Keywords
|
Micricontroller, Proteus , Sensor, Wind Energy, |
INTRODUCTION
|
“Energy can be neither created nor destroyed”. Human resources are increasing nowadays and the need for energy resources is also increasing. The surplus amount of resources has been decreasing. Hence there is an urge to find any alternate resources .Energy can be classified in to renewable and non renewable. The availability of non renewable energy resources reached a particular extent. There is a need to use any alternate form of renewable energy resource. The widely used among the renewable energy resources wind energy. It has its own benefits such as availability, non polluting no green house gases emission, etc. Using wind turbines wind energy can be converted to useful form of electrical energy. For any process to get the perfect results the process should be controlled and monitored at regular interval of times. The parameters to be measured are direction, voltage, current and pressure. Usually the interfacing to computer is done using a data acquisition card. To avoid economic problems and to provide more convenience to the users we are using a microcontroller as data acquisition system. As usual the control and monitoring process is carried out. Proteus 8 software is used to create pcb design foe the microcontroller programming. |
II. RELATED WORK
|
In [1], The authors developed a virtual platform for a Web-based remote application dedicated to condition monitoring and fault detection for ac electrical machines. The platform is based on several tools developed by using the labVIEW software. In [2],the authors developed a condition monitoring system using data acquisition platform. The data acquisition platform fulfills all the industrial requirements In [3], the authors made a study of condition monitoring of wind turbines using labVIEW platform, and a test was performed to measure the performance and output power. In [4], the authors used LABVIEW as a tool to take the virtual equipment instead of real object to control the system and improve the performance..In [5],the author developed an online wind power monitoring system and a PC-based virtual instrument (VI)can carry out an on line maximum wind power tracking using labVIEW and the microprocessor (MCS- 8051). |
III. ARCITECTURE
|
The architecture consists of a microcontroller, pc, sensors. The sensors include pressure sensor, current sensor, and voltage sensor. The parameters to be measured are current, voltage, pressure and direction. The sensors get the information about these parameters. The sensor output is given to the microcontroller which acts as a data acquisition system. Today microcontrollers have built in features to act as a data acquisition (DAQ). The output from microcontroller is converted in to digital form and sent to the pc. The simulation can be made using proteus design suite |
IV. EMDEDDED C VS C
|
Though C and embedded C are different they have some similarities. The constructs are same but the differences lies in their applications. |
• C is used for desktop computers where embedded C is used for microcontrollers. C has the feature to use the surplus resources available in desktop computers hence no need to worry about memory. |
• Embedded C need to use limited resource available on embedded processor. If program code exceeds the limit the system will crash. |
• Compilers for C generate OS dependent executables. |
• Embedded C requires compilers to create files to be downloaded to the microcontroller/microprocessor where it needs to run. |
• Embedded compilers give access to all resources which desktop computer compilers do not. |
• Embedded systems have real time constraints which desktop applications do not have such constraints. |
• Desktop applications have a console where embedded systems do not have |
V. SOFTWARE
|
The best simulation software for electronic designs with microcontroller is proteus8. All microcontrollers are available in it. Hence it gained popularity. To test programs and embedded designs Proteus can be used as a handy tool. The user can simulate his/her programming of microcontroller in proteus design suite simulation software. |
1. Open Proteus ISIS professional and place the necessary Components and wire them. |
2. Double click the processor and select the hex file to be loaded. |
3. Save the design with .dsn extension. |
4. Click on Run button to simulate the design. |
5. After Simulation the circuit in Proteus 8 Software can directly make the PCB design. |
6. Simulation software provides an environment to test our microcontroller program |
7. With proteus design suite you can alter your hardware by rewiring the circuit diagram, varying component values for resistors etc. Removing or making new components to the design. |
8. The user can reprogram microcontroller. The user can change firmware in the IDE of his/her choice |
Here a sample circuit drawn using the components, resistor and LED are shown.These components are available in the library itself. |
Here object selection window is shown which helps to find the necessary components needed for the circuit. The required components are placed in the schematic edit space and the circuit is built. |
The simulation steps starting from writing the code to execution is represented in block diagram. After the successful compilation the program is used for practical implementation. |
Here the compiler we are using is keil |
1. Open Keil μvision and create new project by selecting Project → New μvision project. |
2. After Creating project select the device model as Atmel AT89c51. |
3. Now project is created and message window will appear to add startup file of the device ,click on yes so it will be added to the project folder. |
4. Now select File→ new to open new file and write the program and save it with .cextension. 5. In project window right click on target and click on options . |
6. Click on output tab and check create Hex file to generate hex file 7. Now click on ok so it will save changes. |
8. Right click on source group by expanding target and click on Add files to source group. |
9. Now add the program file saved with .c extension. |
10. Now click on Project →Build target and the status of program is displayed in build output window |
VI.SIMULATION RESULT
|
There are four LEDs indicating the four directions. There are particular range of values for each direction. While reaching those values that particular LED will glow. |
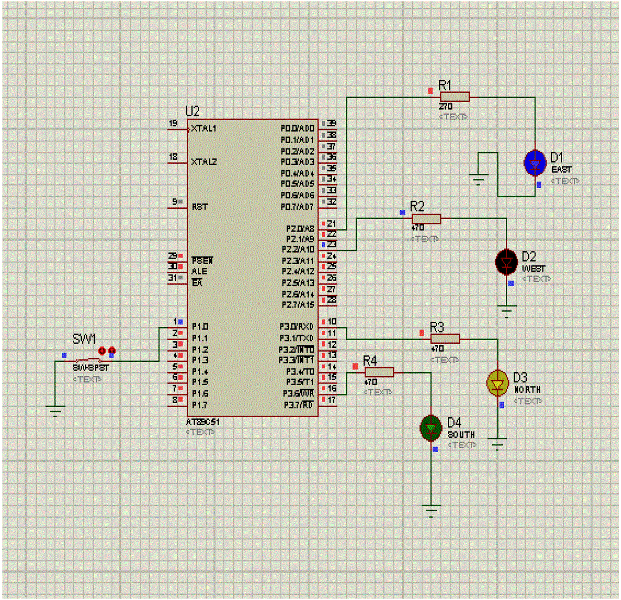 |
VII.CONCLUSION AND FUTURE WORK
|
A monitoring system was developed to measure the parameters of wind turbine.The data acquisition system contains a microcontroller which will be more comfortable to users.The simulation results are obtained using Proteus software.In future a GSM module will be added to the system and the readings are sent to the owner of the wind turbine via short message service |
Figures at a glance
|
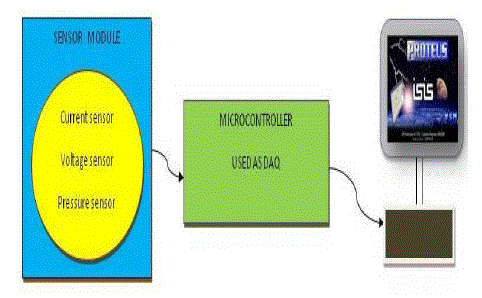 |
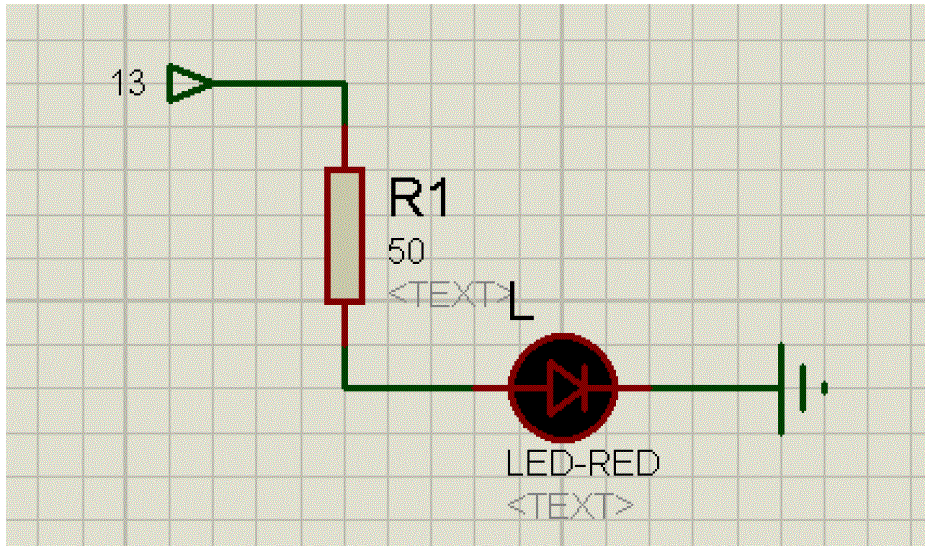 |
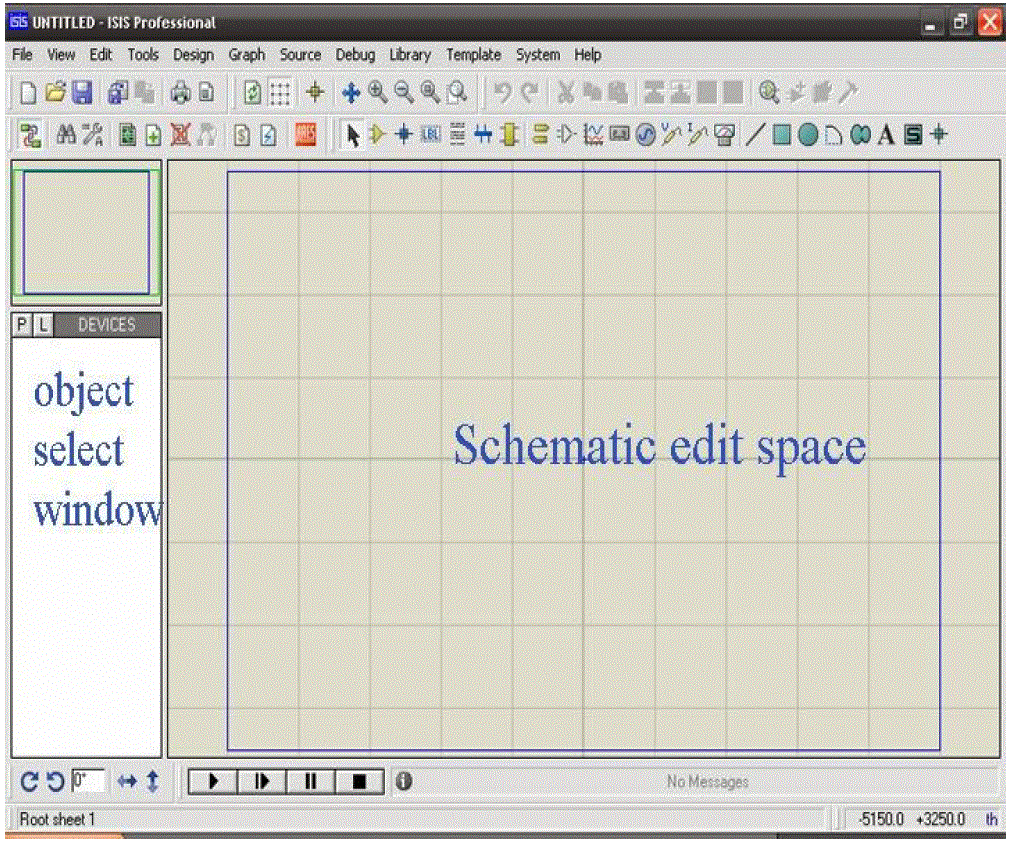 |
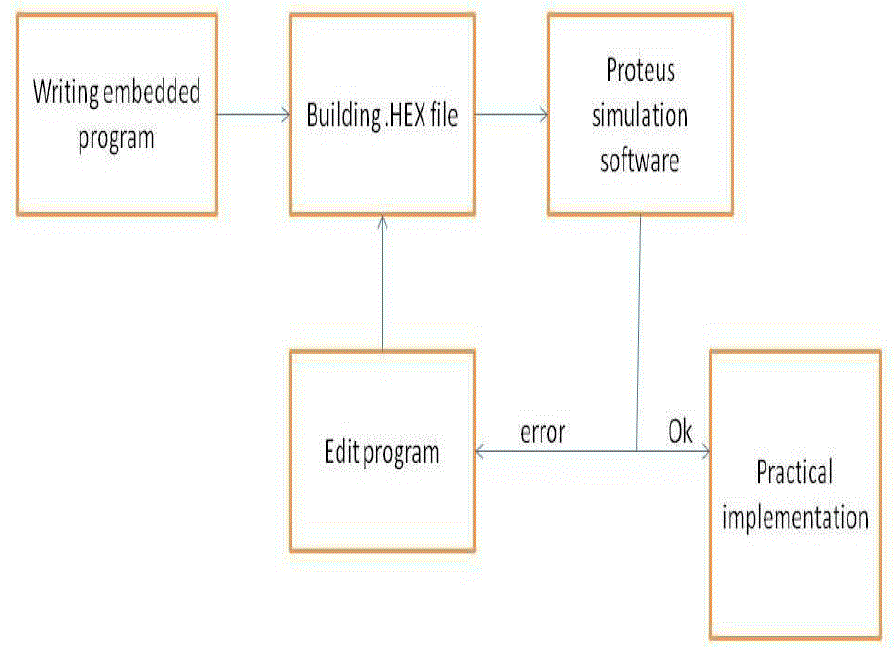 |
Figure 1 |
Figure 2 |
Figure 3 |
Figure 4 |
|
|
References
|
- Amine Yazidi, Humberto Henao, Senior Member, Gérard-André Capolino, Fellow,Franck Betin, and Fiorenzo Filippetti ‘‘A Web-Based Remote Laboratory for Monitoring and Diagnosis of AC Electrical Machines” IEEE Transactions on industrial electronics, October 2011.
- Andrew Cruden, Campbell Booth, Grzegorz Swiszcz1, William Leithead, “A Data Acquisition Platform for the Development of a Wind Turbine Condition Monitoring Condition Monitoring System”, Proceedings of International Conference on and Diagnosis, Beijing, China, April 21-24, 2008
- Dongxiang Jiang, Qian Huang and Liangyou Hong, “Test system of small wind turbine under laboratory conditions”, Proceedings of World Non-Grid-Connected Wind Power and Energy Conference, China, Sep 2009
- Hong-Ling Fu, Wei-Chiang Chang, “Wind Turbine Control Monitor System Simulation and Validation”,proceedings of international symposium on Computer Communication Control and Automation(3CA),2010
- H. C. Lin, “On line Web-based Maximum Wind Power Monitoring and Control System”, Proceedings of IEEE International Conference on Systems, Man, and Cybernetics, Taiwan, October 8-11, 2006.
|