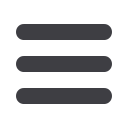
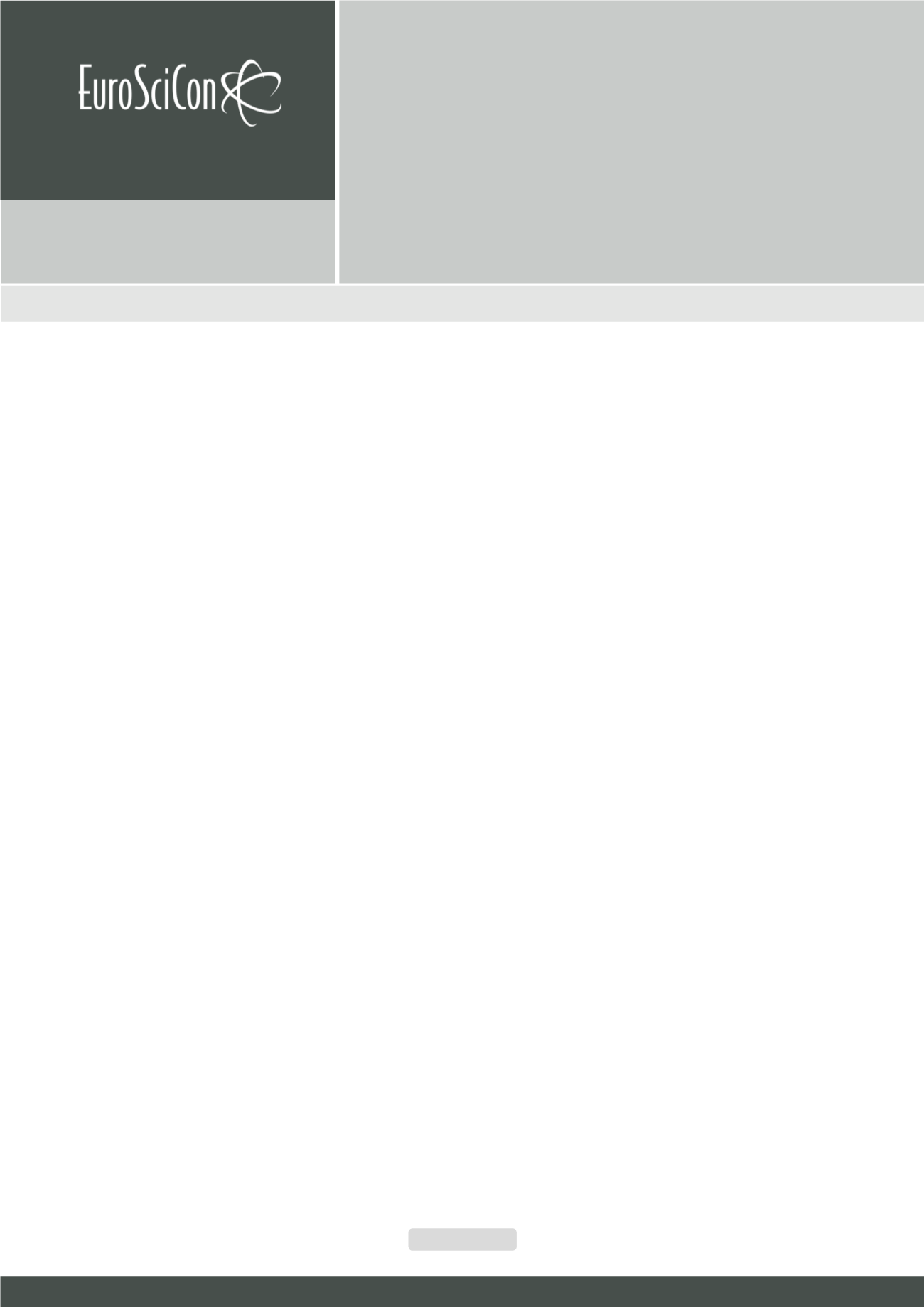
Page 56
Journal of Material Sciences
ISSN: 2321-6212
I n t e r n a t i o n a l C o n f e r e n c e o n
Metal, Mining and
Magnetic Materials
N o v e m b e r 0 1 - 0 2 , 2 0 1 8
P a r i s , F r a n c e
Metal and Magnetism 2018
Inductance matrix calculus of a non-uniform air gap motor
Jossana Ferreira
Federal University of Rio Grande do Norte, Brazil
T
he analysis and themodels of conventional polyphase inductionmachines are based on the uniformmagnetic field distribution
along the air gap. That characteristic leads to a symmetric inductance matrix which cannot be extended to non-uniform air
gap machines. Therefore, a variant and dynamic inductance matrix model is proposed in order to provide a more realistic model
to be applied in cases which the rotor eccentricity is significant such as bearing less machine or machine vibration and noise
analysis. This work is focused on the inductance calculus which means the stator and rotor self-inductances, stator mutual
inductances, rotor mutual inductances and the mutual inductances between windings of stator and rotor. The winding function
has been used to model the air gap function because it takes into consideration the winding distribution along the air gap. In
consequence of this approach, the graphics of mutual inductance between windings of stator and rotor vary vertically in function
of the air gap variance. This occurs due to the average value of the winding function is zero and only if the air gap is uniform.
The results showed that the interactions between the stator and rotor windings provide a mutual inductance variation up to 90%
by comparing the centralized rotor to a 40% variation of air gap and the self-inductances of the stator windings can result in a
variation up to 32% at the same conditions. The model has been used and validated in a bearing less machine problem and it has
presented satisfactory outcomes. Torque and speed measurements have been compared to the calculated amounts by using the
proposed model.
jossana@ect.ufrn.brJ Mat. Sci. 2018, Volume:6
DOI: 10.4172/2321-6212-C7-033