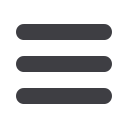
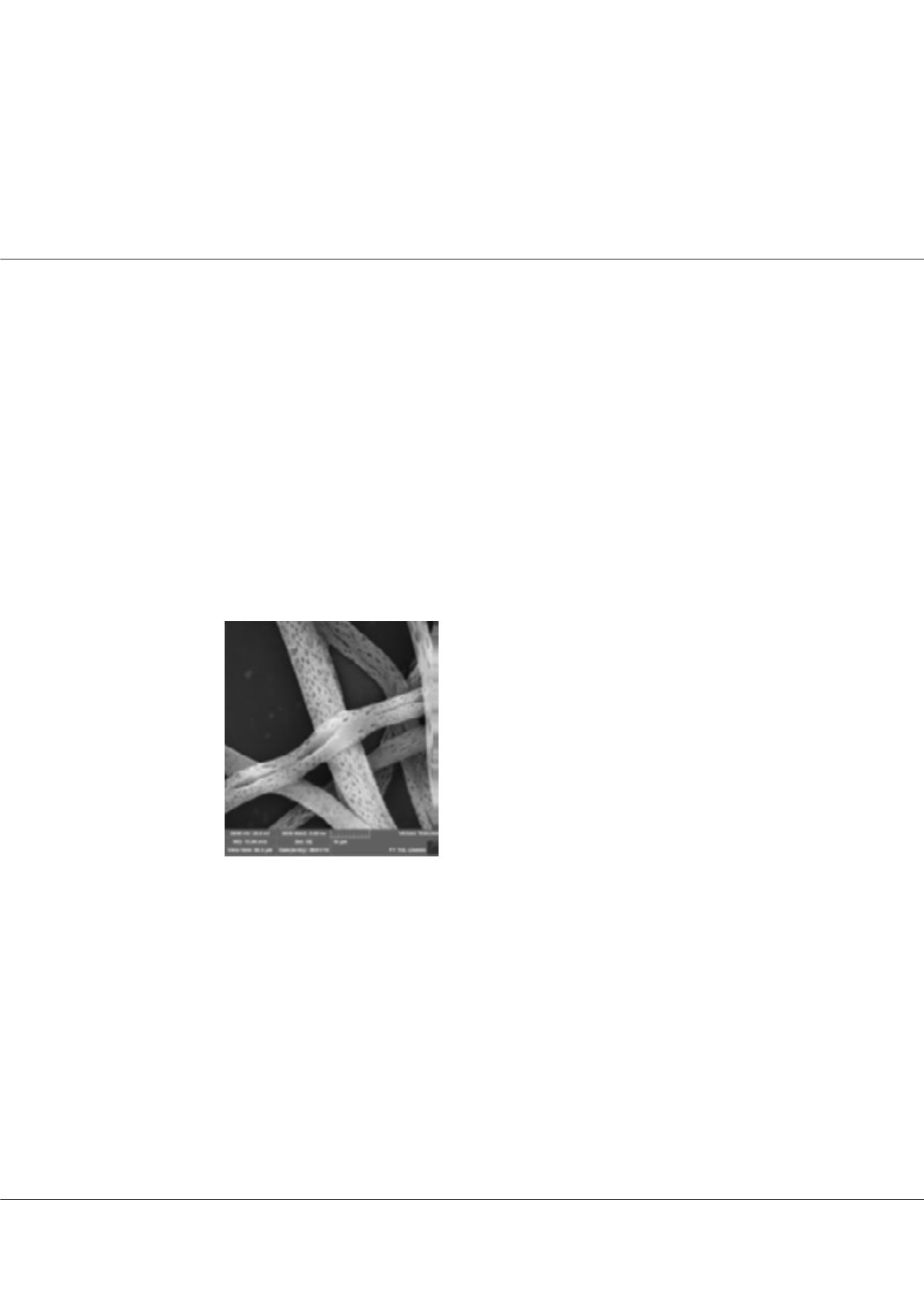
Page 96
Notes:
conferenceseries
.com
Volume 5, Issue 5
Res. Rev. J Mat. Sci. 2017
ISSN: 2321-6212
Advanced Materials 2017
September 07-08, 2017
September 07-08, 2017 | Edinburgh, Scotland
Advanced materials & Processing
11
th
International Conference on
Fibers made by centrifugal spinning technology
Jana Hlavata
and
Eva Kuzelova Kostakova
TU Liberec, Czech Republic
C
entrifugal spinning, Forcespinning¬TM or rotary jet spinning, all these names represent relatively new and simple technology
that allows production of fibers by using only centrifugal forces. These forces are caused by high-speed rotation of the spinneret
unit and are necessary for drawing polymeric jet and fiber formation. Two main ways of centrifugal spinning process depend on type
of the spinneret unit. These are needle and needle-less technology. Besides that, it is possible to combine centrifugal forces with electric
field to produce fibers by electro-centrifugal method. Fibers could be forming from solutions or melts as well. Centrifugal spinning
has several advantages in comparison to electrospinning such as spinnability of liquid form of materials (polymeric solution/melt,
ceramic, metal), larger range of spinnable materials (no requirements on conductivity of material) and higher production rate. Fibers
are arranged in one direction and gathered on collector. This homogenous fiber layer could be used in many different applications, I.e.
in biomedical area, tissue scaffolds, drug delivery systems, filtration, energy industry etc. Materials polycaprolactone (PCL), polyvinyl
butyral (PVB), polyamide 6 (PA 6), polyvinyl alcohol (PVA), copolymer of polycaprolactone and lactid acid (PLC), collagen and
other have previously been successfully spun. Forcespun fibers generally have wide distribution of their diameters. Big variability in
spinning devices, used materials and process conditions lead to production of modified fibers, such as porous fibers, bicomponent
fibers and even hybrid and inorganic fibers.
Biography
Jana Hlavata is Ph.D. student at Department of Nonwovens and Nanofibrous Materials, Faculty of Textile Engineering at Technical University of Liberec, Czech
Republic. She specializes in centrifugal spinning technology, especially in needle and needle-less way. Materials and modified fibers mentioned above have been
successfully spun at two devices assembled at department. These devices are improved and upgrade according to her specifications and requirements. During her
internship at University of Alabama at Birmingham she has been dealing with controlled morphology of porous fibers
jana.hlavata1@tul.czJana Hlavata et al., Res. Rev. J Mat. Sci. 2017, 5:5
DOI: 10.4172/2321-6212-C1-006
Figure1
SEM picture of porous fibers made from PCL
solution by needle-less way of centrifugal spinning
technology. Fibers were produced at Department of
Nonwovens and Nanofibrous Materials at Technical
University of Liberec. Scale is 10 μm.