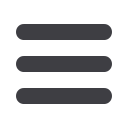
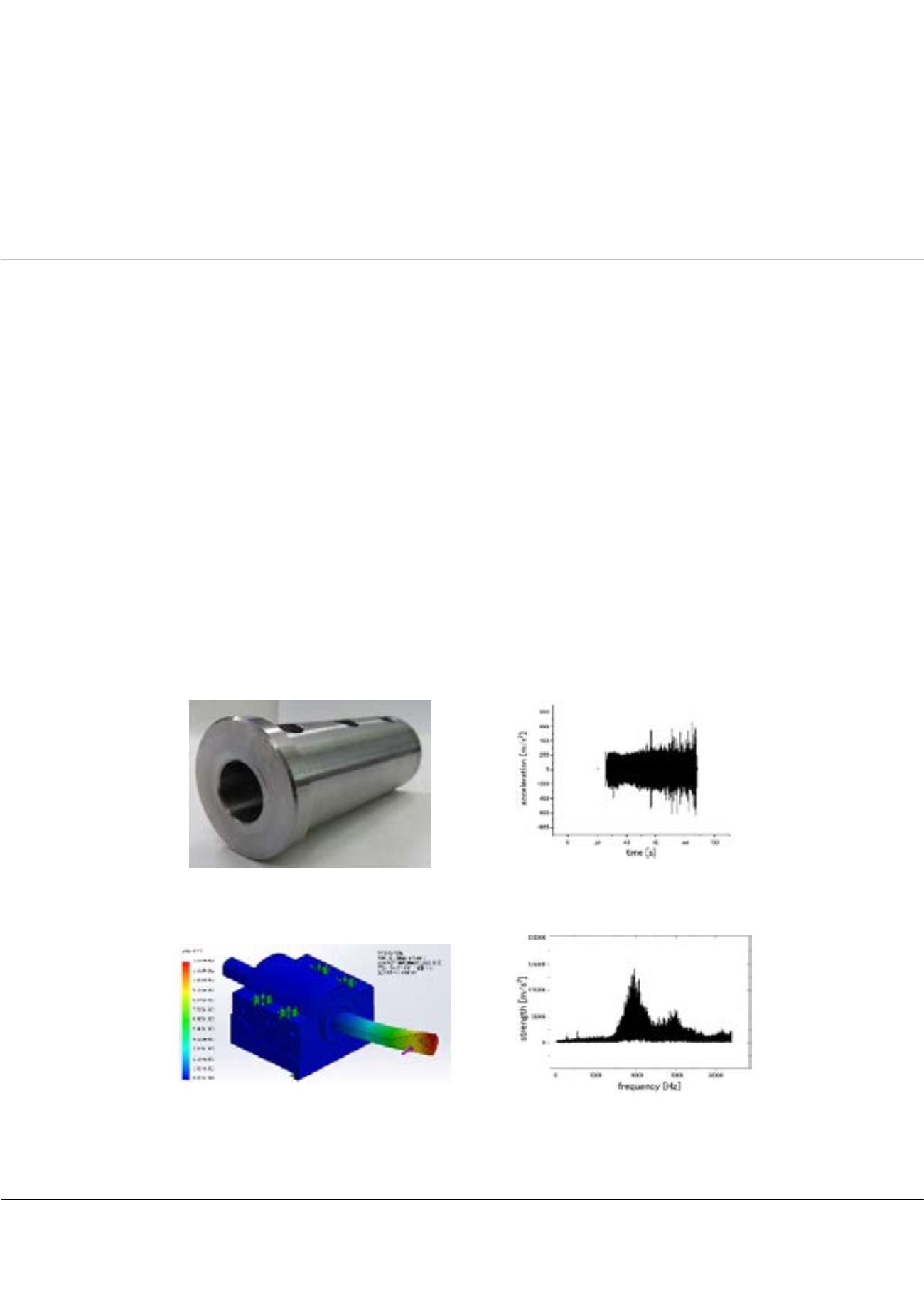
Page 106
conferenceseries
.com
Volume 6
Research & Reviews: Journal of Material Sciences
ISSN: 2321-6212
Advanced Materials 2018
September 04-06, 2018
September 04-06, 2018 | Zürich, Switzerland
21
st
International Conference on
Advanced Materials & Nanotechnology
Dynamic analyses of damping alloy sleeves for boring
Yuto Horigome
1
, Shinichi Nishida
1
and
Fumihito Sakurai
2
1
Gunma University, Japan
2
National Institute of Technology, Gunma College, Japan
T
he NC lathe is one of the major metal cutting machine tool. The overhang amount of the tool become large at boring with the
NC lathe. The tool vibration often become a problem at boring. The surface roughness and tool life are affected by the tool
vibration. Therefore, it is necessary to reduce the tool vibration at boring with NC lathe. In this study, the application of damping
alloy for the NC lathe sleeve was proposed. The characteristic of damping alloy is absorb vibration by transforming dynamic energy
of the vibration into heat energy. A cutting experiment was operated by using the new type sleeve made of only damping alloy and
the traditional type sleeve made of steel. The results such as vibration, surface roughness and tool life are compered between the
both tools. The tool vibration became small and the tool life became long with new type sleeve compared to the traditional type
sleeve. However the surface roughness became large by using new type sleeve. It is supposed that the rigid of new type sleeve is
smaller than that of traditional type sleeve. Therefore, the composite sleeve that was combined with damping alloy and steel was
developed for improving the rigidity. As a result, the tool vibration using the composite sleeve indicated one fifth and the surface
roughness became half compared to the steel sleeve. The vibration analysis based on this experimental results was studied to clarify
the vibration mechanism. The modal analysis was operated with the structural analysis software by using 3D models. And the FFT
analysis was operated by the vibration data. As a result, it was revealed that the natural frequency of cutting tool system with new
type sleeve was changed compared to the traditional system. And it was revealed that the bending mode frequency was closed to
the twist mode frequency.
Yuto Horigome et al., Res. Rev. J Mat. Sci. 2018, Volume 6
DOI: 10.4172/2321-6212-C3-020
Fig.1
The composite sleeve, the tool vibration of the composite sleeve, the modal analysis and the FFT analysis
(a) Composite sleeve
(c) Modal analysis
(b) Tool vibration of composite sleeve
(d) FFT analysis