Keywords
|
Synchronizer, Synchronism-check relays, Automatic synchronization,Microcontroller. |
|
|
INTRODUCTION
|
Synchronizing a generator to the power system must be done carefully. The frequency and voltage of generator must be closely matched to power system, and the rotor angle must be close to the instantaneous power system for closing the generator breaker to connect the isolated generator to the power system. Poor synchronizing can: |
ïÃâ÷ Damage the generator and the prime mover[2]. |
ïÃâ÷ Damage the generator and step-up transformer windings caused by high currents. |
ïÃâ÷ Cause disturbances such as power oscillations and voltage deviations. |
ïÃâ÷ Protective relay elements interpret the condition as an abnormal operating condition and trip the generator. |
Traditionally, generator control systems include a synchronizing panel. The synchronizing panel includes indications of voltage, angle, and slip that show what adjustments the operator needs to make to the governor and exciter and when it is acceptable for the operator to close the breaker. In many cases, the process is automated using an automatic synchronizer with manual control available as a backup. |
In generating facilities with more than a single generator or installations with multiple synchronizing breakers, complicated synchronizing circuits with many contacts are required to switch the VT and control signals between the operator and automatic controls and the high-voltage equipment. Maintaining proper isolation and safety grounding of sensing and control circuits often requires the use of problem-prone auxiliary relays and VTs, which can reduce the reliability of the system. |
Today, protective-relay-grade microprocessor devices can significantly improve manual and automatic synchronizing systems. This paper discusses how this technology can simplify synchronizing circuits to reduce cost, improve reliability, and easily accomplish complete integration, automation, and remote control of the system. |
Before discussing the advancements available from microprocessor-based technology, it is a good idea to review traditional systems and their limitations; it is easier to determine what improvements can be made. |
II-TRADITIONAL AUTOMATIC SYNCHRONIZING SYSTEMS
|
1. An automatic synchronizer is a device that can perform all or part of the functions required to synchronize a generator. It can provide control signals to the generator and exciter to match the frequency and voltage to the system, and it can close the breaker. In its most basic form, an automatic synchronizer measures the slip and calculates the advanced angle at which to energize the close coil to compensate for the breaker close mechanism delay. |
 |
where: ADVANG is the advanced close angle. |
TCLS is the CB close mechanism delay. |
For example, using 0.05 Hz slip and a breaker close delay of 5 cycles, the advanced angle would be 1.5 degrees. At the angle calculated using (1), the breaker close coil is energized and the breaker main contacts will close at the exact zero-degree angle difference. The main advantage of an automatic synchronizer over an operator is that the device can more consistently close the breaker at the precise correct moment. |
An automatic synchronizer often includes generator control functions for frequency and voltage matching. Typically, the control interface is a set of four output contacts to raise and lower frequency and voltage. The contacts are pulsed to raise and lower the generator and the exciter control system control reference. Generally, a proportional pulse width characteristic is the best method to quickly bring the generator speed and voltage into the acceptance range. The pulse duration of a proportional control characteristic is greater when the controlled parameter is far from the acceptance band and gets proportionally smaller as it gets closer to the acceptance band [1]. |
It is necessary to tune the control characteristics to the generator system. Too conservative correction characteristics will cause the process to take a long time to come into band. Too aggressive characteristics can increase synchronizing time if the frequency and voltage overshoot the acceptance bands and hunt between raising and lowering. The mechanical system includes inertia, and the field circuit has a dc time constant, making it necessary to allow time between correction pulses to allow the system to respond before determining if additional correction pulses are required. |
Alternatively, the automatic synchronizer can send the slip and voltage difference measurements as an error signal to the plant generation control system. The generator control system then adjusts the generator(s) to minimize the error until the synchronizing acceptance criteria are met. The automatic synchronizer checks the voltage difference and slip for acceptance bands and, when both are in band, calculates the advanced angle compensation and closes the breaker. This arrangement is especially appropriate for synchronizing an islanded system of multiple generators and load to the grid or another island. |
2. Synchronism-check relays are often used to supervise both manual and automatic synchronizing operations. Most synchronism-check relays check that the angle is inside a ± angle window and stays there for a time period. The angle window and time delay are a surrogate for measuring slip. Many years ago, there was an industry push to upgrade synchronism-check relays from induction disk types with inverse timing characteristics to solid-state types with definite- time characteristics for generator synchronizing applications. The time criteria of such a relay would be set using (2). |
25Td sec= |
 |
where: |
25TD is the synchronism-check time-delay setting. |
25ANG is the synchronism-check angle setting. |
ADVANGMAX is the ADVANG at SLIPMAX per (1). |
SLIPMAX is the allowable slip in Hz. |
For such a synchronism-check relay, the time-delay setting must accommodate the advanced angle. So, for the previous example using 0.05 Hz (18 degrees/second) SLIPMAX and an angle setting of 10 degrees, the ADVANGMAX would be 1.5 degrees. The setting 25TD would be less than 0.47 seconds to allow the synchronismcheck relay to close its contacts before 1.5 degrees in advance of 0 degrees at SLIPMAX. If the actual slip is less than SLIPMAX, the synchronism-check relay would have closed its permissive contact well in advance of the close command from the operator or the automatic synchronizer[3]. |
The problem with this type of synchronism-check relay is that it can cause a late close, up to its angle setting past 0 degrees (in this case, 10 degrees). For example, if the synchronism-check delay is set to 0.47 seconds and the operator has misjudged and initiated the close with slip at 0.10 Hz (36 degrees/second), the close coil would be energized at 6.9 degrees past 0 degrees (because the operator’s hand is still on the control switch). The main contacts would make at 9.9 degrees past 0 degrees because the generator would advance 3 degrees during the 5-cycle mechanism delay at 0.10 Hz. For this reason, it is recommended to set the delay to less than the maximum value calculated using (2). |
In the previous late-close scenario, the synchronism-check contact would then drop out at 10 degrees past 0 degrees. The synchronism-check contact would then be in danger of damage when it tries to interrupt the closing circuit current as the contact opens. Often, under these conditions, the contact will weld closed and the synchronism-check function will be inadvertently disabled (permissive contact closed all of the time). |
IV-BLOCKDIAGRAM EXPLANATION
|
A. Methodology
|
In order to put a solution to the problems above, the automatic synchronizing device needs to perform the following operations: |
First, the device monitors the voltage difference between the two generators and regulates the voltage amplitudes to reduce the voltage difference when it is not in the allowed scope. |
Second, the device monitors the slip frequency between the two generators and regulates the frequencies to reduce the slip frequency when the slip frequency is not allowed. |
Third, the device monitors the phase-angle difference between the two generators and regulates the phases to reduce the slip frequency when the slip frequency is not allowed. |
Fourth, when the frequency, voltage, and phase-angle match the parallel requirements, the closing order is issued[4]. The proposed model consists of PIC microcontroller, which is used to control the GT (Generator Transformer) Breaker. The voltage, Frequency of the generator and power system (grid) measured by the sensors are given as the input to the microcontroller and when the voltage and frequency matches between the generator and grid , control signal from the microcontroller is given to the GT Breaker to close the GT breaker. |
B. Proposed system advantages
|
Microprocessor-based synchronism-check elements measure slip directly, so it is not necessary to include a time delay. If the slip and voltage difference are within acceptance criteria, the synchronism-check output asserts as soon as the angle difference comes into the acceptance range. The synchronism-check element will not cause a late close with this type of relay[5]. |
Microprocessor-based synchronism-check elements are capable of calculating the slip-compensated advanced angle and adjusting their characteristics to assert permissive trip at the advanced angle instead of the edge of the angle window. For example, with an angle setting of ±30 degrees, the element asserts if the system angle across the breaker is between –30 degrees and +30 degrees. But, when slip is detected, it will assert its contact at 0 degrees minus the advanced angle. So, for the example previously discussed with an advanced angle of 1.5 degrees at 0.05 Hz slip, the synchronism-check element would assert at –1.5 degrees and de-assert at 28.5 degrees. |
One take away from this discussion is that operators need to understand that a simple synchronism-check relay should not be relied upon to ensure a smooth synchronization. Its main purpose is to prevent a faulty synchronization with a generator significantly out of phase. A microprocessor-based synchronism-check element with a slipcompensated advanced angle function can be used to initiate closing similar to the feature in an automatic synchronizer. |
V-SIMULATION RESULTS
|
VI-CONCLUSION
|
Automatic systems have the advantage of greater precision and repeatability in calculations. Human operators have the advantage of better recognizing abnormal conditions and errors in the synchronizing indications. Systems that require both operator and automatic synchronizer to initiate the breaker close take advantage. |
The manual one depends on a well-trained operator where the automatic depends on a device based on hardware or software technique. Synchronizing device proposed in the thesis is an Automatic device based on embedded system. |
|
Figures at a glance
|
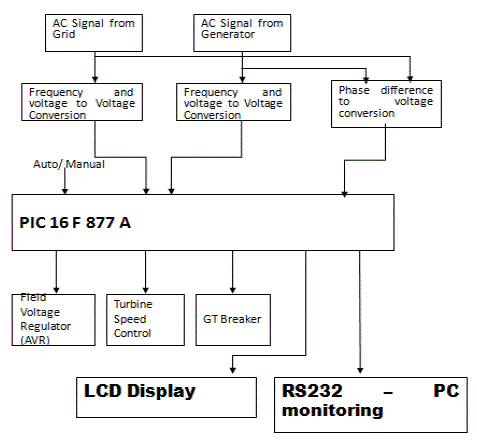 |
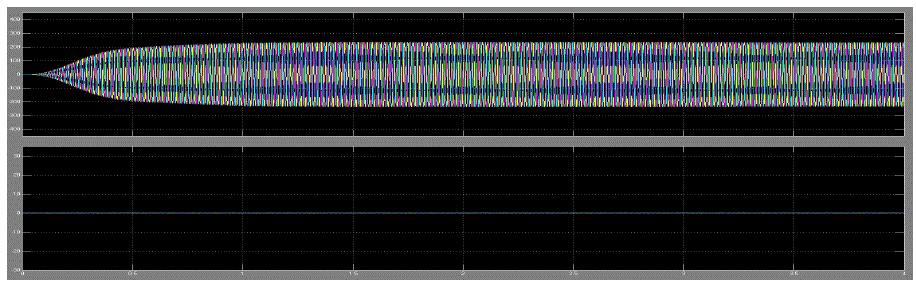 |
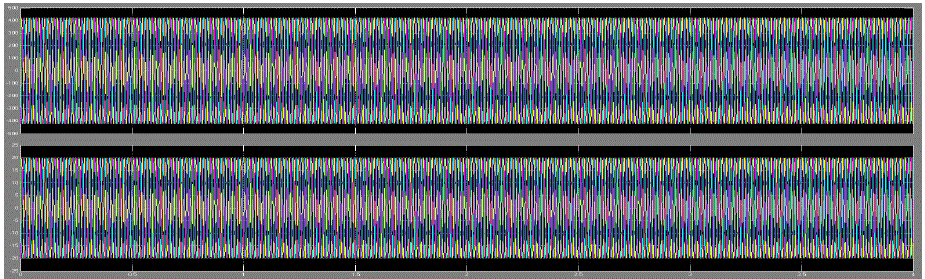 |
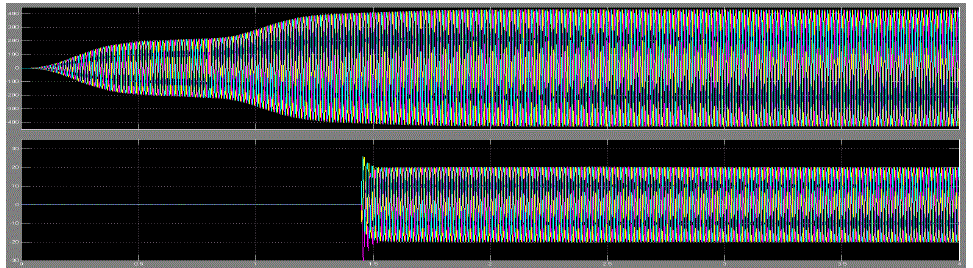 |
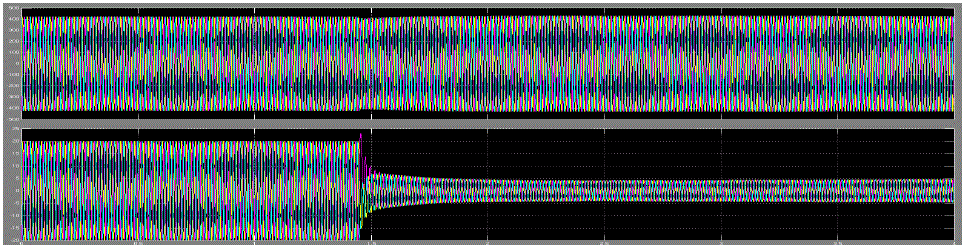 |
Figure 1 |
Figure 2 |
Figure 3 |
Figure 4 |
Figure 5 |
|
|
References
|
- R. A. Evans, “A Manual/Automatic Synchronization Circuit for a 37.5 MVA Steam-Turbine-Driven Generator,” IEEE Transactions onIndustry Applications, Vol. 26, Issue 6, pp. 1081–1085, Nov./Dec. 1990.
- L. C. Gross, L. S. Anderson, and R. C. Young, “Avoid Generator and System Damage Due to a Slow Synchronizing Breaker,” proceedings ofthe 24th Annual Western Protective Relay Conference, Spokane, WA, October 1997.
- R. A. Evans, “A Manual/Automatic Synchronization Circuit for a 37.5 MVA Steam-Turbine-Driven Generator,” IEEE Transactions onIndustry Applications, Vol. 26, Issue 6, pp. 1081–1085, Nov./Dec. 1990.
- IEEE Guide for Operation and Maintenance of Turbine Generators,IEEE Standard 67-2005.
- Z. Ying, D. Cun-Lu, J. Chong-Peng, C. Li “Design of Generator Synchronizing Device Based on PIC16F877 and FPGA”. ISA 2009 “Intelligent Systems andApplications 2009”, Wuhan, 978-1-4244-3893-8, IEEE 2009.
|