Keywords
|
Curvature Sensor,Human Joint Overseeing,Optical-FibreSensor ,Wearable Electronics, Wearable Computing, GSM(Global System For Mobile Communications). |
INTRODUCTION
|
Right now, there are expanding market needs for the estimation of quick varieties of the human joint developments. The purpose behind this expanded necessity for screening human joint developments is on account of there are numerous restorative provisions which could profit from it. Restorative provisions are different and the most widely recognized are non-intrusive treatment and recovery [1]. A few cases of therapeutic provisions are element measuring of lumbar arch [2], element observing. element observing of finger joints [3]–[5], overseeing of appendages [6]–[8] and numerous others. Notwithstanding solution, overseeing of human joint developments likewise gives profits in games [9], [10] .therefore, the sensor has the likelihood of remote estimation. The fundamental focal points of this sensor are straightforwardness, delicacy, and adaptability. This sensor is likewise electrically protected and resistant to electromagnetic impedance. |
For these provisions, both in pharmaceutical and games, it is important to measure the element point varieties. Mechanisms utilized for this object are mechanical or electromechanical goniometers, which are actualized utilizing resistive potentiometers or strain gages. The most solid frameworks for element rakish estimations are electrogoniometers.in [11] an electrogoniometer for wearable carriage and motion catch frameworks which presents a technique for discovering joint edges by utilizing piezoresistive strain touchy materials is demonstrated. Notwithstanding electrogoniometers, goniometers dependent upon optoelectronics are regularly utilized. An optical goniometer for human joint edge estimation which permits persistent and longterm checking of human joint movement in commonplace setting dependent upon a chip from optical mouse is accounted for in [12].dynamic goniometer with an incremental encoder utilizing a mechanical transmission between a pivot and a pulley associated with an optical plate is accounted for in [13]. |
For these provisions, both in pharmaceutical and games, it is important to measure the element edge varieties. Mechanisms utilized for this reason for existing are mechanical or electromechanical goniometers, which are Fiberoptic sensors [14]–[16] are habitually utilized for human joint points observing. Typically the sensor for this requisition is dependent upon power tweak, and the most well-known usage are dependent upon force balance because of bowing of optical fiber. The otherworldly based fiber-optic sensor executions with fiber Bragg grating (FBG) sensor have been as of late distributed [5].The sensors dependent upon the curving of optical fiber have low affectability. There are a few strategies to enhance the affectability of the fiber-optic sensor dependent upon fiber twisting, for example, by utilizing flawed fiber and by utilizing side cleaned strands [17], [18]. The fiber-optic sensors dependent upon the bowing of plastic optical fiber with structural blemishes on the external side of center are accounted for in [19], [20]. The affectability of the sensors [19], [20] was enhanced considerably all the more by expanding the profundity of the fiberdefects.With the presentation of the fiber-optic ebb and flow sensor with a touchy zone [21], the affectability is not an issue any longer actually for the most requesting requisitions. Expository advancement of the curve sensor with a touchy zone is accounted for in [22].This paper displays a sensor framework for checking the developments of human joints dependent upon fiber-optic shape sensor with a touchy zone. The ensuing curve sensor is made plastic optical fiber (POF).the SMS door to send and accept SMS for the screening knee joint Recognize conspire on every fruitful SMS delivery.in expansion to GSM estimations in Proteus and VB programming bundle are executed. In [25] a framework for element rakish developments screening dependent upon polarization change because of the joint pivot, is introduced. In correlation to sensor from [25], the sensor exhibited in this paper is more basic and less expensive. |
The focal point of transformed sensor contrasted with the long ago specified framework is better affectability. In correlation to FBG sensors for joint observing the ensuing sensor is portrayed by minimal effort outline. The plastic optical fiber is much less expensive than the FBG, and it doesn't require exorbitant session framework as on account of the FBG. Additionally, the ensuing human joint development checking framework with sending information through GSM, which gives a plausibility of nonstop and long haul following. This vital characteristic makes the proposed sensor framework a finer result in correlation to other sensing frameworks for human joint developments following. |
LITERATURE REVIEW
|
Jovan S. Baji´cIn this paper, the characteristics of the sensor measured in laboratory conditions as well as measurements of the human knee joint Movements are given. In this paper sensor Sensitivity and resolution, in the measurement range, are 20 mV/° and 1°, respectively. The fabrication process of proposed curvature sensor is also given. Wireless electronics based on ZigBee are also presented. Therefore, the sensor has the possibility of wireless measurement. The application, which provides a possibility of remote human joints monitoring over the internet is implemented in the LabVIEW software package. |
Haiting Di A novel fiber-optic sensor that can measure curvature directly has been developed previously. In this paper, the transduction of curvature to light intensity is described analytically by using the geometrical optics analysis. The mathematical model allows a quantitative optimization of the sensor without having to produce many sensors with slightly different combinations of parameters in order to accomplish a similar objective experimentally. The Monte Carlo simulation by ray tracing and an orthogonal matrix are used to optimize the fiber-optic sensor’s configuration. The results show that the depth of the sensitive zone and the number of teeth are two main parameters that affect the sensor’s sensitivity and the optimum number of teeth is 55, which is in agreement with the mathematical model. |
Haiting Di A novel fiber-optic sensor that can measure curvature directly has been developed previously. In this paper, the transduction of curvature to light intensity is described analytically by using the geometrical optics analysis. The mathematical model allows a quantitative optimization of the sensor without having to produce many sensors with slightly different combinations of parameters in order to accomplish a similar objective experimentally. The Monte Carlo simulation by ray tracing and an orthogonal matrix are used to optimize the fiber-optic sensor’s configuration. The results show that the depth of the sensitive zone and the number of teeth are two main parameters that affect the sensor’s sensitivity and the optimum number of teeth is 55, which is in agreement with the mathematical model. |
Daniel A. James A sensor data acquisition platform has been developed for in-situ sporting applications encompassing stand-alone high speed sampling and storage of multiple accelerometer data. Ambulatory monitoring of elite athlete in competition or training environments was then undertaken. The platform itself is divided into functional blocks and controlled by a small microcontroller using a custom OS. Hence it is easily customizable for a variety of sporting applications. The platform is packaged so as to be robust, hermetically sealed and biomechanically neutral to the athlete.Results and derivative data from rowing and swimming are presented as sample applications. In swimming applications, stroke characteristics for a variety of training strokes are analyzed and found to be better than hand timed data and comparable with results obtained from technology and labor intensive methods, including video analysis. |
PROPOSED WORK
|
The overall block diagram Fig.1. As the major electronic device run in the DC, the construction of a power supply is necessary. The uses step- down transformer for steeping down the 220V AC to 12V AC. A bridge rectifier is used to rectify the 12V AC into 12V DC.The IC regulator is used to convert 12V DC to 5V DC. The power supply is getting constant 5V DC as output. The curvature sensor is optimized for small curvature measurements, and has a high sensitivity in a wide measuring range. The power supply and curvature sensor is connected to PIC controller. The 5V DC is given input to PIC micro-controller. It has 40pin IC.The only 35 single-word instructions to learn.The Operating speed is DC – 20 MHz clock input and DC – 200 ns instruction cycle.Up to 8K x 14 words of Flash Program Memory,Up to 368 x 8 bytes of Data Memory (RAM),Up to 256 x 8 bytes of EEPROM Data Memory. Pinout compatible to other 28-pin or 40/44-pin PIC16F877A microcontrollers. The LCD and GSM is connected to PIC microcontroller. |
Wireless communication electronics based on GSM standard, by which the sensing part of the system communicates with a Mobile Station, is developed for this sensor.Here using 16×2 LCD display for displaying output. |
Fig. 2 shows a block diagram of the experimental setup for angular movement measurement. For laboratory tests sensor is mounted on an improvised joint, which is attached to a precise manual rotation stage (MRS) produced by Thorlabs, Inc. As a light source and detector, LED and transistor are used. High power LED, BC 547 with the peak wavelength of 660 nm, and NPN transistor produced by Industrial Fiber Optic, Inc are used.The transistor provides a very high optical gain,eliminating the need for the post amplification. |
The integrated design of the BC 547 makes it a simple, cost-effective solution in a variety of applications. Optical response of the BC 547extends from 400 to 1100 nm, making it compatible with a wide range of visible and nearinfrared LEDs and other optical sources.This includes 650 nm visible LEDs used for optimum transmission in POF.Both source and detector are housed in a “connector-less” style plastic fiber-optic package, to which POF can be easily connected.As PIC microcontroller is used.This microcontroller is used because it is appropriate for the desired application tasks, and it is very cheap and small.PIC drives LED, measures a signal from NPN tansistor by using 10 bit A/D converter, and communicates with a Mobile Station via GSM module.Power supply for whole device is stabilized to 3.3 V with step-down voltage stabilizer. In Fig. 3 a photograph of the produced curvature sensor with an improvised joint mounted on the precise MRS is shown. |
As we can see from the block diagram, the system produced is designed for wireless and long-term remote monitoring. Measured values can then be Displayed in LCD screen, analysed, recordedon a Mobile station and distributed via GSM module. The power supply voltage for these modules can be in the range from 2.8 to 3.4 V. GSM modules provide a possibility to build an easy to configure network, with a high data rate up to 250 000 Baud/s. For the configuration of the GSM module, Proteus and Visual Basic software is used. Connection of the GSM module to the microcontroller is done by using 4 wires: Power-Supply (3.3 V), Ground, TX and RX.When operating in this mode, the modules act as a wireless serial communication (UART).In this mode it is necessary that all modules have the SMS balance, both a module, which sends data, and all other modules that receive data. In this work, communication with two modules is implemented, but in order to obtain a wireless sensor network, communication with more modules can be easily implemented. Doctor and Patient applications are implemented in Proteus and Visual Basic software. The Doctor application receives data from GSM, and graphically displays and captures measured data. These data from the GSM are available for remote overseeing. The potential errors arising from the connector imperfections, misalignment of light sources and detectors and other effects that are not related to the angle variation are reduced by simple calibration. The curvature sensor was mounted on a commercial knee joint brace and the signal was measured, recorded and analysed. |
STIMULATION OUPUT
|
In Fig. 3 The proteus software package splits into three parts very conveniently namely,ISIS(Intelligent Schematic Input System) for drawing circuit diagram etc., ARES(Advanced Routing and Editing Software) for producing PCB layout drawings, LISA(Lab center Integrated Simulation Architecture) for simulation of circuit diagram. |
The curvature sensor is connect to PIC microcontroller. The manually we want change the angle in the curvature sensor.We set angle 80 degree in the curvature sensor. If angle is excited above 80 degree the message will sent. The message is will display in the LCD display. |
CONCLUSION
|
A simple and low-cost fiber-optic curvature sensor based on intensity modulation together with its application in the human joint angle monitoring is presented. The proposed sensor is suitable for the medical and sports applications, and it is wearable, non-invasive, nonintrusive and completely harmless. Here conclude that SMS based frame work will reduce the time delay in collection and transferring the data to Doctor by using mobile. This system is more efficient and it can be extended for World wide.Wireless communication electronics based on GSM standard, by which the sensing part of the system communicates with a Mobile Station, is developed for this sensor. |
By carefully guiding the lead-in and lead-out fiber sections to the box with the electronics we have avoided the errors that can cause losses in the light transmission. Another way to further minimize these losses is to use the optical fibre with smaller core diameter which are more resistant to the bending. As a logical extension of this work we propose the minimization of the complete angular joint monitoring system to be integrated on the knee brace. In this way, the leadin and lead-out fiber sections lengths will be minimized which would result in smaller error due to the leading and leadout fiber sections bending. The curvature sensor should be placed as close as possible to the light source and photo detector pair in order to improve the sensor performance.. The resulting fiber-optic sensing system compared to the fiber-optic implementations mentioned in the introductory part of this paper has the advantages of higher sensitivity and very simple and low-cost design. Although the measurement system presented here uses very cheap digital microcontroller, it works reliably and with a small measurement error. |
This option is suitable for the continuous monitoring of simple daily, sports and rehabilitation activities. The implemented sensor is mounted on a commercial knee joint brace and its signal is measured. The developed measurement system is cheap, simple, and with some modifications, such as miniaturization, can be produced for commercial purposes. |
Figures at a glance
|
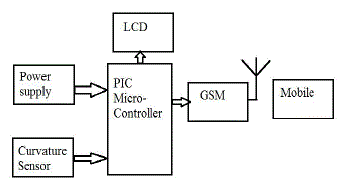 |
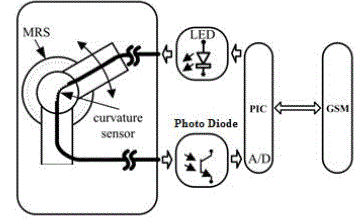 |
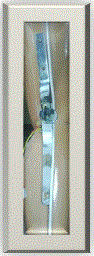 |
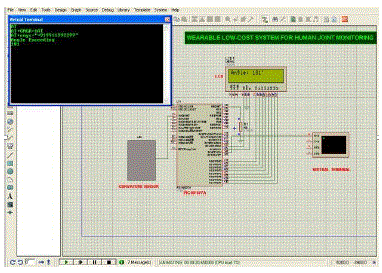 |
Figure 1 |
Figure 2 |
Figure 3 |
Figure 3a |
|
References
|
- R. Eston and T. Reilly, Kinanthropometry and Exercise Physiology Laboratory Manual: Tests, Procedures and Data, 3rd ed. Evanston, IL:Routledge, 2009.
- J. M. Williams, I. Haq, and R. Y. Lee, “Dynamic measurement of lumbar curvature using fibre-optic sensors,” Med. Eng. Phys., vol. 32, no. 9, pp.1043–1049, Nov. 2010.s
- J. T. Dennerlein, D. L. Jindrich, and A. D. Balakrishnan, “Finger joint impedance during tapping on a computer keyswitch,” J. Biomech.,vol. 37, no. 10, pp. 1589–1596, Oct. 2004.
- J. E. Nelson, D. E. Treaster, and W. S. Marras, “Finger motion, wrist motion and tendon travel as a function of keyboard angles,”Clin.Biomech., vol. 15, no. 7, pp. 489–498, Aug. 2000.
- A. F. Silva, A. F. Gonçalves, P. M. Mendes, and J. H. Correia, “FBG sensing glove for monitoring hand posture,” IEEE Sensors J., vol. 11,no.10, pp. 2442–2488, Oct. 2011.
- H. Hu, H. Zhou, T. Stone, and N. Harris, “Use of multiple wearable inertial sensors in upper limb motion tracking,” Med. Eng. Phys., vol.30,no. 1, pp. 123–133, Jan. 2008.
- F. C. Schasfoort, J. B. J. Bussmann, and H. J. Stam, “Ambulatory measurement of upper limb usage and mobility-related activities duringnormal daily life with an upper limb-activity monitor: A feasibility study,” Med. Biol. Eng. Comput., vol. 40, no. 2, pp. 173–182, Mar.2002.
- H. Zhou and H. Hu, “Inertial sensors for motion detection of human upper limbs,” Sensor Rev., vol. 27, no. 2, pp. 151–158, 2007.
- A. J. Wixted, D. V. Thiel, A. G. Hahn, C. J. Gore, D. B. Pyne, and D.A. James, “Measurement of energy expenditure in elite athletes usingMEMS-based triaxial accelerometers,” IEEE Sensors J., vol. 7, no. 4,pp. 481–488, Apr. 2007.
- F. G. Quiroz, A. V. Moreno, and M. R. Peláez, “Development of a dynamic goniometer with an incremental encoder,”RevistaIngenieríaBioméd., vol. 1, no. 1, pp. 28–32, May 2007.
- J. Rantala, J. Hännikäinen, and J. Vanhala, “Fiber optic sensors for wearable applications,” Personal Ubiquit. Comput., vol. 15, no. 1, pp.85–96, Jan. 2011.
- S. Yin, F. T. S. Yu, and P. B. Ruffin, Fiber Optic Sensors, 2nd ed. New York: Taylor & Francis, 2008.E. Udd and W. B. Spillman, Fiber OpticSensors: An Introduction for Engineers and Scientists, 2nd ed. New York: Wiley, 2011.
- K. S. C. Kuang, W. J. Cantwell, and P. J. Scully, “An evaluation of a novel plastic optical fibre sensor for axial strain and bendmeasurements,”Meas. Sci. Technol., vol. 13, no. 10, pp. 1523–1534, Oct. 2002.
- L. Bilro, J. G. Oliveira, J. L. Pinto, and R. N. Nogueira, “A reliable low cost wireless and wearable gait monitoring system based on a plasticopticalfibre sensor,” Meas. Sci. Technol., vol. 22, no. 4, pp. 1–7, Apr.2011.
- A. Babchenko and J. Maryles, “A sensing element based on 3D imperfected polymer optical fibre,” J. Opt. A, Pure Appl. Opt., vol. 9,no. 1, pp.1–5, Jan. 2007.
- . A. Babchenko, Z. Weinberger, N. Itzkovich, and J. Maryles, “Plastic optical fibre with structural imperfections as a displacement sensor,”Meas.Sci. Technol., vol. 17, no. 5, pp. 1157–1161, May 2006.
- A. Djordjevich and M. Boskovic, “Curvature gauge,” Sensor Actuat. A,Phys., vol. 51, nos. 2–3, pp. 193–198, 1996.
- M. S. Kovacevic, A. Djordjevich, and D. Nikezic, “Analytical optimization of optical fiber curvature gauges,” IEEE Sensors J., vol. 8, no. 3,pp.227–232, Mar. 2008.
- Y. Fu, H. Di, and R. Liu, “Light intensity modulation fiber-optic sensor for curvature measurement,” Opt. Laser Technol., vol. 42, no. 4,pp.594–599, Jun. 2010.
- H. Di and Y. Fu, “Fiber-optic curvature sensor with optimized sensitive zone,” Opt. Laser Technol., vol. 43, no. 3, pp. 586–591, Apr.2011.
- A. Djordjevich and M. Boskovic, “Curvature gauge,” Sensor Actuat. A,Phys., vol. 51, nos. 2–3, pp. 193–198, 1996.
- M. S. Kovacevic, A. Djordjevich, and D. Nikezic, “Analytical optimization of optical fiber curvature gauges,” IEEE Sensors J., vol. 8, no. 3,pp.227–232, Mar. 2008.
- M. Donno, E. Palange, F. D. Nicola, G. Bucci, and F. Ciancetta, “A new flexible optical fiber goniometer for dynamic angular measurements:Application to human joint movement monitoring,” IEEE Trans. Instrum. Meas., vol. 57, no. 8, pp. 1614–1620, Aug. 2008.
|