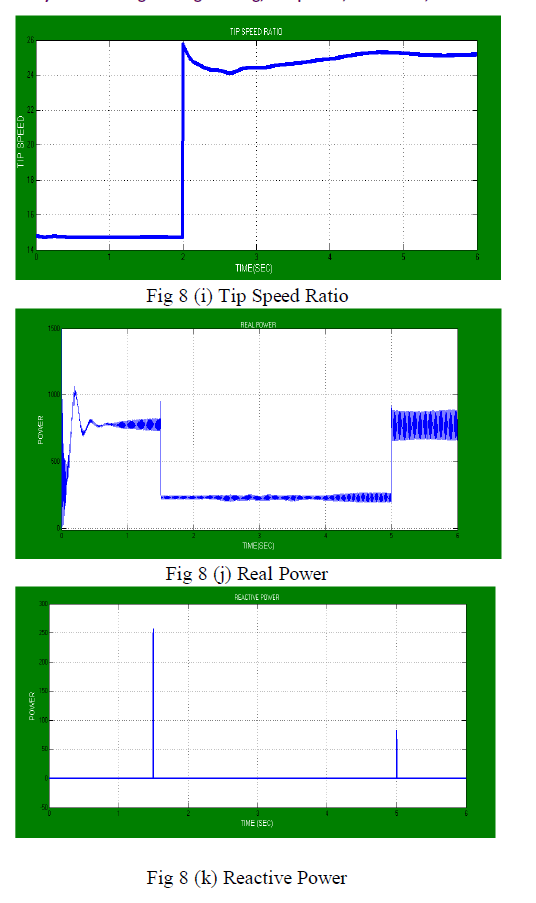 |
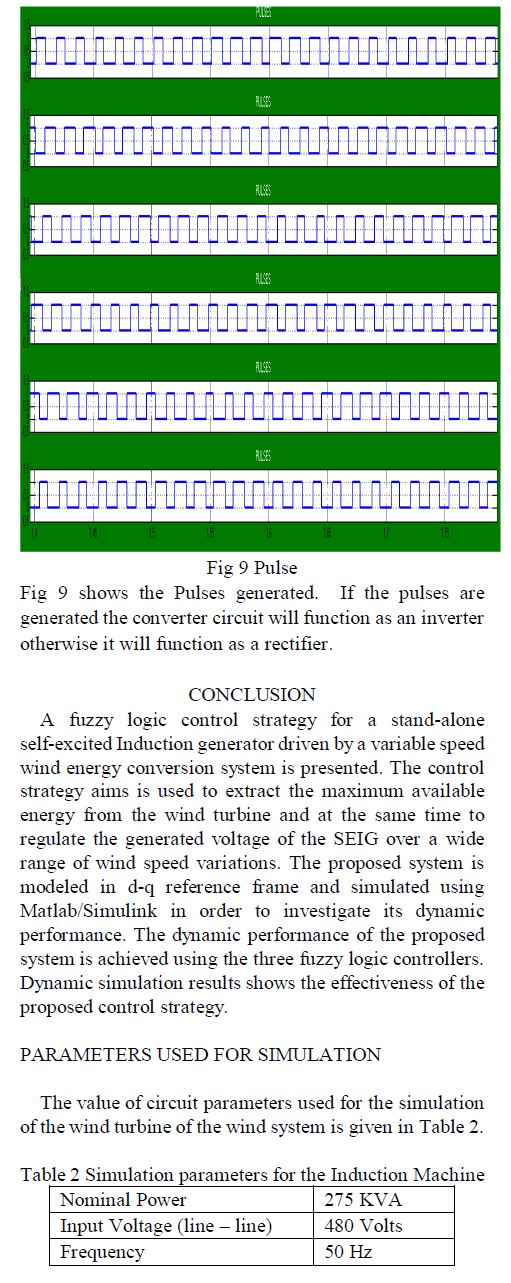 |
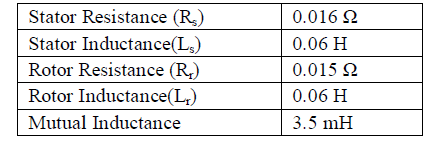 |
References |
- Ackermann T, Soder L., 2002 “An overview of windenergy-status 2002”. Renewable and Sustainable EnergyReviews, No. 6, pp.67 – 127.
- Herbert GMJ, Iniyan S, Sreevalsan E, Rajapandian S., 2007,“A review of wind energy technologies”. Renewable andSustainable Energy Reviews, No.11, pp. 1117– 45.
- Bull SR. Renewable energy today and tomorrow.Proceedings of the IEEE August 2001;89(8): 1216 –26.
- Warne DF, Calnan PG. Generation of electricity from thewind. IEE Proceedings Nov. 1977; 124(11R):963 – 85.
- Chaturvedi R, Murthy SS., Apr. 1989, “Use of conventionalinduction motor as a wind driven self excited inductiongenerator for autonomous operation”. IEEE Transactions onEnergy Conversion, pp. 2051 – 5.
- Murthy SS, Singh BP, Nagamani C, Satyanarayana KVV.,Dec. 1988, “Studies on the use of conventional inductionmotor as self excited induction generators”. IEEETransactions on Energy Conversion, Vol. 3, No. 4, pp.842 –8.
- Hillowala RM, Sharaf AM., Jan/Feb 1996, “A rule-basedfuzzy logic controller for a PWM inverter in a stand-alonewind energy conversion system”. IEEE Transactions onIndustry Applications, No. 1, pp. 57 – 65.
- Rajambal K, Chellamuthu C., Apr. 2005, “Intelligentcontrollers for an isolated wind energy conversion scheme”.Proceedings of IEEE-PEDS Conference, pp.938 – 43.
- Koutroulis E, Kalaitzakis K., Apr. 2006, “Design of amaximum power tracking system for windenergy-conversion applications”. IEEE Transactions onIndustrial Electronics , Vol.53, No. 2, pp.486 – 94.
- Kanellos FD, Hatziargyriou ND., Dec. 2010, “Optimalcontrol of variable speed wind turbines in islanded mode ofoperation”. IEEE Transactions On Energy Conversion, Vol.25, No. 4.
- Simoes MG, Bose K., Jan 1997, “Fuzzy logic basedintelligent control of a variable speed cage machine windgeneration system”. IEEE Transactions on PowerElectronics, Vol. 12, No. 1, pp.87 – 95.
- Poddar G, Joseph A, Unnikrishnan A., Oct. 2003,“Sensorless variable-speed controller for existing fixed-speedwind power generator with unity power-factor operation”.IEEE Transactions on Industrial Electronics Vol. 50, No.5,pp.1007– 15.
- Kim HG, Lee DC, Seok JK, Lee GM., 2003, “Stand-alonewind power generation system using vector-controlledcage-type induction generators”. Proceedings of the ICEMSConference, pp 289 – 92.
- Pena R, Cardenas R, Blasco R, Asher G, Clare J, 2001, “Acage induction generator using back to back PWMconverters for variable speed grid connect wind energysystem”. Proceedings of the IEEE-IECON, pp.1376 – 81.
- O. A. Lara, N. Jenkins, J. Ekanayake, P.Cartwright, M.Hughes, 2009., “Wind energy generation: Modeling andControl”, John Wiley and Sons, UK.
|