IndexTerms
|
Power quality, Harmonics, UPQC, Voltage Source Converter (VSC) |
INTRODUCTION
|
Power quality phenomena include all situations in which the supply voltage (voltage quality) or load current (current quality) waveforms deviate from the sinusoidal waveform at rated frequency with amplitude corresponding to peak value for all the phases for any three-phase system. In recent years, the term Power Quality (PQ) has gained significant importance, especially in electrical distribution side. As per international standards, the term power quality can be defined as the physical characteristics of the electrical supply provided under normal operating conditions that do not disrupt or disturb the user's processes. The disturbances in voltage (harmonics, sags, swells) may cause the tripping of sensitive electronic equipment which can lead to disastrous consequences in industrial plants, such as,unexpected results or a termination of the whole production line. These events are common in industrial sectors and cause high economical damage. In the above scenario, it is the source that disturbs the load/ sensitive equipment. To avoid heavy economical losses, the industrial customers often install mitigation devices/ equipment’s to protect their own plants from such kind of disturbances.The growing use of power electronics based equipment’s in modem plants is resulting in a load which is sensitive and harmonics producing in nature. Interestingly, this equipment’s generally produce distortion in currents and/or voltages. Thus, there is a new trend to install mitigating equipment’s that can serve the dual purpose, to both the utility as well as to the customer. Thus with the implementation of Custom Power Devices in the distribution side, Power Quality is enhanced. One of the most effective solutions to power quality issues in the distribution side is the installation of Unified Power Quality Conditioner (UPQC). UPQC is supported for alleviating all the voltage and current related problems (imbalances, Harmonics etc). Conventional UPQC [1] is constituted of two Voltage Source converters (VSC), an injection transformer and a common dc link as shown in Fig. l(a). The presence of injection transformer can create problems like offset due to energisation of transformers, increased losses in transformer windings and high cost of the system. Thus there is a need for a better injecting device. A DC isolation circuit was proposed in [4]. This implementation increases the complexity of the system along with the increase in the cost of the system. Thus, here in this paper, injection transformer as well as the DC isolation circuit is replaced with a series capacitor which acts as 'Voltage Injecting' source to the line. With the use of a series capacitor as injecting device [5], the cost and the complexity of the system is reduced and the system was found more efficient. |
The conventional UPQC can eliminate three phase faults alone. The system remains idle forsingle phase faults. The cross phase connected UPQC enables to overcome the problems related to single line faults [6]. The cross phase connection enables injection of voltage to a faulty phase from a healthy phase. The cross connection in phase is given at the load side as shown in Fig. l(b). Unlike conventional UPQC, here each phase is implemented with half bridge configuration VSCs and separate DC links for each phase. This configuration provides better control of each phase keeping the cost also minimal. |
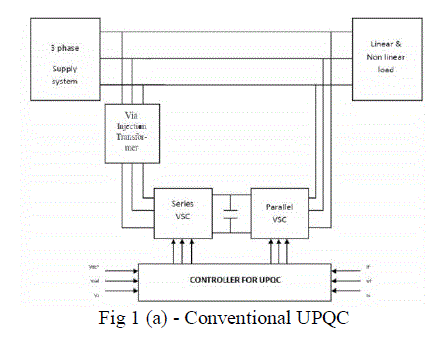 |
Control scheme of the proposed UPQC is also consideredhere in this paper. Various control strategies have beenproposed for UPQC. Some of them are PQ theory [7], wavelettransform [9], neural networks [10], fuzzy algorithm [11], Fourier transform theory [8], State feedback control law [2],power angle control (PAC) concept [13]. |
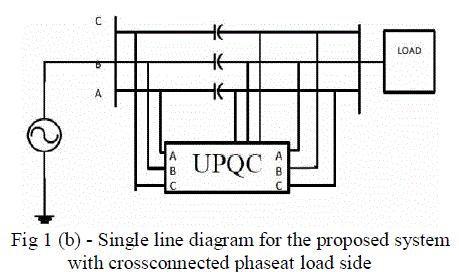 |
In this paper, the control strategy implemented is muchsimilar to DVRs. The control strategy of a transformer-lessDVR is discussed in [5]. The control is implemented basedupon the series capacitor voltage and the inductor currentfeedbacks. The design of the series capacitor and the inductorsare obtained from [15]. |
SYSTEM DESIGN
|
A. Basic System Design |
The basic circuit diagram of the proposed system is shownin Fig. 2. The series and shunt VSC is not the conventional fullbridge configuration. There are three UPQC modulescorresponding to each phase. Each module consists of twoVSCs in half bridges configuration and a split capacitor DClink. Out of the two halfbridges, one acts as the series VSCand other as Parallel VSC. The system is more efficientbecause of different DC link voltages corresponding todifferent phases. Whenever a fault occurs, the system restores immediately and more efficiently. The UPQC module for phaseA is shown in Fig 3. Unlike the conventional UPQC, here theability to eliminate faults occurring due to the single phasing isobtained. Cross phase connection enables the system toeliminate this fault. The elimination of single phase fault can be explained very well. The shunt VSC of the Phase C is connected to Phase A of the load terminal, when Phase C has asingle phase fault occurred. The current in Phase A is absorbedby the shunt VSC and the series VSC for phase C works. This enables injecting series voltage via the capacitor. Themagnitude and phase of the injected voltage in this case will besame as Phase C since the module corresponding to phase Cworks here. This advantage of the proposed system can widely used. |
B. Controller for Series VSC |
The main aim of the series VSC is to compensate for voltage imbalances. For any system, when there are imbalances, the voltage can be resolved into three components. The positive sequence will be always in phase with the supply system. The voltage equation with resolved components is as follows: |
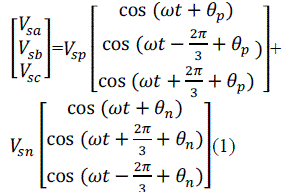 |
Here V and Vare the magnitude of the positive and negative components respectively. θ& are the phases angles of positive sequence component and negative sequence component respectively. |
The ωt and&thetaare extracted using the SPLL (software phase locked loop). The control signals for the series is provided as depicted in Fig 3.The design for the system is based on the control system analysis. |
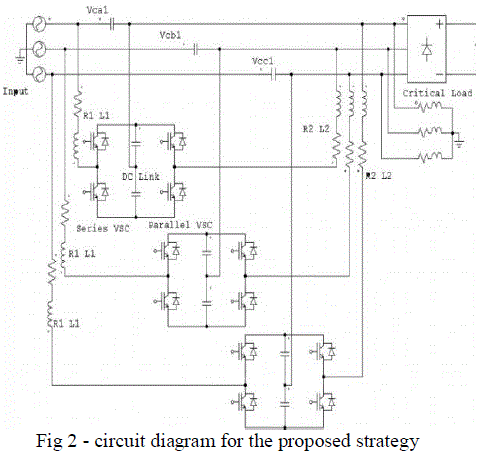 |
From the flowchart, we obtain control block diagram as shown in Fig. 4. The various parameters of the system are obtained by obtaining the overall closed loop transfer function and then performing stability analysis on the system. Based on the stability analysis results and selecting a desired damping ratio, the parameters are calculated. |
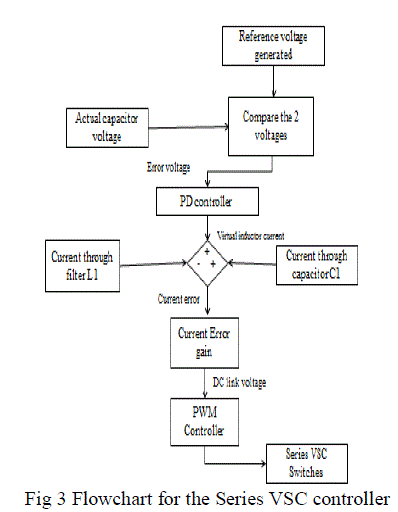 |
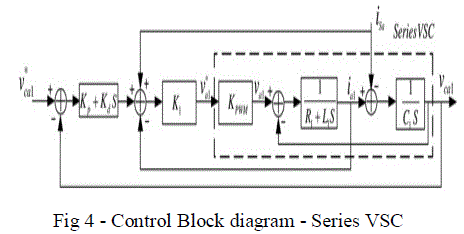 |
Here PWM controller is modeled as a unity gain system (Kpwm = 1). From the total transfer function of the system, V, which is the actual capacitor voltage, is obtained as in the equation below: |
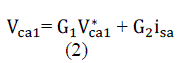 |
Where, Gare transfer function with input V (Capacitor Voltage calculated) and i(Source current) respectively. Thus transfer function Gwill consist of all the parameters K (Current Error gain), K(Proportional Gain of PD controller) and K& (Derivative gain of PD controller) From calculation, the values were found to beK= 25, K=26 &K& = 0.005. Thus the control system for series VSC was analyzed and the switching frequency of the IGBT switches of series UPQC used was 5 KHz. |
C. Controller For Parallel VSC |
The major concern for the parallel VSC is to compensate for unbalances and reactive power components of the load currents and reduce the harmonics in the current. Here a reference current is generated based on the power balance theory and instantaneous power theory. By applying power balance relationship & the theory of instantaneous active power and reactive power we obtain the reference current in a-ß reference frame. Here PLOSS is calculated as the power loss in the resistors through which UPQC module is connected to the lines.The reference current generation in abc reference frame is depicted in Fig 4 |
Thus the reference current generated in a-ß reference frame is transformed using Cmatrix which is as given below: |
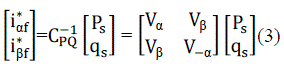 |
Where, the voltages Vα, Vβare given as below |
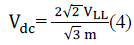 |
Vis the positive sequence component of supply. The reference current generated in a-ß reference frame is converted to abc reference frame. And we obtain currenti , i and i# for phases A, B and C phases respectively. |
The control block diagram of the parallel VSC is shown in Fig 6. From this control block diagram, we obtain the parameters K(Current error gain), K (Voltage error gain) by performing stability analysis on transfer function G . Here again PWM controller is modeled as Unity gain system (Kpwm = 1) |
The flowchart for the parallel VSC control is shown in Fig 5. The DC link reference voltage is calculated with the following formulae Where m= modulation index & here 'm' is chosen as 1). |
The four transfer functions for the system is obtained as below |
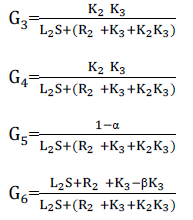 |
WhereG, . The values used here in this paper are K = 15, K= 10. |
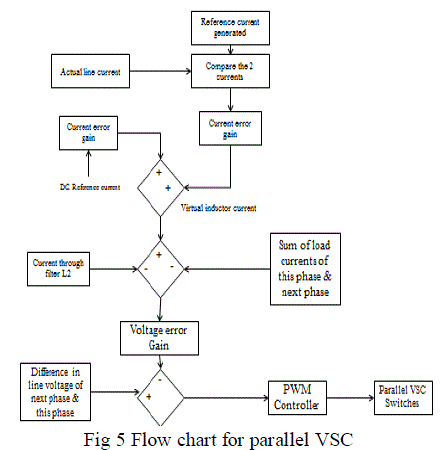 |
 |
III. SIMULATION RESULTS |
The scheme was verified using Matlab/SIMULINK 7.9.0 version. A supply voltage of 415 V, 50 Hz and the symmetrical load of 70KW was applied to the system. A harmonics load with an RL load (5Ω, 10 mH) is also switched to the system. The entire Simulink diagram is shown in Fig 7. |
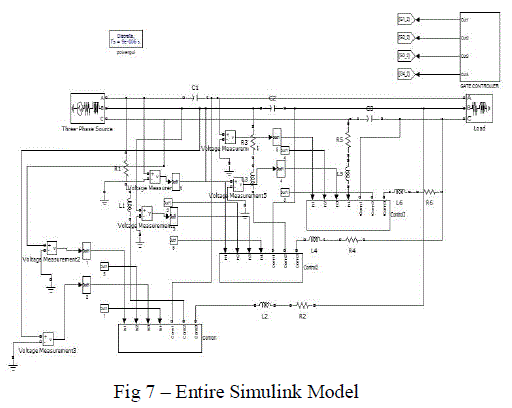 |
The system is analyzed with three phase symmetrical fault during 0.1 s to 0.2 s. At the time period from 0.3 s to 0.4 s, a harmonics load is switched to the system . The supply voltage and current waveforms without UPQC are as below in fig 8(a) and (b) below. |
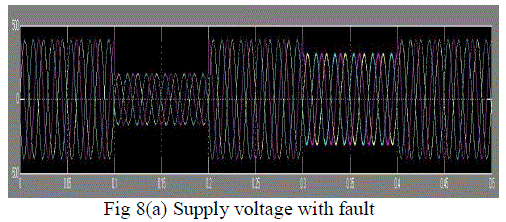 |
 |
With the implementation of proposed UPQC, the faults should be rectified. The output waveforms are represented in Fig 9(a) & 9(b). |
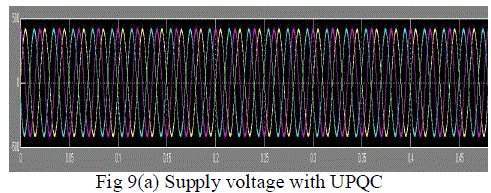 |
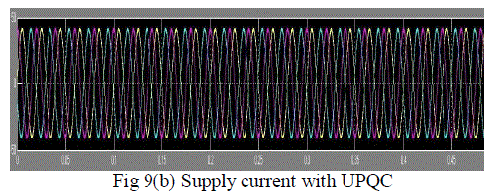 |
IV. CONCLUSION
|
The topology of a cross-phase-connected UPQC is introduced and two multi-loop control schemes are incorporated for the series and parallel VSC within the proposed UPQC. Extensive simulations are carried out to verify the practicability of the configuration and the effectiveness of the proposed control schemes under various operating conditions. It has been shown that the new control strategy for the UPQC is capable of protecting critical loads against voltage deviations, such as voltage imbalance, three-phase voltage sag/swell. Also, the UPQC with the proposed control can regulate the currents to be sinusoidal, balanced, and in phase with the positive phase sequence component of the supply voltage. |
References
|
- Ghosh, A, Jindal, AK., Joshi, A.: 'A unified power quality conditioner for voltage regulation of critical load bus'. IEEE Power Engineering Society General Meeting, 6-10 June 2004, vol. I, pp. 471-476
- Ghosh, Ledwich.G, Power Quality Enhancement Using Custom, Power Devices, Boston: Kluwer. lET Power Electron, Vol. 5, Iss. 5, pp. 600-608,2002.
- Hideaki Fujita, Hirofumi Akagi: 'The Unified Power Quality Conditioner: The Integration of Series- and Shunt-Active Filters'. IEEE Transactions On Power Electronics, Vol. 13, No. 2, March 1998
- Zhang, Y., Zhang, S., Chen, 1.: 'The applications of bidirectional fullbridge DC-DC isolated converter in UPQC'. Int.Conf.on Electrical Machines and Systems, 17-20 October 2008, pp. 1916-1921
- Choi.S.S, EngKian Kenneth Sng, MahindaVilathgamuwa.D, " Analysis of Series Compensation and DC-Link Voltage Controls of a Transformerless Self-Charging Dynamic Voltage Restorer', IEEE transactions on power delivery, vol. 19, no. 3, Pages 0885-8977, 2004.
- GJ. Li, F. Ma, S.S. Choi, x.P. Zhang, Control Strategy Of A Cross-phaseconnected Unified Power Quality Conditioner, IET Power Electron.,2012, Vol. 5, Iss. 5, pp. 600-608, doi: 10. I 049/iet-peI.20 I 1.0272
- Khadkikar, V., Chandra, A: 'A novel structure for threephase four-wire distribution system utilizing unified power quality conditioner (UPQC)'. In!.Conf.on Power Electronics, Drives and Energy Systems, 12-15 December 2006, pp. 1-6
- Kazemi, A, Mokhtarpour, A, TarafdarHaque, M.: 'A new control strategy for unified power quality conditioner (UPQC) in distribution systems'. 2006 Int. Conf.on Power System Technology, 22-26 October 2006, pp. 1-5
- Elnady, A., Goauda, A, Salama, M.M.A.: 'Unified power quality conditioner with a novel control algorithm based on wavelet transform'. Canadian Conf. on Electrical and Computer Engineering, 13-16 May 2001, vol. 2, pp. 1041-1045
- Tey, L.H., So, P.L., Chu, Y.c.: 'Neural network- controlled unified power quality conditioner for system harmonics compensation'. IEEE PES Transmission and Distribution Conf. and Exhibition 2002 Asia Pacific, 6-10 October 2002, vol. 2, pp. 1038-1043
- Singh, B.N., Chandra, H., AI-Haddad, K., Singh, B.: 'Fuzzy control algorithm for universal active filter'. Power Quality'98, 18 June 1998, pp.73-80
- Khadkikar, V., Chandra, A: 'A new control philosophy for a unified power quality conditioner (UPQC) to coordinate loadreactive power demand between shunt and series inverters', IEEE Trans. Power Deliv., 2008,23, (4),pp. 2522-2534
- Afonso, J.L., Freitas, MJ.S., Martins, J.S.: 'p-q theory power components calculations'. Proc. 2003 IEEE In!.Symp.on Industrial Electronics, 9-11 June 2003, vol. I, pp. 385-390
- Zhan, c.J., Fitzer, c.: 'Software phase-Iocked loop applied to dynamic voltage restorer (DVR)'. IEEE Power Eng. Soc.Winter Meeting, 2001, vol. 3, 28, pp. 1033-1038
- B. H. Li, S. S. Choi, and D. W. Vilathgamuwa, "Design considerations on the line-side filter used in the dynamic voltage restorer," Proc. Ins!. Elect. Eng., Gen.,Transm. Dist., vol. 148, no. I, pp. 1-7, Jan. 2001.
|