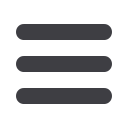
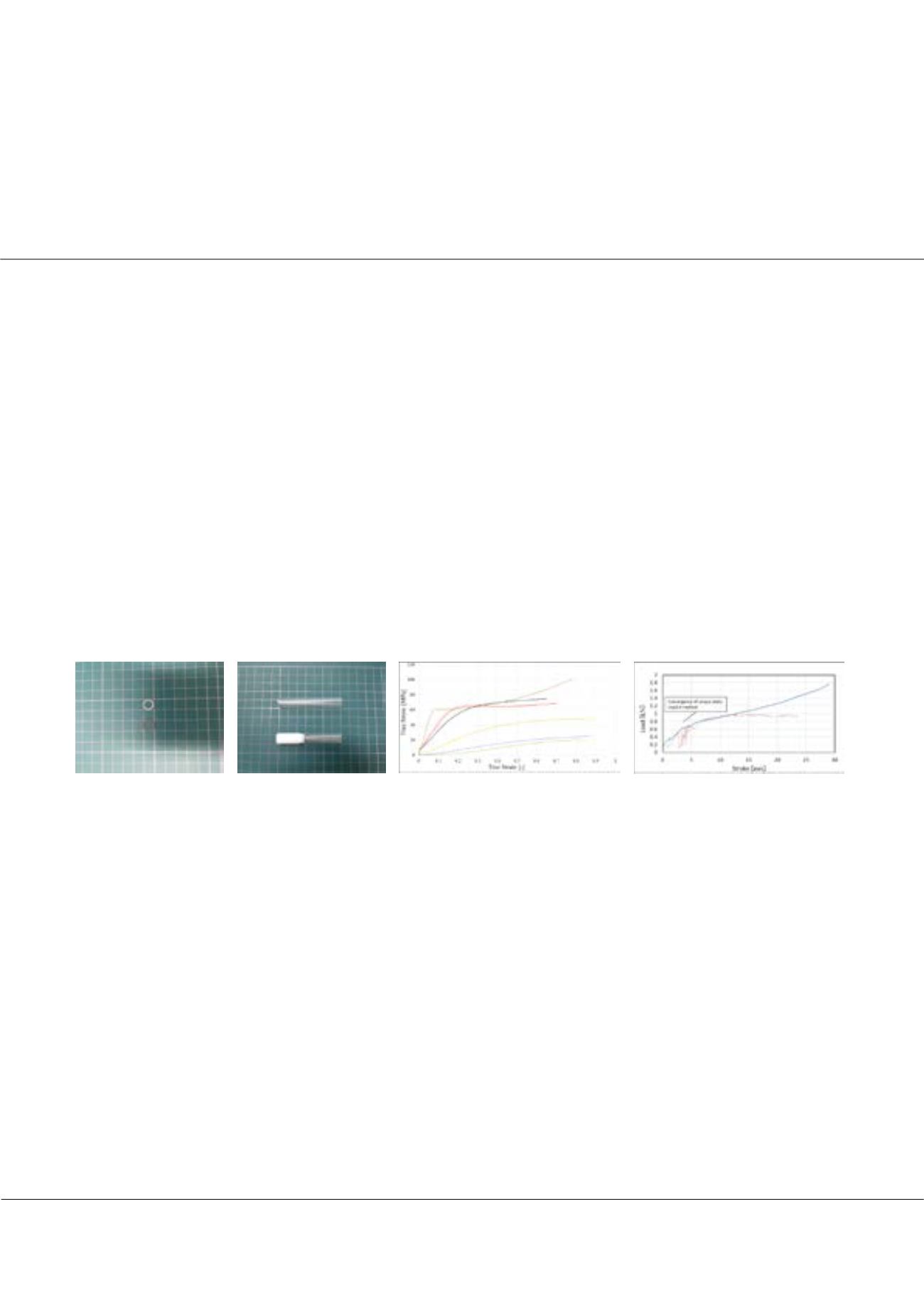
Page 104
conferenceseries
.com
Volume 6
Research & Reviews: Journal of Material Sciences
ISSN: 2321-6212
Advanced Materials 2018
September 04-06, 2018
September 04-06, 2018 | Zürich, Switzerland
21
st
International Conference on
Advanced Materials & Nanotechnology
Cold plastic forming of ABS plastic pipe: ABS plastic pipe
Kentaro Tsunoda
1
, Shinichi Nishida
1
, Junshi Ichikawa
1
, Yuta Kashitani
1
, Yuto, Horigome
1
, Naoki Ikeda
1
, Daichi Uematsu
1
, Makoto Hagiwara
1
, Hideto
Harada
1
and
Nobuyuki Kamei
2
1
Gunma University, Japan
2
DIP Inc., Japan
T
his paper describes about cold plastic forming of ABS plastic pipe. Experiment and Finite element method (FEM) analysis
of pipe expansion process were operated. The application of ABS plastic pipe for air conditioner is under consideration
instead of metal pipe in Japan because of weight saving of air conditioner for lowering the gravity point against earthquake.
The parts of ABS plastic pipe is generally produced by injection molding. The processes need the cooling time, and it takes
much time. In addition, expensive mold die is needed for each application. Thus, cold plastic forming of ABS plastic pipe
was proposed. The cold plastic forming of ABS plastic pipe chosen for this study is hardly studied by other authors. Product
ability of cold plastic forming is higher than the injection molding or hot working. And the punch and die shape is simple
comparing to these process. In this study, pipe expansion process was operated. The ABS plastic pipe has a 10 mm diameter
and 8mm inner diameter and 1 mm thickness. At first, true stress and true strain curves at any strain rate were measured by
ring compression test. Obtained flow stresses was used to FEM analysis. Experimental device for pipe expansion process was
made by Dip Inc.. Objective inner diameter was 10 mm. FEM analysis was operated to clarify the deformation behavior such
as load-stroke diagram. It was possible to produce the expanded ABS pipe. The whitening of worked pipe and strain recovery
was observed. Analysis result was indicated the good agreement comparing to experimental result in load-stroke diagram.
Fig.1
Ring compression test
Fig.2
ABS pipe
Fig.3
Flow curve
Fig.4
Load-stroke diagram
Recent Publications
1.
Ryosuke Okushima, Shinichi Nishida, Junshi Ichikawa, Yuta Kashitani, Yujiro Nitta, Atsuhiro Aoki, Yuto Takigawa, Hayato Aso,
Hideto Harada and Akihiro Watanabe, FEM Analysis of Cold Flaring Process of SGP Pipe, International Journal of Advanced
Engineering, Management and Science, Vol. 3 Issue 2, 75-76 (2017).
2.
Nao Ozawa, Shinichi Nishida, Toshio Haga, Junshi Ichikawa, Yuta Kashitani, Ryosuke Okushima, Yujiro Nitta, Atsuhiro Aoki,
Yuto Takigawa, Hayato Aso, Hideto Harada and AkihiroWatanabe, Forgeability of AZ Series MagnesiumAlloy produced by Twin
Roll Casting, International Journal of Advanced Engineering, Management and Science, Vol. 3 Issue 2, 77-80 (2017).
3.
Sueji Hirawatari, Hisaki Watari, Shinichi Nishida, Yuki Sato and Mayumi Suzuki, Evaluation of Friction Properties of Magnesium
Alloy during Hot Forging by Ring Compression Test, Materials Science Forum, Vol.889, 119-126 (2017).
4.
Y. Kamakoshi, S. Nishida, K. Kanbe and I. Shoji, Finite element method analysis of cold forging for deformation and densification
of Mo alloyed sintered steel, IOP Conference Series: Materials Science and Engineering, Vol.257, (2017).
5.
Shinichi Nishida, Junshi Ichikawa, Yuta Kashitani, Kentaro Tsunoda, Yusuke Takeuchi, Yujiro Nitta, Yuto Takigawa, Atsuhiro Aoki
and Yutaka Sato, FEM Analysis of Cold Flaring Process of SUS304 Pipe, Defect and Diffusion Forum, Vol.382, 120-126(2018).
Biography
Kentaro Tsunoda is pursuing his 4th undergraduate. He studied cold plastic forming of plastic pipe at Gunma University, Japan. He has done his research at the Faculty of
Mechanical engineering of the Gunma University. He has attended two conferences presenting his research works.
snishida@gunma-u.ac.jpKentaro Tsunoda et al., Res. Rev. J Mat. Sci. 2018, Volume 6
DOI: 10.4172/2321-6212-C3-020