Fischer–Tropsch process (F-T) is an efficient technology to synthesize liquid transportation fuel as well as other valuable chemicals. This process is associated with hydrogenation of carbon monoxide gas in presence of transition metal catalyst to valuable liquid transportation fuels and chemicals. F-T reaction is essentially a catalytic process, and most widely used catalysts are either iron or cobalt based catalysts. Iron catalysts are preferred when substiochimetric syngas (with H2/CO molar ration is less than 2, also known as producer gas) is chosen as feed stock for F-T reaction. The deficiency of H2 in substiochimetric syngas can be met by water-gas shift reaction (WGS). Normally, cobalt catalyst is WGS inactive, and hence, is chosen for F-T reaction when feed stock is synthesis gas (with H2/CO molar ratio of 2 or higher). In this work, we have studied the F-T process using an industrial iron catalyst for synthesizing liquid transportation fuels at different processing conditions or reaction parameters. A fixed bed reactor was fabricated indigenously. The physical properties of the catalyst were studied by XRD, BET and TPR study, whereas the liquid product obtained from the F-T reaction was analysed by a GC using FID detector. Carbon monoxide conversions were calculated by analysing the reactor effluent by a GC using TCD detector. The experiments reveal synthesis of liquid F-T fuel at 300oC and GHSV of 1800 h-1. The composition of synthesized liquid F-T fuel (in terms of carbon number of hydrocarbons) falls within the range of conventional diesel fuel
Keywords |
Industrial Iron catalyst, FT synthesis, TPR, WGS |
INTRODUCTION |
Fischer–Tropsch reaction (F-T), which essentially is the synthesis of hydrocarbons from synthesis gas (CO + H2), was invented
in Germany in 1923. At present, the large scale implementation of FT process is done by SASOL and Shell for manufacturing of
transportation fuels and useful chemicals from syngas. FT synthesis is basically a catalytic reaction and the active and selective
catalysts for the FT reaction are mainly based on cobalt or iron [1-2]. Main products of the FT synthesis are linear paraffins and
a−olefins. The general reactions of FTS are summarized as follows: |
 |
The typical molar ratio requirement of H2/CO for F-T reaction is ~ 2, which is the composition of syngas. Syngas can be derived
from gasification of coal, biomass or steam reforming of natural gas. Conventional feed stock for FTS is natural gas; however, steams reforming of methane being an endothermic process, its energy requirements are excessively high that adversely affects
the process economy. Thus, producer gas from biomass gasification (with typical composition of 15% H2, 20% CO, 20% CO2,
5% CH4 and balance N2 [3-5] can form alternate feedstock to syngas for F-T reaction. However, utilization of biomass derived
producer gas (which is also termed by biosyngas by some authors) has its own limitations for F-T reaction. Major problem with
biosyngas is its sub–stoichiometric composition, in that the H2/CO molar ratio is 1. Therefore, F-T reaction with conventional
transition metal catalyst cannot use the biosyngas as feedstock. The deficiency of H2 in the biosyngas can be met through water
gas shift reaction (WGS). Iron based catalysts have received immense attention of researchers due to its water–gas shift activity
as well as easy availability and low cost. The carbon number of the product hydrocarbon (either chain or branched hydrocarbon)
is determined by the process conditions, viz. temperature, pressure and space velocity. Increase in temperature results in shifts
towards the product with lower carbon number. Several previous authors have described the effect of these parameters on the
yield and selectivity of the FT process. Dictor and Bel [6], Donnelly and Scatterfield [7] ,Mirzaei et al. [8] and Anderson [9]
have studied the effect of temperature on FT synthesis. They observed an increase of olefin to paraffin ratio in the product with
increasing reaction temperature for potassium promoted precipitated iron catalyst. Effect of total pressure on the product
selectivity on alkaline promoted iron catalyst has been reported by Dry [10]. Donnelly and Scatterfield [7] found that increasing
the H2/CO ratio in the reactor feed results in production of lighter hydrocarbon (with lower carbon number). The influence of the
space velocity (or in other words, residence time) of the synthesis gas on the selectivity has been investigated by Bukur et al.
[11]. Kuipers et al. [12] have investigated increase in the olefin to paraffin ratio with increasing space velocity (and hence,
resulting in decrease of the conversion due to smaller residence time) on a poly–crystalline cobalt foil. Similar studies have also
been done by Bukur et al. [11] on a commercial (Ruhrchemie) supported iron catalyst (Fe/Cu/K/SiO2), and Iglesia et al. [13] on
TiO2–supported ruthenium catalysts. Bukur et al. [11] have reported no effect of the space velocity on the molecular weight (i.e.
the carbon number) of the hydrocarbons, while Iglesia et al. [13] have observed an increase in the average molecular weight of
the products with decrease of the space velocity. The selectivity to methane and olefins has been reported to reduce with
decreasing space velocity, while the selectivity towards paraffins remains unchanged. In our earlier paper, on industrial cobalt
catalyst we reported the dependence of space velocity on the product profile. With higher space velocity, the interaction between
gas molecule and the catalyst particles is decreased, as a result of which higher selectivity towards short chain hydrocarbon are
observed [2]. A space velocity of 1800 h-1 was found to be optimum for liquid product towards diesel fraction.
In this study, we have attempted to synthesize liquid fuel by FT process using commercial iron catalyst using a fixed bed reactor.
Two experimental parameters, viz. temperature and gas hour space velocity (GHSV) of the process have been kept constant, as
the effect of these parameters on product distribution is well known. In this work, mainly synthesis of liquid hydrocarbons from
FT reaction has been studied at three different pressure levels, so as to deduce the change in product profile of FT fuel with this
parameter using an industrial iron catalyst. Such a study is also important for the best and effective use of iron catalyst for
production of liquid transportation fuel from syngas and it can also become a basis for optimization of FT process for bio-syngas. |
II. MATERIALS |
All gases used in experiments were procured from M/s Vadilal Gases Ltd. (Gujarat, India, purity: 99.999%). The gas cylinders
of reaction mixture (H2/CO = 67%/33% v/v) were connected to gas supply lines through two–stage high pressure regulator. The
analyses of the gaseous products in the reactor effluent were performed by an online gas chromatograph (Make: Thermo Fischer
Ceres 800 Plus system) using Porapack–Q column provided with a thermal conductivity detector (TCD). The liquids products
were analyzed by the same GC provided with a flame ionization detector (FID) using BP–10.5 column. For characterization of
gas chromatograph, hydrocarbon standards in the carbon number range of C5-C24 were procured from Sigma Aldrich. |
III. EXPERIMENTAL |
A. Catalyst source
Commercial grade iron based catalyst was used in experiments. It was procured from an industrial source and according to the
terms and conditions of the supplier the exact elemental composition of the catalyst cannot be disclosed. However, XRD, BET
and TPR study of the catalyst has been done in order to understand the active metal phase, surface and reduction property of the
catalyst, which is a prerequisite for any heterogeneous catalyst employed in reaction.
B. Catalyst Characterization
X–Ray Diffraction (XRD): Powder X–ray diffraction (XRD) measurements were performed using a Bruker Axs Company, D8
Advance diffractometer (Germany). Scans were taken with a 2 step size of 0.02 and a counting time of 1 s using Cu–K– radiation source generated at 40 kV and 30 mA. Data was collected over a 2 range from 20o to 70o, and phases were identified
by matching experimental patterns to entries in the JCPDF2.
BET Measurement: Brunauer–Emmett–Teller (BET) surface areas, pore volumes and average pore diameters were determined
by N2 physi–sorption at 77 K using a Beckman Coulter, Model: A53878. A 0.3 g catalyst sample was degassed at 300oC for 2 h
and then heated at 10oC/min to 300oC and held at this temperature for 2 h before analysis.
Temperature–programmed reduction (TPR): H2–TPR was performed using Micromeritics TPD/TPR 2720 system to determine
reducibility of the calcined iron catalysts. For H2–TPR, the catalysts (0.5 g) were reduced in a flow of 5% H2/Ar (30 cm3/min)
with a ramp rate of 10oC/min to 800oC. A thermal conductivity detector (TCD) was used to measure H2 consumption. The
detector output was calibrated based upon 100% reducibility of Ag2O powder, and a H2O trap was used to remove H2O
produced during the reduction. The degree of reduction of the catalyst was calculated as follows by using data from TPR [14]. |
 |
C. Experimental set–up: A schematic diagram of the reactor and its accessories is shown in Fig. 1. A fixed bed tubular reactor
(MOC: SS 316, thickness: 2 mm, ID: 6.35 mm or ¼ in.) was used for all reactions. The reactor had two gas supply lines of 6.35
mm (¼ in.) ID, each for purge gas (nitrogen) and synthesis gas (mixture of CO and H2). The synthesis gas supply line was
preheated with wrapped thermal tapes so as to the feed gas to 423 K. The reactor effluent line (ID 6.35 mm) was also heated in a
similar manner to 373 K to avoid any condensation of the product in the line prior to back–pressure regulator valve. Thereafter,
no thermal wrapping was given to the product lines, thus maintaining the temperature in them at ambient condition, where
higher hydrocarbon products can condense. The liquid product was collected in a trap (gas–liquid separator) kept at ambient
temperature. Cold water (at 298 K) was circulated in a jacket around the trap so as to achieve maximum possible condensation
of the hydrocarbon products. The lighter hydrocarbons and unreacted reactant gases are removed from the trap and purged
through a gas flow meter. The flow rate of feed synthesis gas was controlled using mass flow controller (Make: Eureka Ml Flow,
Range: 0–500 cm3/min). Catalyst (1 g) was placed inside the reactor enclosed between glass wool plugs. The catalyst was
reduced in situ at 673 K for 12 h under a stream of 50% H2 and N2 mixture (0.1 MPa pressure, 30 ml/min). After 12 h of
reduction, the temperature was reduced to 573 K under the constant flow of hydrogen. Synthesis gas was introduced at a
particular space velocity (GHSV), and pressure was gradually increased and set at the desired value. The temperature inside the
reactor was monitored using two thermocouples, one at the catalyst bed and other at the surface of reactor. Temperatures at
these locations were maintained constant by circulating cooling water through a thermal jacket (in the form of in. copper
tubing) wrapped around the reactor. |
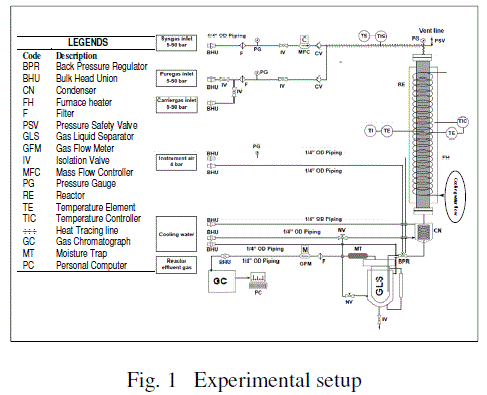 |
D. Analysis: The CO conversion (%) has been calculated according to the following equation: |
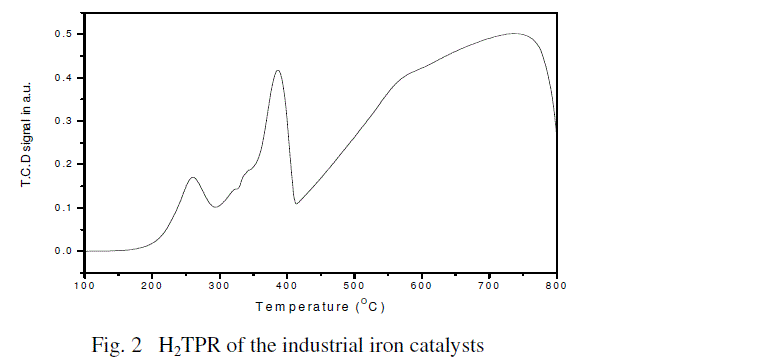 |
XRD analysis: The crystallinity and phase purity of the calcined catalyst was examined by powder X–ray diffraction (XRD). Fig.
3 shows the XRD patterns of industrial iron catalyst The pattern of the promoted calcined catalyst matches well with the
standard patterns of Iron oxide (JCPDS file no. 850987). All the peak pattern of the solid samples can be readily indexed to
Fe2O3, where the diffraction peaks at 2q values of 33.2, 54.2, 56.3 and 62.59° can be ascribed to the reflection of (1 2 1), (1 3 2),
(1 2 0) and (1 3 0) planes of the hexagonal Fe2O3 respectively. However, there are a number of unidentified weak intensity peaks
present in between the 2q range of 28 to 65o also present.
E. Effect of reaction pressure: F-T reaction is essentially a polymerization type reaction, in which the –CH2– units formed
from adsorbed CO and H2 reactant gases add up to form hydrocarbons of different chain length. Thus, as evident from reactions
R.1, the numbers of product moles in F-T reaction are less than reactant moles resulting in positive pressure–dependence, as per
Le Chatelier’s principle. An obvious consequence of these effects is that increase of reaction pressure also promotes the FTS
reaction, leading to an increase in the CO conversion. With increasing pressure, longer chain hydrocarbons are likely to form
that could possibly condense and saturate the catalyst pores by liquid product. To assess effect of reaction pressure on product
selectivity, we have carried out a series of reactions at reaction pressure range of 1 to 2 MPa using synthesis gas with molar ratio
of H2/CO as 2:1 and temperature of 593 ± 10 K. At each reaction pressure, the reduced catalyst was tested for 10 h. Fig. 4 shows
the GC data of the FT liquid product and the results are presented in the Fig. 5 for reaction pressures of 1, 1.5 and 2 MPa,
respectively, at GHSV of 1800 h–1. The overall CO conversion for each reaction was found to be 50-70% for pressure range of
1 - 2 MPa. It is clearly observed that with the increase in reaction pressure, there is an increase in the molar concentration of
each of the carbon number of the product, and also in the CO conversion efficiency. There is no change in overall product
profile, since there is no peak shift in three different pressures. The only change observed was an increase in the concentration of
the each of the hydrocarbon ranging from C7 - C20. However, the major selectivity was towards hydrocarbons of carbon number
range C9-C16, which is the hydrocarbon fraction of conventional diesel fuel. |
 |
V. CONCLUSION |
Present study has attempted to synthesize liquid hydrocarbons in the range of C9-C16 by FT process using commercial iron
catalyst for use as transportation fuel. The major reaction parameter was chosen as reaction pressure, whereas the residence time
was chosen from our earlier study of optimization of FT process using industrial cobalt catalyst. An intermediate GHSV of 1800
h-1 was selected to obtain product in the desired carbon number range (corresponding to liquid fuel). Faster GHSV than this
optimum value would give a gaseous product and a slower GHSV would give solid product. This will lead to additional storage
and transportation problem for gaseous FT product, whereas cracking of solid FT product would be necessary for use as
transportation fuel. This will severely affect the process economy. Increase in the pressure not only increases the % CO
conversion, but also the concentration of liquid hydrocarbons. Main goal of our experiments was to synthesize liquid FT fuel,
and hence selection of reaction or process parameters is very important. We observed that for liquid FT product temperature
below 300oC in not sufficient to produce liquid hydrocarbon, whereas temperature beyond 320oC is also not favourable as this
increases the selectivity of methane and other gaseous FT product at an expanse of liquid product. Thus, we strictly adhered to a
temperature of 300oC in order to synthesize liquid hydrocarbon that can directly be used as transportation fuel. Under the studied
condition of pressure, temperature and GHSV iron catalyst did not showed any severe change in the product profile. Thus, it can
be suggested from this study that with this iron catalyst even at lower pressure condition of 1 MPa fuels fraction similar to that
of conventional diesel can be synthesized. We believe that these results will be useful for design and optimization of a large
scale FT using the same catalyst. |
ACKNOWLEDGMENT |
The author wish to acknowledge Ministry of New and Renewable Energy (MNRE), Government of India for funding (vide
ref.19/20/2007–R&D/BE) of the project. Mr. Hanif A. Choudhury also acknowledges MNRE for financial support during this
research work through National Renewable Energy Fellowship. |
References |
- Alipio BC, David FC, Isabel RS, Juan CNM. Manuel AE. Comparison of batch, stirred flow chamber, and column experiments to study adsorption, Desorption and transport of carbofuran within two acidic soils. Chemosphere. 2012; 88(1): 106-120.
- Arnaud B, Richard C, Michel S. A comparison of five pesticides adsorption and Desorption processes in thirteen contrasting field soils. Chemosphere. 2005; 61(5): 668-676.
- Chunxian W, Jin-Jun W, Su-Zhi Z, Zhong-Ming Z. Adsorption and Desorption of Methiopyrsulfuron in Soils. Pedosphere. 2011; 21(3): 380-388.
- Chunxian W, Suzhi Z, Guo N, Zhongming Z, Jinjun W. Adsorption and Desorption of herbicide monosulfuron-ester in Chinese soils. J Environ Sci. 2011; 23(9): 1524-1532.
- Christine MFB, Josette MF. Adsorption-desorption and leaching of phenylurea herbicides on soils. Talanta. 1996; 43(10): 1793-1802.
|