Keywords
|
Hysteresis band pulse width modulated controller (HPWM) ,Indirect vector control of Induction Motor(IVCIM), Voltage source Inverter(VSI) |
INTRODUCTION
|
The effective way of varying speed of an Induction Motor (IM) drive is to supply with three phase Inverter of variable frequency and variable voltage. It can be obtained through a dc voltage link via a current controlled inverter. In order to maintain the proper magnetic conditions in the core the applied voltage /frequency ratio must be constant |
The various methods for the control of output voltage [6] of inverters are (i) External control of ac output voltage. (ii)External control of dc input voltage. If the available voltage is dc, then the dc voltage input to the inverter is controlled by means of chopper. This method is not much used as it involves more losses, reduced efficiency, high cost and complexity.(iii) Internal control of inverter control within the inverter itself. The most efficient method of doing this is by Pulse Width Modulation (PWM) control used within the inverter. PWM inverters are quiet popular and most widely used in all industrial applications. In the present paper the output voltage of inverter is controlled by using HBPWM control |
The PWM principle, different methods of PWM techniques and HBPWM controller is discussed in detail and description of modeling of HBPWM controller in SIMULINK/MATLAB. Simulation block diagram of IVCIM using HBPWM current controller for the inverter is presented and the simulation results are shown. |
PWM CONTROL
|
In this method, a fixed dc input voltage is given to the inverter and a controlled ac output voltage is obtained by adjusting the on and off periods of the inverter components. Inverters employing PWM principle are called PWM inverters. PWM techniques are characterized by constant amplitude pulses. The width of these pulses is modulated to obtain inverter output voltage control and to reduce its harmonic content. The advantages possessed by PWM technique are [8](i)The output voltage control with this method can be obtained without any additional components.(ii)With this method, lower order harmonics can be eliminated or minimized along with its output voltage control. As higher order harmonics can be filtered easily, the filtering requirements are minimized.[1] |
The main disadvantage of this method is that the SCRs are expensive as they must possess low turn on and turn off times. This is the most popular method of controlling the output voltage of an inverter in industrial applications. [2] |
TYPES OF PWM TECHNIQUES
|
There are several types of PWM techniques [4] Sinusoidal PWM (SPWM),Selected harmonic elimination (SHE) PWM, Minimum ripple current PWM, Space vector PWM, Hysteresis band current control PWM (HBPWM),Sinusoidal PWM with instantaneous current control, Sigma-delta modulation . |
The hysteresis band current control PWM has been used because of its simple implementation, fast transient response, direct limiting of device peak current and practical insensitivity of dc link voltage ripple that permits a lower filter capacitor. |
HBPWM CURRENT CONTROL
|
The HBPWM is basically an instantaneous feedback current control method of PWM where the actual current continually tracks the command current within a specified hysteresis band. [3] |
The Fig 1 explains the operation principle of HBPWM for a half bridge inverter. The control circuit generates the sine reference current wave of desired magnitude and frequency, and it is compared with the actual phase current wave. As the current exceeds a prescribed hysteresis band, the upper switch in the half-bridge is turned off and the lower switch is turned on. As a result the output voltage transitions from +0.5Vd to -0.5Vd, and the current starts to decay. As the current crosses the lower band limit, the lower switch is turned off and the upper switch is turned on. The actual current wave is thus forced to track the sine reference wave within the hysteresis band by back- and-forth switching of the upper and lower switches. The inverter then essentially becomes a current source with peak to peak current ripple, which is controlled within the hysteresis band irrespective of Vd fluctuation. The peak-to peak current ripple and the switching frequency are related to the width of the hysteresis band. The HBPWM inverter control method is shown in the Fig 2. The inputs to the HBPWM controller are three phase current errors and the outputs are the switching patterns to the PWM inverter. k in the figure represents the normalization factor and is used for the purpose of scaling the current error input to the HBPWM controller. PS is the pulse separation circuit for the separation of pulses to the IGBTs in the upper and lower leg of the inverter.[4] |
The hysteresis current controller gives output pulses to the inverter according to this rule [7] |
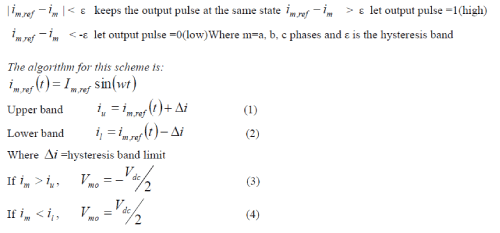 |
Else, maintain the same state. Where m=a, b, c phases i is load current and dc V is the dc link voltage of the inverter.[3] |
The main drawback of this method is that the PWM frequency is not constant and, as a result non optimum harmonics will result. |
SIMULINK MODELOF HBPWM CURRENT CONTROLLER
|
The HBPWM current controller block diagram using SIMULINK/MATLAB is shown below in Fig 4. Current errors for the three phases are determined and a hysteresis block is employed for each phase. The outputs of HBPWM controller, which are pulses, are given to inverter feeding the 3-ø IM. The hysteresis block is available in SIMULINK library in discontinuities and fixed point block set |
SIMULINK MODEL OF IVCIM DRIVE USING HBPWM CONTROLLER
|
To illustrate the operation of HBPWM current controller the simulation model of an IVCIM drive using HBPWM current controller is developed and simulated. The model is shown in Fig 5. The IM block is available in the SIMULINK library in Sim Power Systems block set. The motor specifications can be specified by double clicking the block. The IM is squirrel cage type and the synchronous reference frame is selected. The motor block is internally d-q modeled.[5] |
The reference inputs to the system are the reference speed (ωref) in radians per second, the flux linkages (flux*) and the load torque (Load torque) The required outputs are the developed electromagnetic torque (Te) and the rotor speed (ωm). |
VECTOR CONTROLLER
|
The inputs to the vector controller are rotor reference flux (flux*) and difference in reference speed and actual motor speed (ωerr ). Flux* is used to generate ids * . ids *is the control current to control ids, where ids is the d-axes component of stator current. The Fig 6 shows the vector controller for the IM drive. |
 |
 |
iqs * is the control current to control iqs, where iqs is the q-axes component of stator current. ïÃÂ÷err is used to calculate iqs *using algorithm. A PI controller is used to generate the reference torque Te * from ïÃÂ÷err. The gain constants KP and KI of the PI controller chosen are 16 and 32 and are selected by performance. The Rotor flux is calculated from the equation (5) |
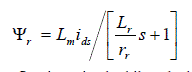 |
The dynamic part of the flux is omitted while calculating the reference rotor flux. This is because the rotor flux is constant in steady state. The iqs * is calculated using Te * and flux*. |
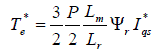 |
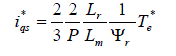 |
Slip speed denoted by ωsl in rad/sec is calculated using Phir (rotor flux) and iqs (q-axes component of stator current) from the following equation 4 |
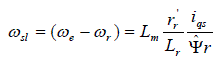 |
The synchronous speed ωe and therefore theta are calculated using the equations 5 and 6 respectively. |
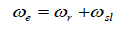 |
 |
(ABC-DQ) TRASNFORMATION
|
The a-b-c to d-q transformation can be implemented by the SIMULINK model shown in the Fig 7. |
Transformation matrix used for a-b-c to d-q transformation is given by the following equation 13 |
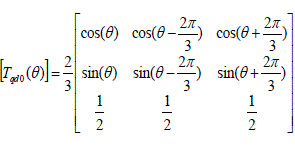 |
(DQ-ABC) TRANSFORMATION
|
The d-q to a-b-c transformation can be implemented by the SIMULINK model shown in the Fig 8. |
Transformation matrix used for d-q to a-b-c transformation is given by the equation (14). |
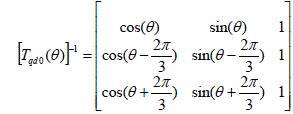 |
SIMULATION RESULTS AND DISCUSSIONS
|
The simulation results of the IVCIM drive employing HBPWM controller with an inverter and an IM with the following specifications are considered. |
Inverter: DC link voltage (Vdc) = 428.76V |
The dc link voltage Vdc should be around 1.453VL where VL is R.M.S value of line voltage. |
Sampling time (Ts ): 1.8μs,Hysterisis Band width of HBPWM current controller is 0.03. |
Induction motor: 3 phase, 6 hp, 440 V, 4-pole Frequency: 50 Hz Stator resistance ( rs): 0.007 ohm. Rotor resistance ( rrL) ecnatcudni egakaeL rotatS .mho 820.0 :( Ãâóls): 0.8 mH. Rotor Leakage inductance (Llr gnizitengaM .Hm 8.0 :( Ãâó inductance (Lm):34.7 mH |
The motor has high starting torque of about 10 to 12 times the load torque. But in the graph the starting torque is seen to be constant at three times the load torque. In the vector controller circuit for iqs * generation where a PI controller is used to generate the reference torque, a saturation limit of three times the load torque is set. |
It can be seen from the graph that the disturbance in load is given even before the drive reached the post disturbance speed 160 rad/sec. Now if the drive is left as such without any further disturbance, it stabilizes at around 3.277 sec. But the step disturbance of 50 rad/sec in speed given at 2.2 sec causes the drive to stabilize at around 3.5 sec. |
HBPWM controller, when there is a step disturbance in load torque and speed at 1.9 sec and 2.2 sec respectively. Pre and post disturbance values of load torque are 100 N-m and 150 N-m respectively.. This dip can be reduced by proper selection of gain constants of the PI controller generating the reference torque Te *. As the speed of motor reaches the reference value of 100 rad/sec, the developed torque reaches a final value of 170 N-m. |
It can be observed from the graphs shown in Figs 13 and 14(a) that when the current error input to the HBPWM controller is not normalized i.e. k=1, the input current to the stator of IM is smooth but with the normalization factor k=0.003 the input current to the stator of IM is distorted and there is an increase in torque pulsations in the developed torque. The Fig 3.14(b) shows the zoomed portion of the stator current in the in the Fig 3.14 (a). Further normalization causes further distortion of input current and increase in the pulsations in the torque waveform. |
If any one of the inputs to the HBPWM current controller is zero the IM drive ceases to work as the input current to the IM motor becomes zero. The graph in the Fig 15 shows current input to the motor when A-phase current error input to the HBPWM current controller is zero. |
The switching loss of the inverter using HBPWM controller in the IVCIM drive is calculated by defining a ratio α as follows: |
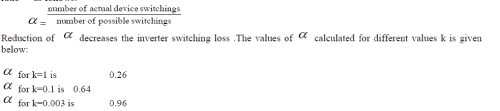 |
Total Harmonic Distortion: |
The total harmonic distortion (THD) is a measure of closeness in shape between a waveform and its fundamental |
component and is defined as 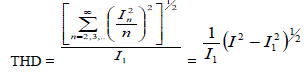 |
where, n I = RMS value of the nth harmonic component of the current 1 I = RMS value of the fundamental component of the current . I = RMS value of the total current. The % total harmonic distortion (%THD) of the input current to the stator of the IVCIM using HBPWM controller for hysteresis band widths of 0.02 and 0.5 are shown in the Table 1: |
CONCLUSIONS
|
In this Paper the working principle of HBPWM current controller and its modeling in SIMULINK for an inverter control is discussed. As its application, an IVCIM drive is modeled and the results are shown. The hysteresis band width of the HBPWM current controller is 0.02. The speed, torque responses, stator current waveforms, inverter switching losses and %THD of the stator current of the IVCIM. |
Tables at a glance
|
 |
Table 1 |
|
Figures at a glance
|
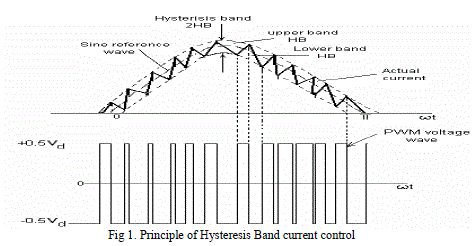 |
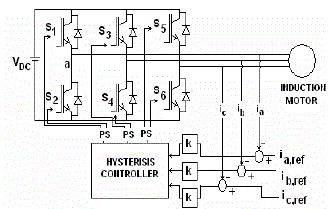 |
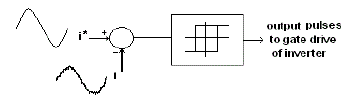 |
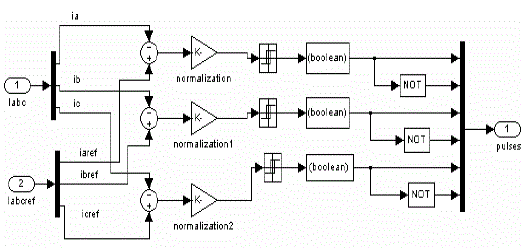 |
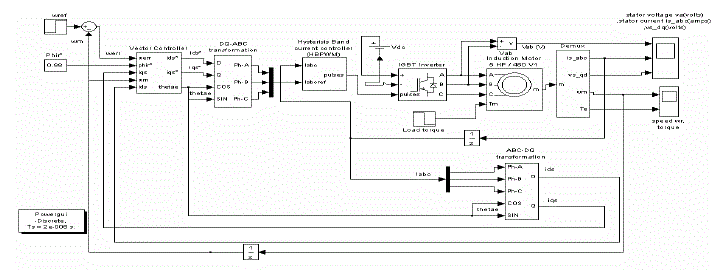 |
Figure 1 |
Figure 2 |
Figure 3 |
Figure 4 |
Figure 5 |
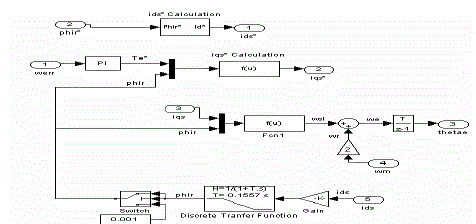 |
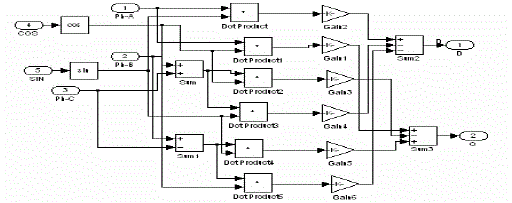 |
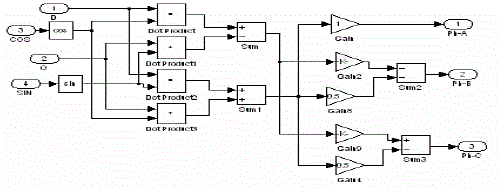 |
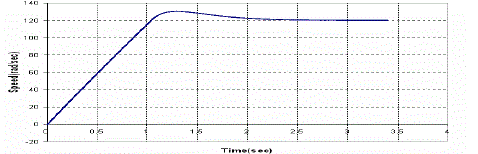 |
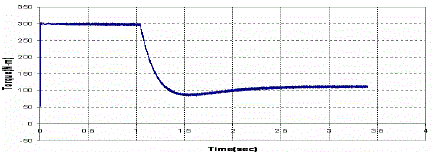 |
Figure 6 |
Figure 7 |
Figure 8 |
Figure 9 |
Figure 10 |
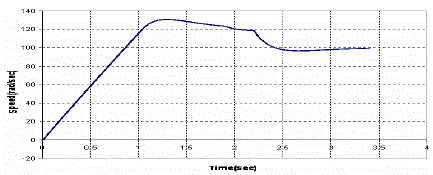 |
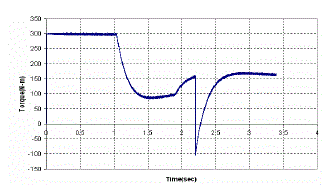 |
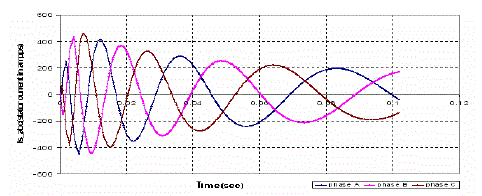 |
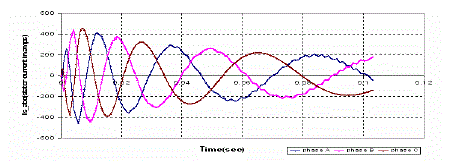 |
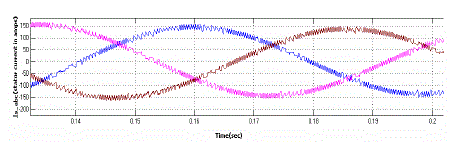 |
Figure 11 |
Figure 12 |
Figure 13 |
Figure 14 |
Figure 14b |
|