A MEMS based spiral shaped piezoelectric transducer has been designed for harvesting energy with human walking motion. The torque obtained by human walk has been subjected to the spiral shaped piezoelectric transducer in order to obtain maximum displacement. A bimorph spiral shaped piezoelectric transducer has been designed to reduce the brittleness of the structure. FEM simulations has been performed with different types of metals and varying dimensions. The bimorph spiral shaped piezoelectric transducer gives maximum displacement of 6.1858x 106 μm for 150 Nm torque with nickel as its shim layer and PZT-5H as its upper and bottom layer.
Keywords |
Spiral shaped piezoelectric transducer, PZT, Bimorph, MEMS. |
INTRODUCTION |
Energy harvesting is a form of renewable power generation and is a key enabling technology for a whole host of future
distributed systems such as wireless sensors, implantable devices and structural health monitoring. Among the
possibilities for energy generators, piezoelectric materials have been generally used because of their ability to convert
ambient mechanical energy into electrical energy. PZT is available in the form of polymer[2] and ceramic, the
disadvantage of using polymer is we cannot obtain a rigid structure so inorder to design spiral shaped PZT we use
ceramic material. For an energy harvesting device the output obtained should be as greater as possible, the output
power[7] obtained is directly proportional to the mass and inversely proportional to the operating frequency of the
device. A harvester needs to be designed for a particular type of energy source with a certain frequency. One difficulty
often encountered is that for a common low frequency, e.g., 50-200 Hz, a beam-type harvester operating with the
lowest flexural mode usually has a frequency that is too high. Of course one can increase the harvester size to lower its
frequency, but usually there is a limit on the device size. The mass of the system is responsible for maximum output
power as well as the device to operate at low frequency and a spiral shaped bimorph piezoelectric transducer has large
mass but in reduced size and shape which gives maximum displacement and it occupies less space than a rectangular
shape piezoelectric transducer of same dimension. |
In this paper we propose a spiral shaped bimorph as a low frequency energy harvester based on the availability of
ceramic spiral transducers. piezoelectric transducer is available in two types, unimorph and bimorph. A bimorph
piezoelectric transducer gives maximum displacement and avoids breakage of structure like spiral shaped. A bimorph
type consists of a shim layer (metal) sandwiched between two PZT layer. Simulation of rectangular and spiral shaped
bimorph piezoelectric transducer has been done using COMSOL software were spiral shape gives maximum
displacement. A spiral bimorph is effectively a long and curved bar or belt and hence has relatively low frequency.
Since the long belt has a spiral shape, the largest dimension of the structure still remains small. A spiral shape can be
designed with multiple number of arms namely 1 arm spiral and 2 arm spiral. The displacement of 2 arm spiral is more
as compared to 1 arm spiral, 2 arm spiral is selected and simulated for different types of shim layer(metal). |
DESIGN OF STRUCTURE IN 3D MODEL USING COMSOL |
A. Rectangular shaped bimorph piezoelectric transducer |
In a rectangular shape, the shim layer (nickel) is sandwiched between two piezoelectric layer (PZT-5H). The structure
is fixed at one end and it is known as fixed constraint as shown in the figure. |
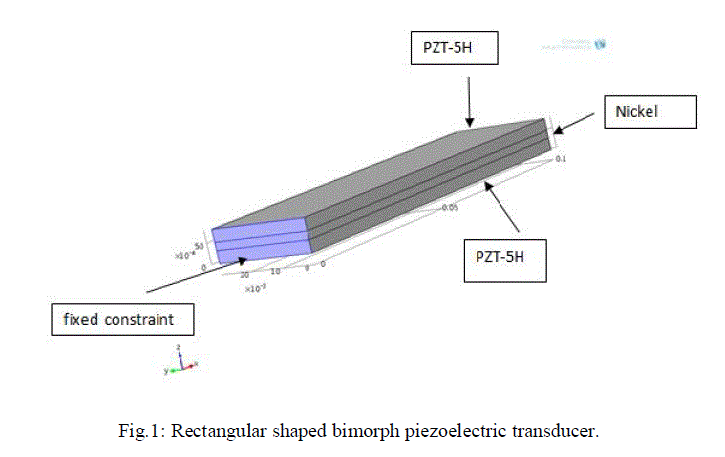 |
In fig 1, the rectangular shaped bimorph piezoelectric transducer is shown were the shaded region with blue colour
represents fixed constraint and the upper and bottom layer material used here is PZT-5H and the shim layer material
used is nickel. |
arm spiral shaped bimorph piezoelectric transducer |
A long belt is curved in the form of spiral in order to obtain maximum displacement with low operating frequency. |
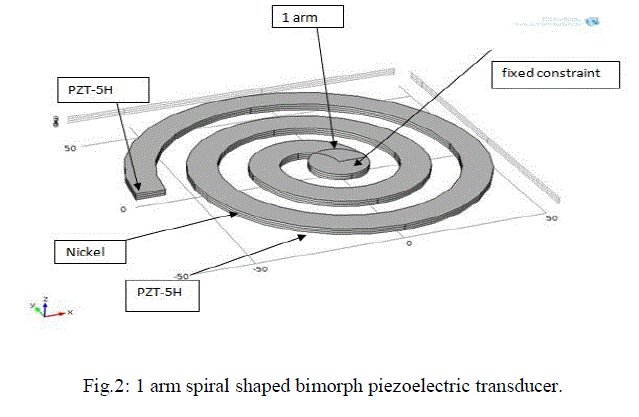 |
In fig 2, the 1 arm spiral shaped bimorph piezoelectric transducer is shown were the small circle in the middle is fixed.
The material used in bottom and top layer is PZT-5H and nickel as shim layer. |
C. 2 arm spiral shaped bimorph piezoelectric transducer |
Two long belt is curved in the form of spiral in order to obtain maximum displacement with low operating frequency. |
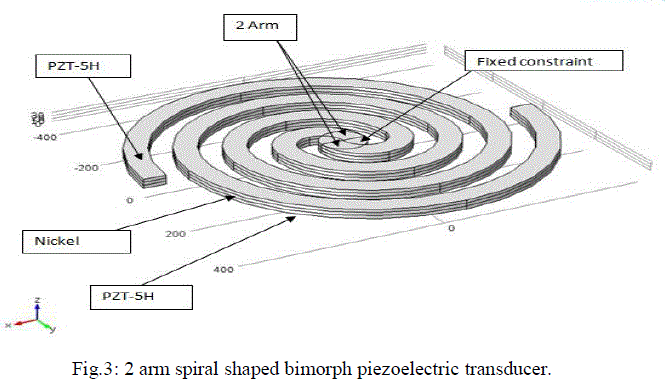 |
In fig 3, the 2 arm spiral shaped bimorph piezoelectric transducer is shown were the circle in the middle is fixed. The
material used in the upper and bottom layer of the spiral is PZT-5H and for shim layer the material used is nickel. |
SELECTION OF MATERIAL |
A. Lead Zirconate Titanate |
Twenty of the thirty-two crystallographic elements exhibit piezoelectric properties. Only few materials are useful for
piezoelectric transducers. Primarily quartz, Rochelle salt, ammonium dihydrogen phosphate (ADP) and ceramics made
with barium titanate, dipotassium tartrate, potasssium dihydrogen phosphate and lithium sulfate are some of the
materials used in real applications. Lead Zirconate Titanate is a ceramic and it has been choosed for designing spiral
shape because stiffness is essential for obtaining spiral shape. There are various types of PZT available out of which we
select PZT-5H because youngs modulus is less for this PZT compared to the other types of PZT available like PZT-4,
PZT-5A and PZT-8. Youngs modulus is a very important property when it comes for deflection of a material, it
determines the rigity of a material and it is different for different materials. A material can give us maximum
displacement if the youngs modulus is less and maximum displacement results in greater energy generation hence PZT-
5H is selected. Poisson ratio for all these material is 0.31. |
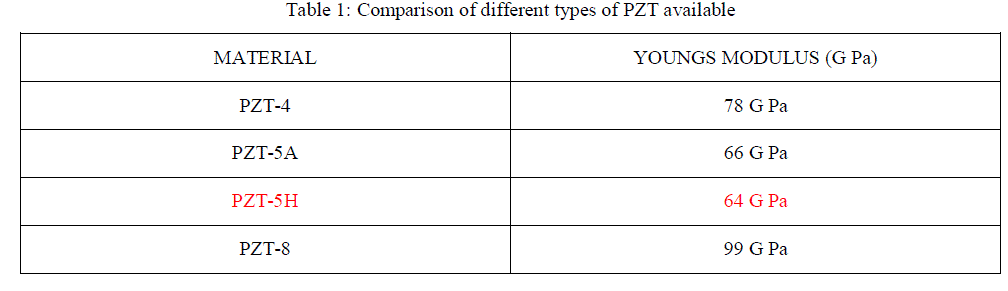 |
B. Nickel (shim layer) |
The selection of nickel has been taken place after the simulation of the design. The below mentioned materials were
used as shim layer placed in between PZT-5H for simulating the spiral shaped piezoelectric transducer. The maximum
displacement is obtained with tungsten(W) but the availability of this material is rare in the world so it is avoided next
is platinum but 1gm=Rs 3693, it is costly, gold 1gm=Rs 2749 costly, palladium is a rare material. The material which
gives highest displacement after the above mentioned material is nickel, displacement=6.1858*106 μm. Nickel is
readily available and its cost is very less 100gm=Rs 463.309. |
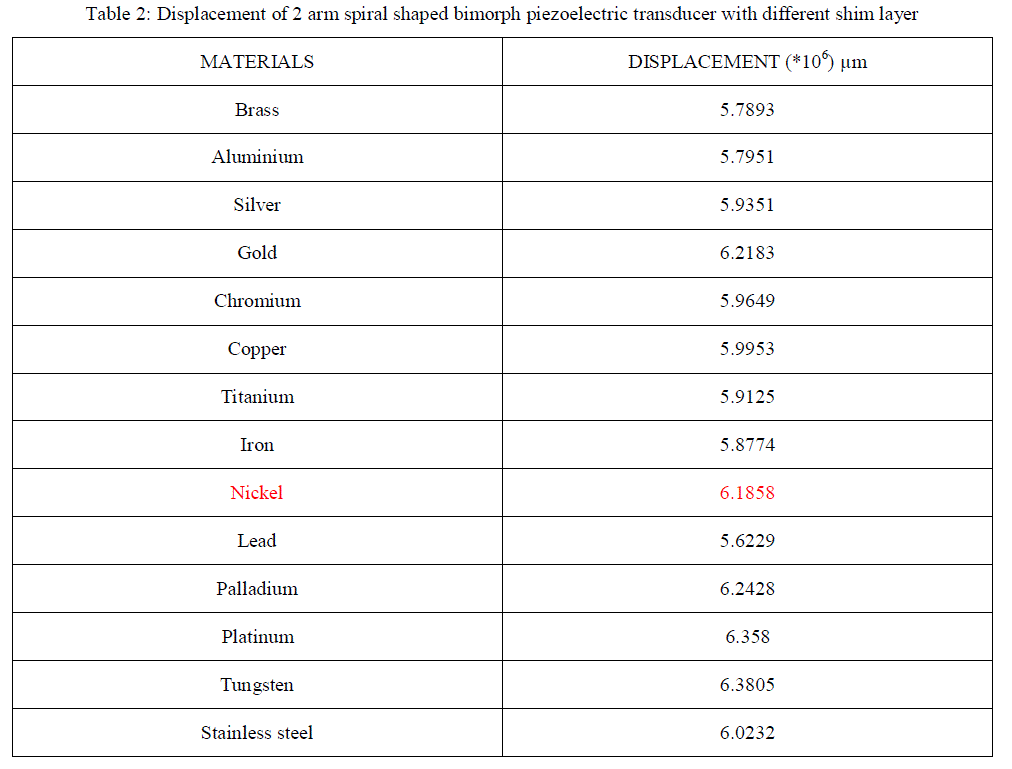 |
APPLICATION OF FORCE |
The moment of force exerted by the human ankle is a very important factor. Depending upon the moment of force
exerted by the human ankle is responsible for the displacement of the spiral shaped piezoelectric transducer. According
to Susannah K.S. Thorpe, 1997 the torque exerted by the human leg is calculated with the help of the following
formula: |
 |
where, |
Ma = muscle stress at ankle |
r = joint angle |
σ = muscle stress |
TS = triceps surae |
A = physiological cross-sectional area |
with the above formula it has been found that a 30±5.9 year old person with height 1.8±0.07m and mass of 77.5±5.6
can exert 150 Nm. |
SIMULATIONS |
Simulation parameters: |
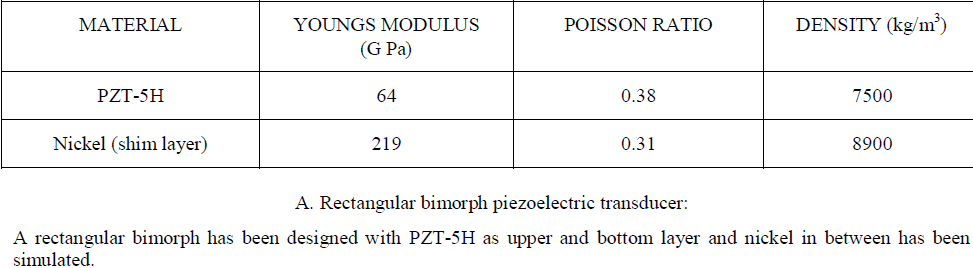 |
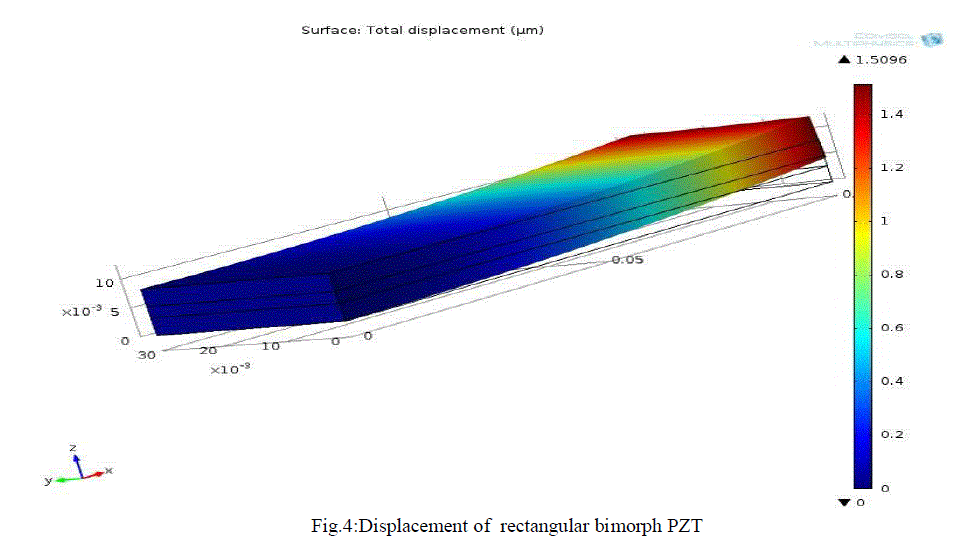 |
In fig 4, the simulation of rectangular shaped bimorph piezoelectric transducer has been performed were we obtain a
displacement of 1.5096 μm for a applied torque of 150 Nm. |
B. 1 arm spiral shaped bimorph piezoelectric transducer |
A 1 arm spiral shaped PZT designed with nickel sandwiched between PZT-5H has been simulated. |
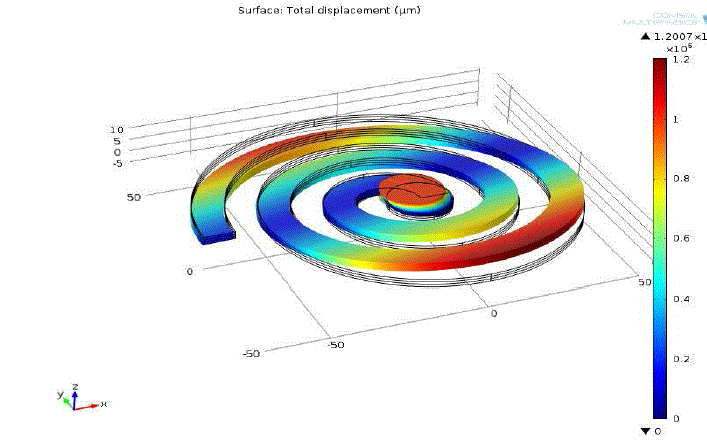 |
Fig.5: 1 arm spiral shaped PZT |
In fig 5, a 1 arm spiral shaped piezoelectric transducer is subjected to a torque of 150 Nm for which a displacement of
1.2007x106 μm is obtained. |
C. 2 arm spiral shaped piezoelectric transducer |
A 2 arm spiral shaped PZT designed with nickel sandwiched between PZT-5H has been simulated. |
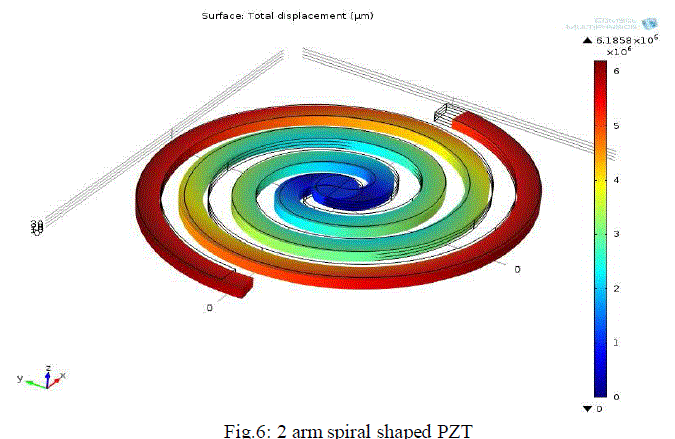 |
In fig 6, a 2 arm spiral shaped piezoelectric transducer is subjected to a torque of 150 Nm for which a displacement of
6.1858x106 μm is obtained. |
RESULTS AND DISCUSSIONS |
A spiral shaped bimorph piezoelectric transducer for various shapes and dimensions and for various materials has been
simulated and found out that PZT-5H as upper and lower layer and nickel as shim layer has given maximum output
displacement of 6.1828*106 μm for application of force of 210Nm. |
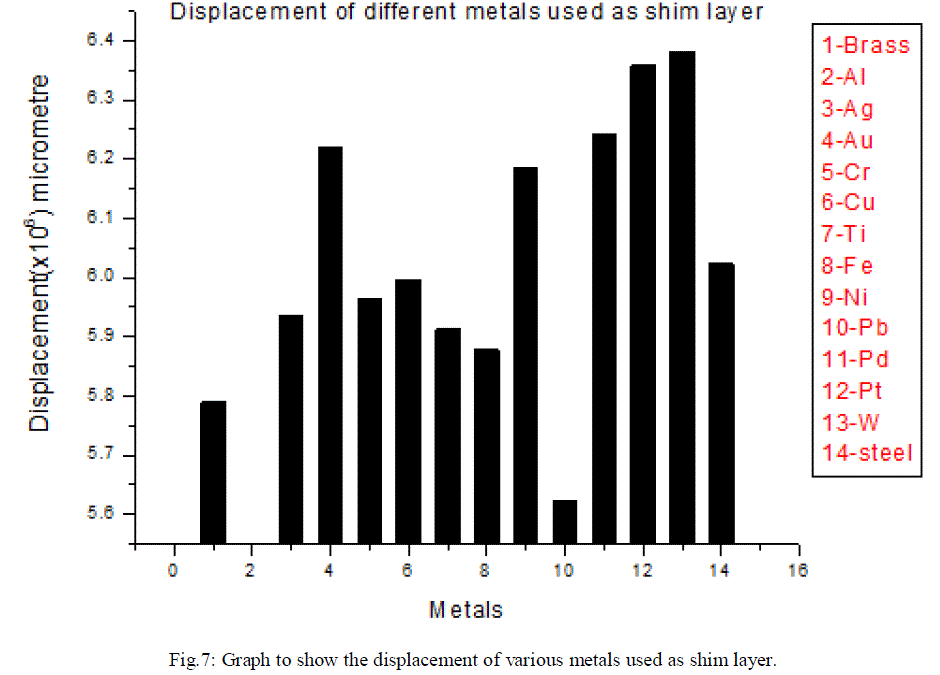 |
In fig 7, the above graph shows the displacement of 2 arm spiral shaped bimorph piezoelectric transducer with different
shim layer(metals). The displacement of tungsten(W), palladium(Pd) is greater than nickel but it comes under the
category of rare metal and so the displacement of gold and platinum is greater but it is costly compared to nickel hence
nickel is chosen to be the best shim layer material than the other metals according to the simulation results. |
CONCLUSION |
The performance of a piezoelectric transducer in rectangular and spiral shape has been simulated with COMSOL 4.3
multiphysics software. Spiral shape has been classified into 1 arm and 2 arm were 2 arm spiral shaped bimorph
piezoelectric transducer gives maximum displacement of 6.1858x106 μm with PZT-5H as upper and bottom layer and
nickel as shim layer. |
References |
- M. M. Deterre, E. Lefeurve, "Micromachined piezoelectric spirals and ultra-compliant packaging for blood pressure energy harvesters powering medical implants," IEEE transactions on MEMS, 249-252, 2013.
- J. G. Rocha, L. M. Gonclaves, "Energy harvesting from piezoelectric materials fully integrated in footwear," IEEE transactions on Industrial Electronics, vol. 57, no. 3, 813-819, march 2010.
- Tao Dong, Einar Halvorsen, "A MEMS based spiral piezoelectric energy harvester," Proceedings of power MEMS+microEMS, November 9- 12, 77-80, 2008.
- Susannah K. S. Thorpe, "Stresses in human leg muscles in running and jumping determined by force plate analysis and from published magnetic resonance images," The Journal of Experimental Biology 201, 63-70, 1998.
- HU Yuantai, "A low frequency piezoelectric power harvester using a spiral shaped bimorph," Science in china series G: Physics, Mechanics & Astronomy, vol. 49 no.6, 649-659, 2006.
- Dr. S. Renganathan, "Transducer engineering," 1999, Allied publishers limited.
- A. K. Shawney, "Electrical and Electronics measurement and instrumentation," 1997, Dhanpat Rai & sons.
- Hai-ren WANG, 2013, âÃâ¬ÃÅ Spiral shaped piezoelectric transducer in torsional motion as low- frequency power harvester,âÃâ¬Ã Applied mathematics and mechanics, edition 34(5), 589-596, 2013.
- HU Yuantai, HU Hongping, âÃâ¬ÃÂA MEMS based spiral piezoelectric energy harvester,âÃâ¬Ã Science in China series G:Physics, Mechanics and Astronomy, vol.49 No.6 649-659.
- Elizabeth K., âÃâ¬Ã Thin Film Piezoelectric Energy Scavenging Systems for Long term medical monitoring,âÃâ¬Ã IEEE computer society, 2006 .
|