Keywords
|
Optofluidics, Microfluidics, Polydimethylsiloxane (PDMS), Nanoparticles. |
I. INTRODUCTION
|
The term “optofluidics” was coined in 2003 to define an emergent research field that focuses on combining microfluidic and optical technology[1]. The term “optofluidics” first appeared in the name of a University Research Center funded by the Defense Advanced Research Projects Agency (DARPA) in 2003. The charter of the center was to “develop adaptive optical circuits by integrating optical and fluidic devices.” This optics-centric definition points to an interesting aspect of this field’s origin optics researchers were trying to incorporate microfluidic technologies into their research to create novel optical devices. Optofluidics refers to a class of optical systems that are synthesized with fluids. Fluids have unique properties that cannot be found in solid equivalents, and these properties can be used to design novel devices. Examples of such properties include: the ability to change the optical property of the fluid medium within a device by simply replacing one fluid with another, the optically smooth interface between two immiscible fluids and the ability of flowing streams of miscible fluids to create gradients in optical properties by diffusion[2]. Most optical systems are currently made with solid materials such as glasses, metals and semiconductors, but there are cases in which it has been advantageous to use fluids. The oil-immersion microscope, liquid mirrors for telescopes, liquidcrystal displays and electrowetting lenses are good examples. |
Integration and reconfigurability are two major advantages associated with optofluidics. Whereas microfluidics has made it possible to integrate multiple fluidic tasks on a chip, most optical components, such as the light source, sensors, lenses and waveguides, remained off the chip. Optofluidic integration combines optics and microfluidics on the same chip by building the optics out of the same fluidic toolkit. The second advantage of optofluidics lies in the ease with which one can change the optical properties of the devices by manipulating fluids[3]. |
Microfluidic is a burgeoning field with important applications in areas such as biotechnology, chemical synthesis and analytical chemistry[4]. Many of these applications of microfluidics are discussed elsewhere in this issue, and for the purposes of this review we emphasize only a few salient points. First, there is now an extensive body of literature on how the physical properties of fluids that are available only on small spatial scales can be exploited for device functionality. Many of these effects can also be used to control optical properties. Second, technological advances in device fabrication have made it possible to build miniaturized devices with complex networks of channels, valves, pumps and other methods of fluidic encapsulation and manipulation. This creates a powerful set of tools for |
fluidic control, and because the feature sizes in these systems are shrinking over time, they will inevitably approach the wavelength of visible light. When this convergence happens, optofluidic-device applications will increase dramatically, just as the ability to lithographically define features with dimensions just below the wavelength of light has created a revolution in photonics. Third, a large anticipated market for microfluidics lies in portable devices for environmental monitoring, medical diagnostics and chemical-weapon detection. Optofluidics is helping to realize these aspirations by combining optical elements into microfluidic devices in ways that increase portability and sensitivity. |
Although any microfluidic fabrication method can, in principle, be adapted to synthesize optofluidic devices, most of the implementations thus far have been with soft lithography. Soft lithography allows rapid fabrication of complex microfluidic structures in flexible polymer substrates at a fraction of the cost of traditional glass or semiconductor manufacturing.Although the most popular polymer is polydimethylsiloxane(PDMS),many other materials are suitable,such as photo curable hydrogels,thermoset plastics and elastomers, and photo curable solventresistant elastomers such as perfluoropolyethers (PFPE)[6]. The optical transparency and good optical quality of PDMS has been demonstrated in applications such as soft lithographic fabrication of blazed gratings and solid immersion lenses, showing that these materials are suitable in the optofluidic context. |
II. OPTOFLUIDICS
|
Optofluidics is the complementary merging of photonics and fluidics. In optofluidic systems, fluids give fine adaptability, mobility and accessibility to nanoscale photonic devices which otherwise could not be realized using conventional devices. However, homogeneous fluids have regulated properties with limited functionalities. Fluids should have unique and novel properties in order to develop optofluidic systems which are applicable for a wide range of practical problems. To this end, various colloidal particles are added into the fluids to provide specific physical, chemical and biomolecular functionalities. This introduction of colloidal dispersion will lead to a breakthrough for optofluidic systems. Optofluidics enables on chip optical manipulation of nano /micro-sized objects in micro fluidic channels, thereby providing a non-intrusive method to optically manipulate micro particles in a small fluidic sample volume. |
`III. FABRICATION
|
Most research in microfluidic systems is now carried out in PDMS and other polymers. Fabrication in polymers is easier, more flexible, and much less expensive than in silicon or glass. It also avoids other problems of hard materials (e.g., formation of sharp shards on breakage) and enables certain components (e.g., pneumatic valves) that cannot be fabricated in rigid materials. In the following sections, we will focus on the use of PDMS for the development of microfluidic systems. PDMS has several attractive properties that make it suitable as a material for rapid prototyping of microfluidic devices capable of supporting a wide range of applications. Systems in PDMS are typically fabricated using techniques in soft lithography. Soft lithography involves the replication of a topographically defined (typically in photo resist) structure on a master in soft elastomers. The process can be carried out in ambient laboratory conditions. Replication can also be repeated multiple times. Soft lithography therefore enables rapid, simple, and inexpensive fabrication processes. The details of fabrication using soft lithography can be found elsewhere. Here we provide a summary of the processes involved. The microfluidic channels are designed in a CAD program and printed onto a high-resolution transparency (~5000 dpi) (or, somewhat less conveniently and more expensively, converted into a conventional chrome mask). |
This transparency is used as a photo mask in 1:1 contact photolithography (usually using SU-8 or PMMA as photo resist) to produce a master. This master consists of a positive bas-relief of photo resist on a silicon wafer, and serves as a mold for PDMS. Liquid PDMS prepolymer is poured over the master and cured for 1 h at 70°C. The PDMS replica is then peeled from the master and sealed (following plasma oxidation of the interfaces involved) to a flat PDMS, glass, or silicon surface to form the microfluidic channels. The overall process takes approximately 24 h. Figure 1 shows a schematic diagram of the procedures involved. |
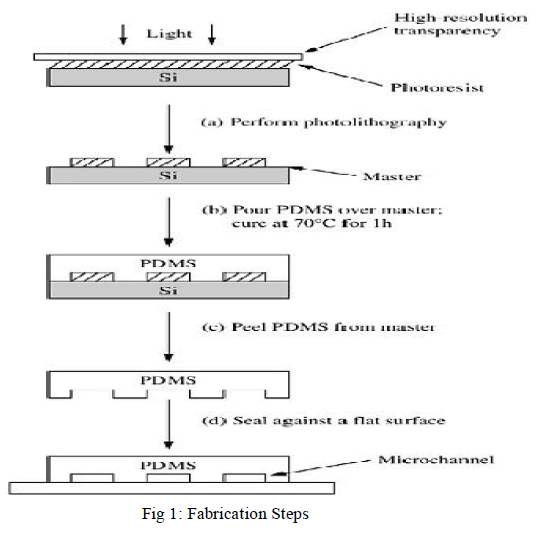 |
III.1 L2 Lenses. |
The design of the L lens is similar to that of the L2 waveguide, it is formed by laminar flow of three streams of fluids; the index of refraction of the central (“core”) stream is higher than the index of the sandwiching (“cladding”) streams [13]. The streams enter a microchannel containing an “expansion chamber”—a region in which the width of the channel expands laterally. |
Figure 5.4 shows a schematic diagram of this system. The expansion chamber is typically 10 times wider than its entrance and exit. For some rates of flow, the shape of the interface between the core and clad-ding streams in the expansion chamber is biconvex. This fluidic biconvex structure focuses light propagating in the plane of the expansion chamber, and perpendicular to the direction of flow of the liquids. By changing the relative rates of flow of the three streams, it is possible to change the curvature of the interface and thus the focal distance of the lens in real time. |
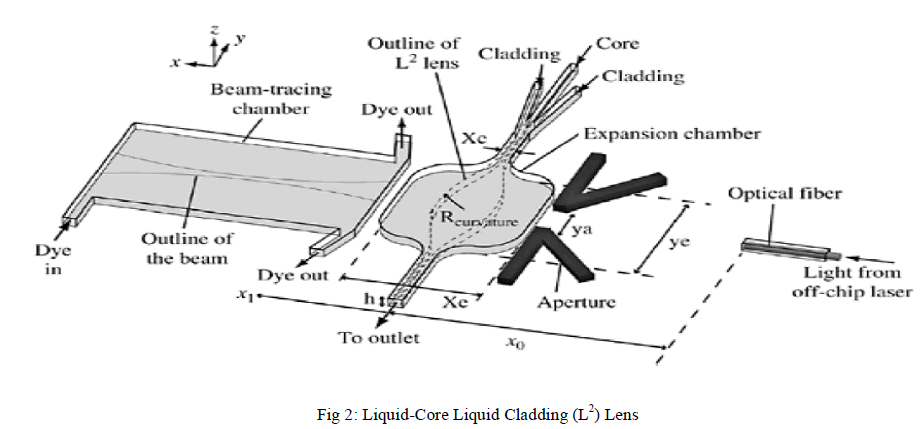 |
Figure 5.5 shows the shapes of the lens under different flow conditions. Since the height of the expansion chamber was much smaller than its width and length, the flow was quasi-two-dimensional, and the L lens is roughly cylindrical[13]. When the rates of flow of the left and the right cladding streams were the same, the core stream, or the L lens, was biconvex and symmetrical inside the expansion chamber. Varying the relative flow rates between the left and the right claddings varies the curvatures of the left and right interfaces separately. It is therefore possible to obtain an extensive range of lens shapes: meniscus, plano-convex, and biconvex. |
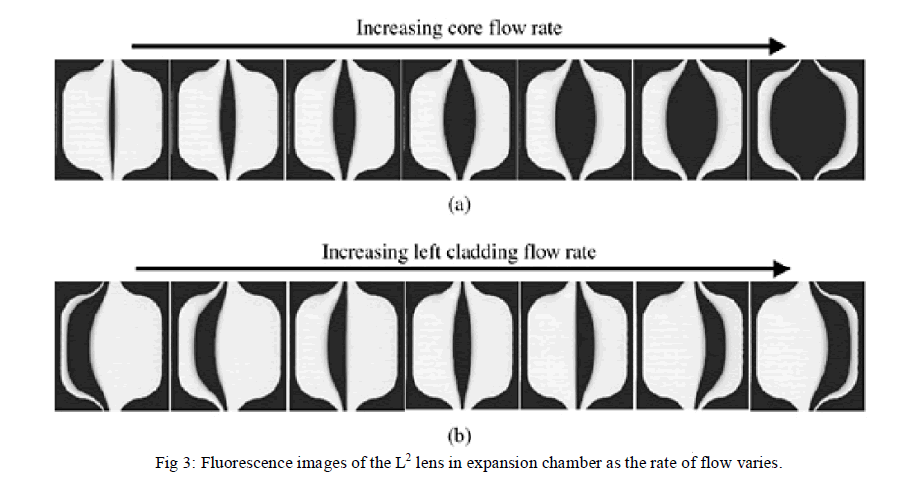 |
IV. CONCLUSION
|
Optofluidics is a rapidly growing field. The permutations of optics and micro fluidic combinations are numerous and exciting to explore; we can reasonably expect this field to continue its rapid growth over the next decade. Optofluidics have brought about new and potentially better ways to build or use established optical structures and devices. Some of the growth directions in recent years have also been remarkably unanticipated. We conclude by noting that optofluidics is a field still in its infancy. It is full of promise, but few devices have been successfully commercialized as of yet. Many technological elements and even some fundamental concepts are just now being developed. As technological tools, optofluidic devices are good complements to micro-electromechanical systems (MEMS). Where MEMS physically actuate solid components to achieve reconfigurability, optofluidic devices reconfigure themselves through fluidic controls. One currently understudied area that is especially noteworthy is the optical control of fluids. Such controls can dramatically simplify fluid manipulation by completely removing the need for on-chip plumbing.We believe that the field of optofluidics will continue to surprise us with its new and unique devices and techniques. |
|
References
|
- Ai–Qun-Liu., “Approach of optofluidics from optics to photonics ” IEEE Conference., August 2012, pp. 53-54.
- Bains, S., “Going with the flow [optofluidics]” , IEEE Review., vol.52 , no. 3, March 2006, pp 42-45.
- Horowitz, V. R., D. D. Awshalom, and S. Pennathur, “Optofluidics: Field orTechnique?” Lab on a Chip , 2008, 8: pp. 1856–1863.
- Bragheri, F., Osellame, R ;Ramponi, R , “Optofluidics for Biophotonic Applications” , IEEE Photonics Journal., vol.4 , no. 2, April 2012, 596 – 600.
- Psaltis, D., R. S. Quake, and C. Yang, “Developing optofluidic technology through the fusion of microfluidics and optics”, Nature 2006,442: p. 381.
- McDonald, J. C. et al. “Fabrication of microfluidic systems in polydimethylsiloxane, Electrophoresis 21, 27–40 (2000).
- David Erickson, David Sinton, DemetriPsaltis, ‘Optofluidics for energy applications’ , Nature Photonics 5, 583–590( Sept 2011).
- Monat.C, P.Domachuk, and B.J.Eggleton,“Integrated optofluidics:A©McGraw-Hill Global Education Holdings, Photon, 2007, 1(2): pp.106–114.
- Ronchi, V. Giovan Battista Amici’s contribution to the advances of optical microscopy. Physis 11, 520–533 (1969).
- Borra, E. F., “The liquid-mirror telescope as a viable astronomical tool,” Journal of the Royal Astronomical Society of Canada , 1982, 76:245 –256
- M. Oheim, “High-throughput microscopy must re-invent the microscope rather than speed up its functions,” British Journal ofPharmacology , vol.152, p. 1, 2007
- Haas, W. E. Liquid-crystal display research — the first 15 years. Mol. Cryst. Liq. Cryst. 94,1–31 (1983).
|