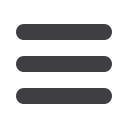
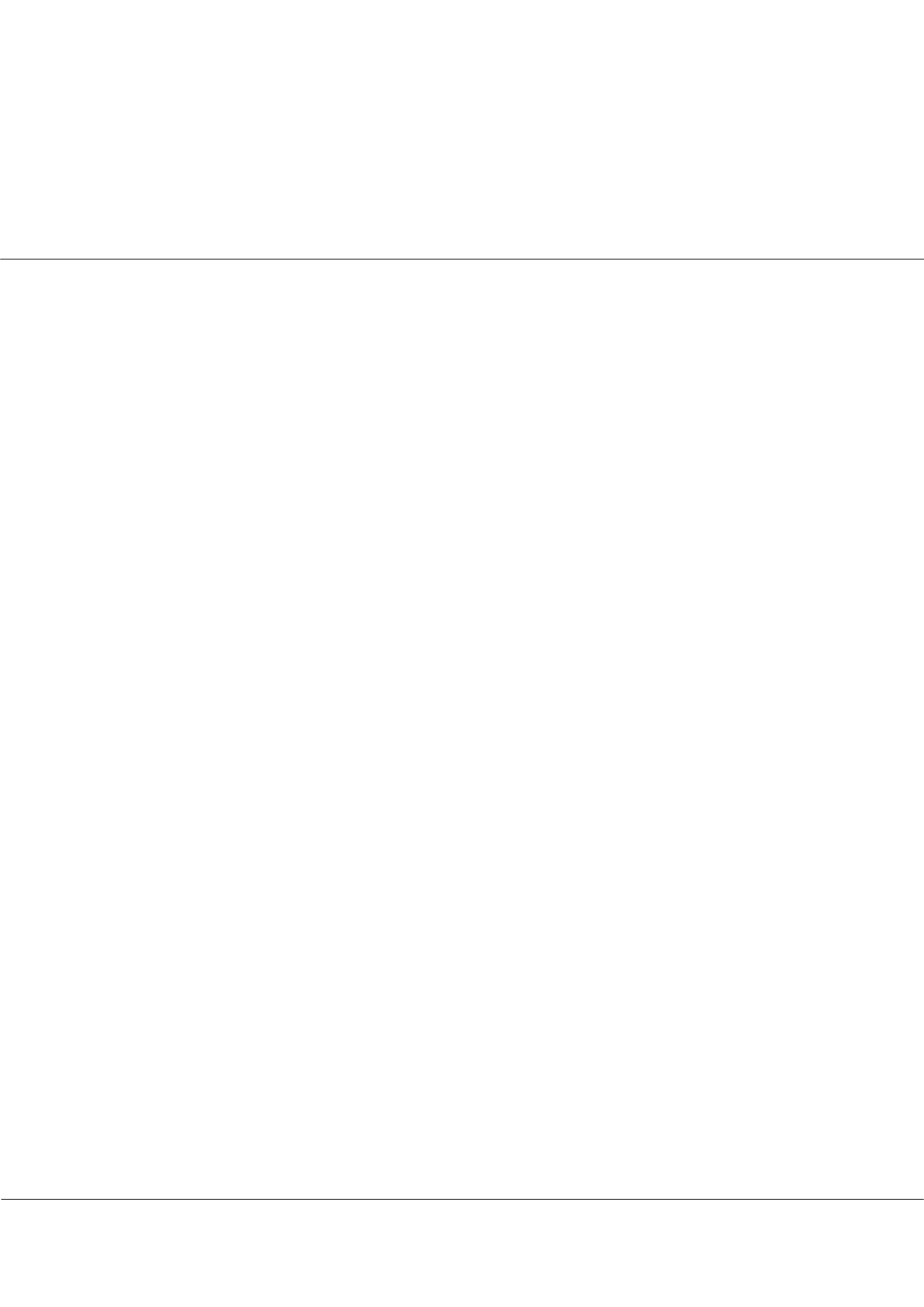
Page 76
conferenceseries
.com
Volume 6
Research & Reviews: Journal of Material Sciences
ISSN: 2321-6212
Materials Physics 2018
August 16-17, 2018
August 16-17, 2018 | London, UK
4
th
International Conference on
Condensed Matter and Materials Physics
Texture simulation of cold-rolled FCC metals by using Taylor model
Shih Chieh Hsiao
NCKU, Taiwan
T
he orientation of grains plays a significant role at the anisotropy of mechanical properties. In 1980s, Van Houtte proposed
the revised model, as known as the relaxed constrained Taylor model, to predict the experimental rolling texture of high
SFE metals. Until now, lot of researchers work on the evolution of the texture between experiment and simulation, but are
not able to simulate all the specific texture simultaneously, and the intensity of them are quite different as well. Thus, in this
research, we combined the full constraints and relaxed constraints Taylor models to predict the texture of severely cold-rolled
copper, and compare the difference of texture between experiment and simulation quantitatively. This study consists of cold-
rolling experiment and numerical simulation. In cold-rolling experiment, copper was rolled and measured by XRD and EBSD
to analyze the texture and microstructure respectively. In numerical simulation, statistical 10,000 orientations were imported
to the combined Taylor model to simulate the rolling texture measured by XRD. In experiment, the 95% cold-rolled copper
shows high Cu (16.2%), S (34.6%) and Bs (14.4%) orientations, which are the main components of rolling texture of high-
stacking-fault-energy metals. In simulation, the combined Taylor model successfully simulates high Cu (9.21%), S (23.24%)
and Bs (13.81%) orientations. The results are showed as {111} pole figure in figure 1, symbol
●,▲
and ■ stands for Cu, S and Bs
respectively. The combined Taylor model is able to predict the deformed texture. Not only the preferred orientations but also
the intensity are achieved.
sshawnnccatt@hotmail.comRes. Rev. J Mat. Sci. 2018, Volume 6
DOI: 10.4172/2321-6212-C2-018