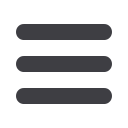
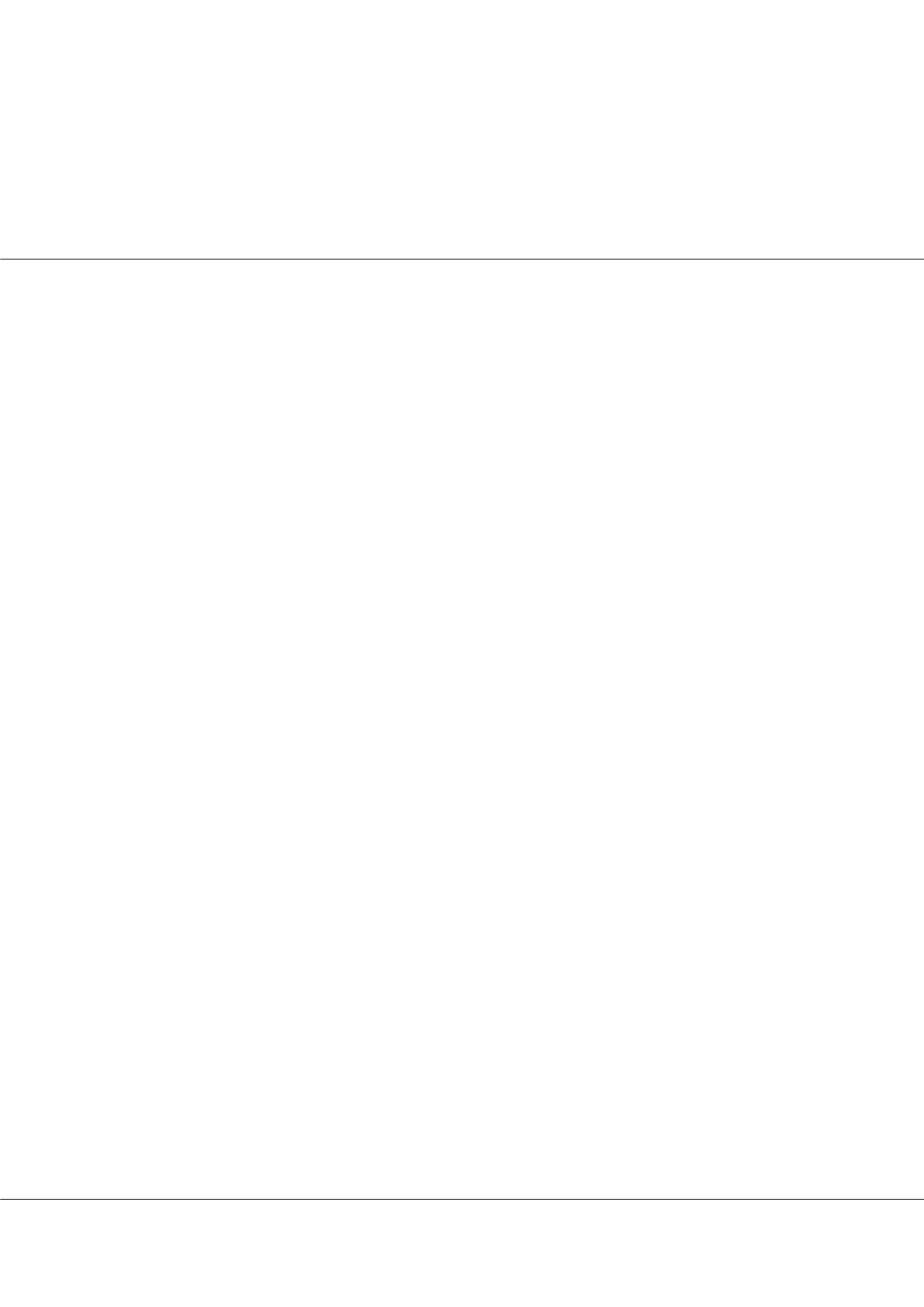
Page 79
Notes:
Research & Reviews: Journal of Material Sciences | ISSN: 2321-6212 | Volulme 6
November 07-08, 2018 | Atlanta, USA
Materials Science and Engineering
15
th
International Conference and Exhibition on
Applied Crystallography
3
rd
International Conference on
&
Study on uniaxial tensile and creep deformation of structural steel
Rajkumar Singh, Madhuri Thombre, Suraj Prakash Toppo
and
Sagar Bapat
Bharat Forge Ltd., India
C
reep resistant Ferritic-Martensitic steel is considered as a promising structural material for power plant applications. For
such steels, intensive research have been carried out in the scientific world to understand the high-temperature deformation
mechanism both through uniaxial Constant Strain Rate Test (CSRT) and Creep test at 0.3-0.5Tm. However, very few attempts were
made to correlate the effective stress of CSRT with actual creep rate. The present work is an attempt to establish a relationship between
these two. To characterize the stress exponent (n) and activation energy (Q) of F92 steel, experiments were carried out via Differential
Strain Rate Test (DSRT) and CSRT between strain rate range of (10
-5
-10
-3
s
-1
) and temperatures (400-700⁰C). The estimated (n) and
(Q) through CSRT were found to be 13 and 600kJ/mol, respectively. To rationalize high obtained values of n and Q, BMD model was
used and rationalized values came to be 5 and 236±20kJ/mol, respectively. The values of n and Q were also obtained directly from
DSRT and found to be 4±0.2 and 195±2kJ/mol, respectively, which are close to the values obtained from CSRT. These values reported
being associated with the climb of edge dislocation deformation mechanism. The CSRT results were further analyzed for identified
n≈4-6 to predict steady-state creep rate (έss) for corresponding effective stress (σ-σ
th
) which is reported to be responsible stress for
creep deformation and further validated by conducting creep test. Microstructural characterization of the samples was carried out
under TEM and the metallurgical factors identified affecting the results.
rajkumar.singh@bharatforge.comRes. Rev. J Mat. Sci. 2018, Volume 6
DOI: 10.4172/2321-6212-C8-036